What is Textile Yarn?
A textile yarn may be defined as a long fine fiber strand of parallel continuous filaments or twisted staple fibers or material in a form suitable for knitting, weaving, or otherwise intertwining to form a textile fabric. Most fabrics are made from yarns that have been created from fibers twisted together or laid side by side. The fibers may be natural, manufactured, or a combination of both. Because of the many yarns available today, you can choose from fabrics that vary greatly in design, texture, and performance.
You may also like: What is Yarn?
Yarn occurs in the following forms:
- A number of fibers twisted together (spun yarn);
- A number of filaments laid together without twist (a zero-twist yarn);
- A number of filaments laid together with a degree of twist;
- A single filament with or without twist (a monofilament); or
- A narrow strip of material, such as paper, plastic film, or metal foil, with or without twist, intended for use in a textile construction.
Yarn Specifications and Quality Parameters:
In practice, yarns can be described by many specifications depending on the desired yarn performance during weaving or knitting, fabric type and fabric construction, and end-product performance. Figure 1 illustrates different types of yarn specifications. Almost all yarn specifications will involve yarn type, count, and twist. In addition, other specifications may be stated depending on the fabric-forming system used and the intended application or end product. These include yarn bulk integrity described by physical or mechanical parameters such as strength, elongation, toughness, and flexibility and yarn surface integrity described by yarn hairiness, abrasion resistance, friction, and roughness. For technical fibrous products, yarn types may also be specified in terms of special treatments such as hydrophilic finish, hydrophobic finish, flame-retardant finish, resin treatment, and enzyme treatment.
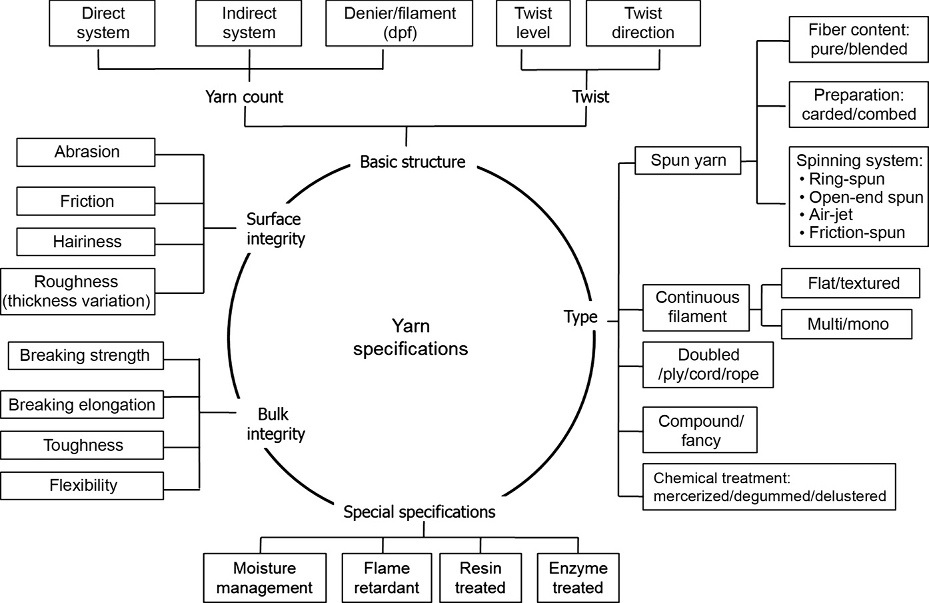
Specifications and parameters of yarn are mentioned below:
1. Yarn Type:
Normally, the first specification is yarn type. Any yarn type must be associated with the fiber type used or fiber content. This may be 100% of a single fiber type (e.g., 100% cotton or 100% wool) or a blend of two or more fiber types (e.g., 50% cotton/50% polyester yarn). Yarns may also be made of multiple structures such as ply, cords, ropes, compound, and fancy yarns. Yarn type may also be specified by some desired chemical treatments such as mercerization and slack mercerization in the case of cotton yarns, shrink resistance for wool yarns, degumming of silk yarns, delustering of synthetic yarns, and texturing of continuous-filament yarns.
