Basic Concept of Package Dyeing Machine:
Package dyeing is a mature technology that is one of the most commonly used methods of yarn dyeing. It is a yarn coloration process. The other names for package dyeing is cop, cheese and cone dyeing. Package dyeing machine is a sophisticated apparatus that mainly used for yarn dyeing at high temperatures. Yarns wound onto perforated poly propylene tubes or stainless steel dye spring fit over perforated pipes in package dyeing machines called as high temperature and high pressure (HTHP) which are available in vertical or horizontal type of dyeing machines manufactured by Fong’s, Thies, Then, Cubotex and Dalal.
In package dyeing machines, the yarn is wound into suitable packages (e.g., cones, cheeses), mounted onto perforated spindles, and then dyed by forcing the dye liquor through the package. The earlier machines were atmospheric machines with unidirectional flow (into-out) of liquor through the package. Subsequent machine modifications were made to improve the levelness by enclosing the vessel and frequently reversing the direction of the liquor flow. Virtually all modern package dyeing machines are now pressurized and capable of operating at temperatures up to 135°C.
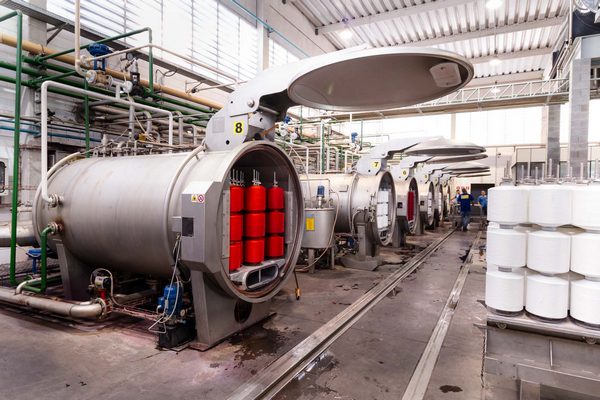
For dyeing, the yarn is wound on perforated stainless steel cones or cheese formers. The dyers prefer cheese form, as they tend to give level dyeing because of their uniform diameter. The success of package dyeing, in terms of both levelness and yarn quality, is greatly influenced by the degree of care taken in the preparation of the yarn packages. A wide range of designs and materials are being used to support the packages, such as perforated cones, springs, rockets, plastic tubes, and nonwoven fabrics, to name a few. With most stainless steel formers, cost can be a serious problem. Plastic formers are less expensive, but they have a shorter life and are heavy stained by certain dyes causing contamination. Nontextured nylon or polyester filaments are relaxed before winding on package formers, otherwise shrinkage during dyeing will cause damage to the yarn and crush the package former. The winding onto radially compressible formers is not very successful.
A vertical spindle machine, popularly known as H.T.H.P. package dyeing machine, is shown in Figure 2. The change from a rectangular to a circular shape allowed the vessels to be more readily pressurized for dyeing above 100°C.
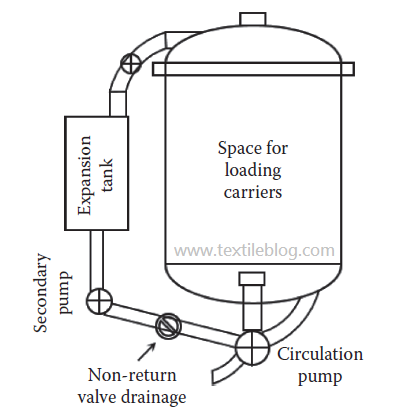
The pressure vessels are cylindrical with domed ends, the upper being the lid or the cover, which is securely locked by a series of bolts in older machines or by a sliding ring or similar quick-locking device. The lids of the large-diameter machines are heavy and therefore raised by pneumatically or hydraulically operated cylinders. The machine capacity may vary from 100 to 1000 kg. Machine diameters go up to just more than 2 m and the vessel height is usually similar. The overall height of the machine is increased by the pump fitted immediately below the main vessel. The height of the machine and the need to load it by an overhead travelling crane necessitates either plenty of headroom or setting the machine in a pit below the shop-floor level. Where the machines are mounted at ground level, a raised platform with surrounding safety rail is required. A 5-ton hoist is usually sufficient for a machine of 2-m diameter.
The cheeses, cones, or other packages are loaded onto perforated vertical spindles, which are then carefully placed in the package dyeing machine. The spindles are up to 125 cm long and usually circular in cross section (7 cm diameter), although some have a Y cross section to permit easier longitudinal flow of dye liquor. Larger diameter spindles favor level dyeing. The number of packages (cones/cheeses) per spindle is usually around 8–10. The column is pressed down firmly by mechanical devices and the end-cap is screwed tightly to complete the seal. Packages of hydrophilic fibers should be allowed time to wet out and swell before pressure is applied. As some textured yarn packages tend to shrink when wetted for the first time, it may be necessary to wet out the loaded packages for 5 min, and then additional packages are put into each column to maintain uniform permeability.
