Waste control is a major problem in the spinning industry. In a spinning industry, the input raw material is fiber from natural and man-made origin and the output material is a yarn. Therefore, there are wastes generated from fibers as well as yarns.
Many spinning industries are lacking standardized processes in place to manage the wastes generated. With the increasing concern of controlling waste to reduce environmental pollution, every textile industry is paying increased attention for the management of the waste. Furthermore, a proper waste management affects the quality, production efficiency, and profitability of the organization. Waste control approaches in spinning industry can help to achieve sustainability in addition to the approaches taken to achieve sustainability by optimizing the processes.
The approaches to waste control and management plays a significant role in increasing the production efficiency and maximizing profitability. Different types of machineries used to make the spinning waste usable or recyclable. A significant contribution was received from various spinning industries in Bangladesh in the form of quality images and feedback on the waste control and management.
Waste Control in Spinning Mills:
Different types of waste in spinning mills are shown in below table.
Section | Types of Waste |
Blow room |
|
Carding |
|
Comber |
|
Simplex |
|
Ring frame |
|
Winding |
|
Control of process waste in spinning mill are described with section wise:
Blow Room Waste:
The main objectives of blow room machines are the opening of fiber to small tuft, cleaning of fiber tuft, blending, and removal of microdust. Blow room section not only generating soft waste but also giving spinner a chance to reuse the soft waste in adequate proportion. Amount of waste extracted in blow room is mostly determined by the trash level in cotton.
The cleaning at blow room should always be considered along with the following things:
- The cleaning efficiency of blow room machines for, seed coats is much less than for leafy matter and sand dust taken together.
- The cleaning efficiency and waste increases as trash content increases.
- No aspect of yarn quality other than neps and foreign matter is influenced by the quality of blow room processing.
- An optimum level of opening is essential for cleaning of cotton.
The different types of blow room waste is depicted in Figure 1. Waste extracted in blow room is usually in the range of 2.5%–4.5% for cotton fiber and less than 0.5% for synthetic fibers. There are many factors influencing the waste generation at blow room section including speed and settings of beaters, exhaust suction pressure in pipeline, air current, and position of machines in blow room. In order to minimize the soft waste produced at various machines at blow room section, speed of beater should be monitored precisely because increased beater speed can not only cause harsh action on dedicated fiber but also increase the amount of soft waste generated.
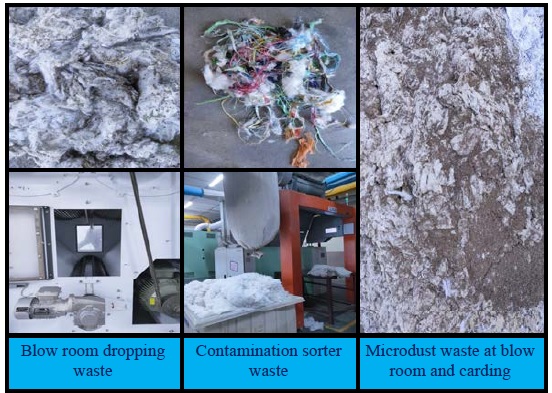
Improving cleaning efficiency and reducing waste at blow room:
To improve cleaning efficiency of beater, first examine the mechanical condition of machine, spikes on krischner beater, blades and fingers on bladed and porcupine openers and repair or replace as required. The inter grid bars space should be check for any chock up.
The waste is affected by changes such as:
- Distance between the grid bars and the angle of inclination of bars.
- Speed of beater.
- Fan speed in relation to the beater speed.
- Setting between feed rollers and beaters.
- Setting between beater and brid bars.
Carding Waste:
The carding process is used to individualize the fibers from the bunch of fibers and producing softly twisted rope-like structure called sliver. During the individualization, some of the fibers are released as waste and contribute to soft waste. The licker-in and cylinder droppings along with flats waste contribute the generation of soft waste at carding machine.
Waste extracted in cards is usually in the range of 4%–7%, depending upon the type of card and mixing. Between the same type of cards and mixing, the waste% should not vary more than 0.5% from the average. The card waste is also governed by the cleaning efficiency achieved in blow room. Thus, while assessing the waste, combined waste extracted in blow room and cards should be taken into account. The different types of carding waste and their extraction point on carding machine are shown in Figure 2.
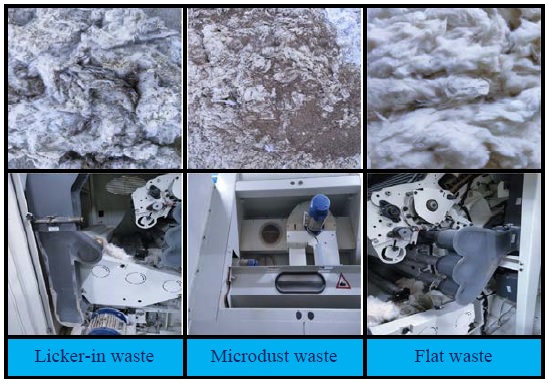
The behavior of waste and cleaning at cards depends on the following considerations:
- The total collected waste at card does not show any close relationship with the trash in the lap feed to the card.
