Study on Compliance Issues and Audit Requirements of Two Different Garments Factories
Authors:
Jonayed Arefine1
Raj Deep Saha
Dept. of Textile Engineering
Daffodil International University, Dhaka, Bangladesh
Email: jonayed23-4557@diu.edu.bd1
ABSTRACT
The project is basically on the rules and regulations of BSCI, ILO, BGMEA and Bond report. This report is to find out the current situations of compliance issue in different two garments industries. To observe the worker’s current situations in garments industries, take some data of BSCI, ILO, Bond and BGMEA in different garments industries. And then compared the data to each other. After that it has been shown the compression that garments A and garments B in freedom of association, child labor policy, health and safety, and other criteria. Results show that garments A is batter than garments B and garments B also batter some criteria than garments A.
INTRODUCTION
1.1 Background of the Study
Compliance is a law where they establish the worker’s rights in the factory or industries. Workers find their freedom in the factory or industry. And a compliance factory also develops its international affairs worldwide. We have interested in compliance because it is an only sector in garments industries where we should develop. Maximum companies are not maintaining the code of conduct of the compliance rules. And some companies are focused only on some rules and regulations. And some garments factories focused on all worker’s law. They maintain factory law and policy, child labor policy, freedom of associations, management practice. Nowadays buyers number one recommendation is “compliance” because they are always curious about worker’s safety. In our thesis, we focused on the main point of compliance. And how to develop compliance in every garment sector. We have an analysis of previous data of some reputed garments industries and analysis their report in our paper.
1.2 Objectives of the Study
- To compare BSCI rules between two garments in different years.
- To compare BOND license criteria between two garments in different years.
- To compare BGMEA certificates criteria between two garments in different years.
1.3 Importance of Study
From this report, a textile engineer can know about the knowledge about factory policy, child labor policy and other criteria of the BSCI, BGMEA, ILO. And how to develop compliance in the factory. A factory person gains knowledge about their rules and rights in their factory. Ordinary people gain knowledge about the rules and regulations in the garments factory. A researcher gains the knowledge about comparative audit system in compliance audit and he can focus on another issue.
1.4 Limitations of the Study
Every work sector maintains its criteria and rules; we should follow the rules and regulations. In our thesis, It has many limitations in garments industries. It is not a garment industry’s fault, they maintain their rules only. We have appreciated their rules and regulations.
We have found below limitations to complete our thesis:
- Some previous documents are missing.
- Production rate before compliance is missing (Some documents).
- Some restrictions are showing certificates.
LITERATURE REVIEW
2.1 History of Garments Industries:
For most of human history, clothing has been a handicraft. Even today, while textile production is fully computerized, garments are sewn and pieced together by human hands on sewing machines.
Before the reproduction of ready-to-wear clothing, each garment was made by oneself. Even after the Industrial Revolution, up into the early part of the 20th century a dress, for example, was made for the person who would wear it.
Though ready-to-wear apparel has been applicable for a long time, the ability to walk into a store, pluck a garment off a rack, or order it online is a relatively new idea.
In the not too far past, a garment would last for a very long time. Today, we buy an item of clothing, wear it a few times, and toss it. The creation, production, and distribution of clothing is the largest manufacturing trade in the world.
Ready to Wear in the Old Days
Antiquarian records show that merchants in Ancient Babylonia shipped and distributed some ready-to-wear garments as early as 1400 BCE (BC). In Ancient Rome, garments were composed in workshops of up to 100 workers to outfit the military.
Before 1300 CE (AD) people did not wear suited garments. Middle Eastern people wore loose, flowing robes. Medieval Europeans wore linen under-tunics and wool top tunics made of such durable fabric that a garment lasted a lifetime.[1] Women reel wool into thread and weavers, generally men, wove fabric in home workshops.
After 1350, clothing became more form suited. A small ready-to-wear industry soon began to produce shirt additions such as detachable sleeves and collars, as well as gloves, and hats. By the second half of the 16th century, gloves, stockings, collars, and hats were imported and exported in bulk volume.
Before the Industrial Revolution, most textile and garment production existed on a small scale in the home to home workshops called cottage industries. Broker dropped off raw materials to the workers’ homes where production relied on self-pacing and included low and highly skilled work.