Compressing the packages lengthways not only provides a good seal but also tends to compact some areas of low density and high permeability, thus providing more uniform liquor flow along the column. Nontextured continuous-filament yarns are sometimes wound on rigid formers, which either interlock or are fitted with spacers to provide a seal against excessive liquor flow. Where high rates of liquor flow are required, long spindles could create pressure drop along the column. The spindles are screwed firmly into holes set in a frame called carrier with a circular hollow base and a center pillar with an eye at the top for lifting. At the center bottom of the carrier frame, there is an inlet for dye liquor; this inlet fits onto the pump discharge when the frame is lowered to the bottom of the dye vessel. There may be separate carriers for cones/cheeses, tops, and loose-stock as shown in Figure 3.
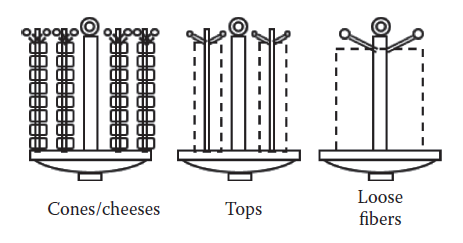
The cylindrical dyeing vessel is provided with a hinged lid, which, when closed, makes a pressure-resisting seal. Before the lid is clamped down, the carrier carrying the cones, cheeses, tops, or loose fibers is lowered into position; it rests on a seating, which is connected to the circulating pump below. The liquor is forced through the perforated pipe on which the packages are mounted. Under working conditions, the pressurized vessel must be filled with dye liquor. An overflow pipe is connected from the side of the vessel to the expansion tank so that extra dye liquor can be taken out of the vessel to accommodate for the increase in volume, which accompanies the rise in temperature. At the beginning, the flow should always be from outside to inside, and the flow could be reversed after a few minutes.
The machine is connected to a circulating pump. When the vessel is open to atmosphere, circulation is possible only from inside to outside, meaning that the liquor moves from the interior of the carrier through yarn package and comes into the vessel from where it returns to the pump. The circulation from outside to inside needs suction, which cannot be done successfully by the circulation pump. The penetration will obviously be better if the flow is reversed periodically. To have a two-way flow, the vessel must be closed and capable of withstanding pressure of up to 20 lb in–2. Developments in the package dyeing machines have resulted in improvements in pump design and spindle geometry, which benefits the circulation. The conventional machines have a flow rate of 30–45 L kg–1 min–1, with complete circulation every 30 s. The machines with a flow rate of 50–150 L kg–1 min–1, with a complete circulation every sixth second, are considered as rapid dyeing machines. These will allow the temperature to rise at a rate of 8°C–16°C min–1, as compared to 2°C–3°C min–1 in conventional machines. The main pump is fitted to the bottom of the vessel, usually as close to the center as possible to minimize frictional losses in flow.
For heating the liquor, conventionally, high-pressure steam is passed through horizontal coils located in the lower part of the vessel. A large surface area is thus available for heat exchange. The system is compact and heat loss is minimized.
In conventional package dyeing machines, the material-to-liquor ratio is around 1:10 when fully loaded. In partially flooded state, the liquor covers all the packages but does not fill the dome of the machines, causing reduction in the effective liquor ratio. Only in-to-out flow through the packages can, however, be used, and the packages must be sufficiently rigid to avoid distortion.
Types of Package Dyeing Machine:
Package dyeing machines may be of vertical or horizontal type ,and have one or many tubes acting as small dyeing vessels, each with a single individual spindle. Different types of package dyeing machines are
- Vertical kier dyeing machines
- Horizontal kier dyeing machines
- Tubular dyeing machines
Advantages of Package Dyeing Machine:
Package dyeing machines are widely used to dye yarns in package form. They allow for automatic and economical dyeing with accurate results. Advantages of package dyeing machine is point out below.
- Automatic control
- Uniform dye application
- High temperature dyeing a possibility.
- Low liquor ratios, giving savings in water, effluent and energy.
- Small lot sizes are common and possible using in package dyeing.
- Custom color and shade matching are possible due to the smaller lot sizes than dope dyeing.
- These factors make package dyeing good for flexibility and color development.
Disadvantages of Package Dyeing Machine:
- Color uniformity is difficult to achieve from lot to lot, creating waste or product variation.
- Colorfastness is not as good as solution dyeing, leading to bleeding or transfer of dye onto other materials during subsequent operations as well as shade changes during downstream processing.
- Fading and changes to color more likely from package-dyed yarns.
- Eight-step process has a longer lead time than solution-dyed yarn.
- Energy and water usage costs are very high for package-dyed yarn.
While package dyeing is adequate for most materials, thick, high twist yarns and threads may not allow for good dye penetration, and materials exposed to outdoor environments are likely to experience fading and shade changes.
References:
- Kiron, Mazharul Islam, “Package Dyeing Machine: Types, Working Principle and Advantages,” in Textile Learner, January 16, 2012, https://textilelearner.net/package-dyeing-machine-types-working-principle-and-advantages/.
- Textile and Clothing Design Technology Edited by Tom Cassidy and Parikshit Goswami
- Textile Dyeing By Dr. N. N. Mahapatra
- Control Systems in Textile Machines By G. Nagarajan and Dr. G. Ramakrishnan