- The cleaning efficiency achieved in mills is about 80% for most mixing. However, for fine and superfine mixing for which very high flat speed and low production rates are employed, a cleaning efficiency of 85% or more is achieved. The overall effect is that the lint loss in card waste will increases with decreasing trash content in lap.
- There is a tendency for the card to compensate for any lack of cleaning in blow room. The overall cleaning efficiency achieved in the blow room and the card taken together remains within a narrow range of 93–95%.
Controlling the waste at carding:
The following facts should be kept in mind while controlling the waste and cleaning at cards:
- Use of only one mote knife, placed slightly below the normal position of the top mote knife to give less waste and better cleaning in cotton mixing.
- Higher lickerin speed or greater wire point density on lickerin gives higher cleaning efficiency accompanied by some increase in the lint lost under the lickerin.
- Use of perforated undercasing helps in reducing waste.
- With other speeds and setting held constant, the flat strip waste varies almost proportionately with the flat speed.
- Wider front plate and back plate setting increases flat strip waste.
- For controlling cleaning of the card, almost the only place is the lickerin region.
- Card is excellent cleaning machine for seed coats especially the cylinderflat region which removes 80% of the seed coats.
- The tandem card gives 5–7% higher cleaning efficiency and better removal of seed coats.
Waste can be controlled by maintaining the correct setting in the licker-in zone and carding zone. The waste% to be removed in the carding process depends on the process and quality requirements of the product. Cylinder to cylinder undercasing setting influences air currents and leads to fly generation, and too wide setting causes the loss of fibers. Closer setting of licker-in to licker-in undercasing increases the good fiber loss with waste. If the setting between the feed plate and licker-in is too close, more lint loss will occur, and it will increase the waste%. The speed of the flat is also directly related to the amount of waste removed in the form of flat strips; that is, the higher the flat speed, the heavier the flat strips.
Waste in Draw Frame:
The objectives of draw frame include attenuation of sliver, removal of hooks, fiber blending, and reducing yarn unevenness through doubling. Soft waste is generated at both breaker and finisher draw frame including broken sliver ends; fiber fly is generated at high-speed drawing and unutilized sliver parts at the end of the batch which contributes the major portion of soft waste generated at draw frame. However, some points which help in minimizing soft waste at draw frame include adequate drafting rollers and calendar roller pressure to avoid frequent end breakages, spring pressure, amount of pretension in sliver at creel section and delivery side while processing combed cotton.
Comber Waste:
The combing process has been carried out in order to improve the quality of the carded sliver by eliminating short fibers, parallelizing fibers, straightening hooked fibers, and removing neps. Combing process removes very high amount of short fibers in the form of noil and that can be reused to some extent again at blow room section or for coarse count open-end yarns. Combed slivers due to low inter fiber cohesion have more chances of failure when compared with carded slivers and generate more amount of sliver waste. The total waste extracted during combing is usually in the range of 15%–20%, depending upon count and customer requirement in terms of IPI, RKM, and hairiness (Fig. 3.3).
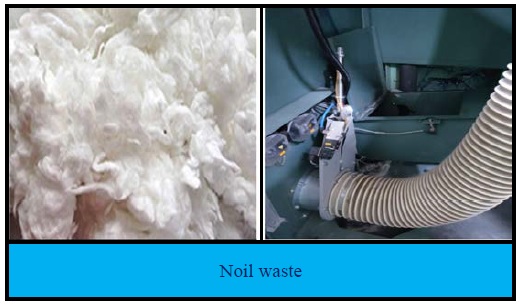
Obviously, combing is not required for man made fibers as they are free from short fibers and foreign matter. A higher % of comber waste need not always means that better removal of short fibres and neps, and therefore may not always be advantageous either for yarn quality or performance beyond a certain level.
Technological consideration:
For an effective removal of short fibers, retention of long fibers and removal of neps, the following considerations are of up-most importance:
- The card trailing hooks are longer and more numerous than the leading hooks. They are removed when fed as leading hooks by keeping an even number of reversals between the cards and the comber.
- The waste at comber can be reduced by increasing pre-comber draft without affecting the resultant yarn quality. However, a high comber draft also results in extremely low inter fibre cohesion causing excessive lap linking, frequent sliver breaks at comber, draw frame and the can feed inter creel. Therefore, a pre-comber draft of 30–40 for counts upto 40s is adequate. Pre-comber draft of above 20 is suitable only for very long staple cottons.
- The proper place for controlling neps is carding and no combing. It is often more economical to run cards at somewhat low production rate than to take out extra comber waste.
The waste at comber needs to check and controlling due to the following reasons:
- More waste other than the nominal means financial loss.
- Less waste other than the nominal could lead to unacceptable yarn quality and performance.
- Comber waste variation could contribute to lea count variation.