2. Yarn Count or Linear Density of Yarn:
Ideally, yarn count, also known as yarn size or yarn fineness, should be described by yarn diameter or thickness. In general, linear density is defined as the mass per unit length of a fiber, sliver, or yarn. In case of spun yarns, two systems of linear density (or yarn count) are commonly used: the direct system, which is based on weight per unit length, and the indirect system, which is based on length per unit weight.
- Direct system: Denier, Tex (Weight of Unit Length)
- Indirect System: (Units of Lengths) per (Units of weights)
3. Yarn Appearance:
The Visual Effect obtained by viewing a sample of yarn wound with a designated traverse on a black board of designated size.
- Nep: A tightly tangled mass of unorganized fiber
- Slub: An abruptly thickened place of yarn
- Thick place: A yarn defect where the diameter is greater than the adjoining segments and extending for 6 mm
- Thin Place: A yarn segment where the diameter is 25% lesser than the average diameter of yarn
- Fuzz: Untangled fibers that protrude from the surface of the yarn
- Bunch: A yarn segment not over 6 mm in length that shows abrupt increase in diameter caused by more fibers matted in this particular place
- Method: Yarn wound on hylam black boards wound for fixed wraps per inch as per count compared with standard reference boards.
- Grades: Above ‘A’ to below ‘D’ – The imperfections increase from Grade ‘A’ and the maximum in grade ‘D’. Average index of five boards of five graders.
4. Yarn Evenness:
- Unevenness: Variation in the linear density of a continuous strand or of a portion of a strand.
- Apparatus: Uster–Evenness Tester
- Principle: Difference in the capacitance variation. Lower the Count lower the Imperfections. One km of yarn is run through two capacitance plated at specific speed (fixed as per the count). The capacitance variation is integrated and expressed as % unevenness (U %). The imperfections are counted and are reported per kilometer.
5. Count Test:
Apparatus:
- Wrap reel
- Balance
120 yards of yarn / 100 meters of yarn wound in a wrap reel and weighed. From the weight, the count is calculated.
6. Single Thread Strength Testing:
Force required breaking a single strand of yarn of unit length
Apparatus:
- Single thread Strength Tester
7. Lea Strength Testing:
- Lea Breaking Strength
- The Force required to break one lea
- Unit –pounds
- Count Strength Product
- Apparatus –Lea Tester
8. Principles of Tensile Testing:
- Constant Rate of Loading: The Rate of change of Load is constant – Uster Dynamat
- Constant rate of Traverse: The pulling clamp moves at a constant rate – Lea – Pendulum tester
- Constant rate of Extension: Rate Of change of Specimen length is constant – Statmat
9. Yarn Twist:
Twisting is a mechanism used to consolidate fibers into yarns and provide yarn strength. Yarn twist is typically described using two parameters: twist level and twist direction. Twist level is commonly expressed by the number of turns of twist per unit length. Another way to express twist level is by using the twist multiplier. In spun yarns, twist is necessary to maintain yarn integrity and provide strength. The combination of twist level and twist direction represents a key parameter in the design of yarns or fabrics.
10. Twist Testing:
Direction Twist:
- S –Twist: When Held in vertical position, the spiral confirm in slope to the central position of the letter ‘S’
- Z –Twist: When Held in vertical position, the spiral confirm in slope to the central position of the letter ‘Z’
No of Turns (Twists) per Unit length:
- Single Twist
- Double Twist
- Twist Multiplier
Apparatus:
- Twist Tester
Methods:
- Direct Method
- Indirect Method
You may also like:
- What is Yarn | Types of Yarn
- Fancy Yarn: Types, Properties, Manufacturing Process and Application
- What is Yarn Twist | Twist Direction | Twist Level
- Yarn Count System and Determination by Different Methods