Simplex / Roving Frame Waste:
Simplex is an intermediate process in which sliver is converted into low twist material called roving. The sliver which is taken from draw frame is thicker so it is not suitable for manufacturing of yarn. The sliver is drafted many times from its original length during roving frame process and little amount of twist is inserted to it to improve the strength of roving. This roving is wound on to the large packages. These packages are used as input material during ring frame process. During the processing of sliver to roving, sometime breakage is happening either of sliver or roving which gives the generation of soft waste around 0.5%. The roving waste can be used after removing from the bobbin and a preopening is required on the machine available for the purpose.
Ring Frame Waste:
At many stages of spinning process waste is removed to clear the cotton or to separate the short fibers but at the stage of ring spinning there is no need to remove waste. This step is exclusively for drafting twisting and packing the yarn in the shape of bobbin. Whatsoever material is wasted here is because of our inability to control the machine, process or processing condition. Thus to control the waste we have to control all factors.
Higher bonda waste percentage is mainly due to higher end breakage rates during spinning which depends on mechanical condition of ring frame and the quality of the material fed. Further, the amount of this waste depends on the number of spindles allotted to a tender, the number of rounds the tender takes over the spindle, and the quality of the roving feed. In practice, reducing pneumafil waste forms a regular feature of the process control activity in a mill. The different types of ring frame waste are depicted in Fig. 3.4.
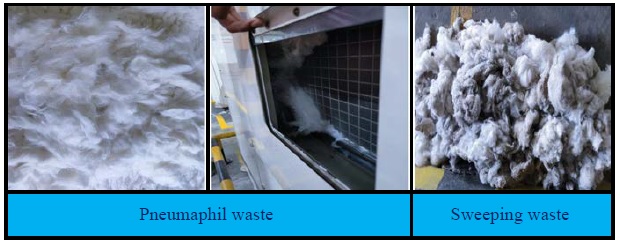
Factors responsible for waste generation in ring frame:
- Yarn breakage rate.
- Time taken in attending to the yarn breakage.
- Working practice and culture.
- Housekeeping and material handling.
- Mechanical breakdown and failures.
- Methods of attending to the break downs.
Waste control in ring frame:
This is done in the following steps:
- Analysis and segregation of the waste of different types.
- Weigh that waste and recording that section wise, person wise, shift wise.
- Comparison with the standards.
- Feed backs and action to improve waste generation.
Control of Hard Waste:
Waste generated in the yarn manufacturing process can be classified into soft waste and hard waste. Reusable wastes such as sliver, lap bits, roving ends, and pneumafil waste are normally termed as soft waste. Yarn waste obtained from ring frame and winding department is not reusable, hence it is called as hard waste. The occurrence of hard waste must be controlled as it affects the productivity of the spinning mill. Hard waste generation in winding department must be less than 1%. The hard waste collection at winding machine is shown in Fig. 3.5.
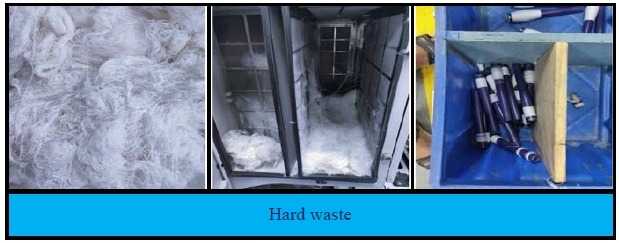
The various causes of hard waste generation are:
- Over end piecing of yarns while attending end breakage during doffing
- Control of end breakage immediately after doffing
- Reducing the cop rejection % in winding
- Adopting proper material handling procedures
- Proper work practices in ring frame and winding
In many spinning mills, there is good scope for improving yarn realization and reducing wastes. Because in the spinning mill wastes are generated in more amount and it can be controllable and reducible at some extent.
Various measures that can be taken to reduce hard waste are as follows:
- Improve the quality of cops by reducing defects like ring cuts, over filled cops, double gaiting, etc.
- Maintain the number of under wound coils on the cop at below 5.
- Ensure a high cop content for the given package size.
- Avoid using damaged cops in ring frames.
- Maintain the number of clearer cuts at below 80 per one-lakh meters for single yarn and 30 per one-lakh meters in doubled yarn in automatic cone winding.
- Maintain the machinery in good condition.
- Train the workers for correct work methods.
- Ensure that cop rejection does not exceed 5%.
- Control the “repeaters” at below 10%.
- Allow only minimum amount of yarn in the suction while feeding full cops in the magazine.
- Avoid removing remnants on the cops using knife.
- Maintain proper records for hard waste.
References:
- Waste Management in the Fashion and Textile Industries Edited by Rajkishore Nayak & Asis Patnaik
- Pollution Control in Textile Industry By S. C. Bhatia
- Sustainable Technologies for Fashion and Textiles Edited by Rajkishore Nayak
- Process Management in Spinning by R. Senthil Kumar
- Process Control and Yarn Quality in Spinning By G. Thilagavathi, and T. Karthik
You may also like:
- Comber Machine and Combing Process | Advantages of Combing Process
- Comber Machine Production Calculation
- List of Spinning Machines with Manufacturers Name
- Recent Development of Carding Machine in Yarn Spinning