The Industrial Revolution
In 1738 Lewis Paul and John Wyatt of England created the Roller Spinning machine which spun cotton into filament. By 1764 a multi-spool spinning wheel was able to spin filament more quickly than ever before. The Water Frame was created by Richard Arkwright in 1770 produced stronger filaments and was powered by water. It was the Water Frame that made it possible to move textile manufacture from the cottage to a factory-like setting.
The Power Loom, patented in 1784 by Edmund Cartwright wove filaments into cloth on a machine. As later improvements expended speed and efficiency, women began to replace the men who were formerly weavers. By 1880 there were 250,000 cotton automatic looms in Britain.
The first merchant ship to fly the fledgling United States flag exported ginseng and imported hats, men’s breeches, and gloves. By the late 1700s, Bristol England was home to over 200 businesses that ship hates, gloves, drawers, pants, stockings, shirts, jackets, and footwear.
Early in the 19th century, some large-scale apparel still relied on hand sewing for piece work. In 1835, a New York company promoted 800 tailors and 1200 plain sewers.
The creations of steam-powered machines for producing textiles and clothing drew the ire of frightened craftspeople. In England and France, angry tailors and weavers who saw the machinery as a threat to their livelihood stormed factories and wrecked the machinery.[2] Textile and garment work became fast-paced and dependent on the large amounts of capital that it took to purchase machinery and physical plants. Workers lost their individuality, independence, and society’s reliance on their skills. They were no longer craftspeople but employees, just cogs in the wheel.
2.2 History of Bangladesh Garments Industries:
Bangladesh earns worldwide fame especially muslin and jamdani cloth or our country was used as the deluxe garments product for the royal figures in Europe and other countries.[3] The British rulers in India didn’t develop our cloth business at all. Rather they destroyed them and carried cloths from England. Garment Industry Large-scale production of readymade garments (RMG) in organized factories is a relatively new experienced in Bangladesh. Until the early sixties, individual tailors made the product as per specifications provided by individual customers who supplied the fabrics. The domestic market for readymade garment, excepting children’s wear and men’s knit underwear (Genji), was virtually absent in Bangladesh until the sixties.
RMG industries growing in Bangladesh in 1970, then they started to export their products worldwide. The sector rapidly attained high importance in terms of job, foreign exchange earnings and its contribution to GDP.
Most importantly, the growth of the RMG sector produced a group of entrepreneurs who have created a strong private sector. Of these entrepreneurs, a sizeable number is female. A woman entrepreneur established one of the oldest export-oriented garment factories, the Baishakhi Garment in 1977. Many women hold top executive positions in the RMG industry. The hundred percent export-oriented RMG industry experienced phenomenal growth during the last 15 or so years. In 1978, there were only 9 export-oriented garment manufacturing units, which generated export earnings of hardly one million dollars. Some of these units were very small and produced garments for both domestic and export markets. Four such small and old units were Reaz Garments, Paris Garments, Jewel Garments, and Baishakhi Garments.
Reaz Garments, the pioneer, was established in 1960 as a small tailoring outfit, named Reaz Store in DHAKA. It served only domestic markets for about 15 years. In 1973 it changed its name to M/s Reaz Garments Ltd. and expanded its operations into the export market by selling 10,000 pieces of men’s shirts worth French Franc 13 million to a Paris-based firm in 1978. It was the first direct exporter of garments from Bangladesh. Desh Garments Ltd, the first non-equity joint-venture in the garment industry was established in 1979. Desh had technical and marketing collaboration with the Daewoo Corporation of South Korea. It was also the first hundred percent export-oriented company. It had about 120 operators including 3 women trained in South Korea, and with these trained workers it started its production in early 1980. Another South Korean Firm, Young one’s Corporation formed the first equity joint-venture garment factory with a Bangladeshi firm, Trexim Ltd. in 1980. Bangladeshi partners contributed 51% of the equity of the new firm, named Young ones Bangladesh. It exported its first consignment of padded and non-padded jackets to Sweden in December 1980.
Till the end of 1982, there were only 47 garment manufacturing units. The breakthrough occurred in 1984-85 when the number of garment factories increased to 587. The number of RMG factories shot up to around 2,900 in 1999. Bangladesh is now one of the 12 largest apparel exporters of the world, the sixth-largest supplier in the US market and the fifth- largest supplier of T-shirts in the EU market. The industry has grown during the 1990s roughly at the rate of 22%.
2.3 Problems of Garments Industry
2.3.1 Raw materials:
Bangladesh imports raw materials for garments like cotton, thread color, etc. This dependence on raw materials hampers the development of the garments industry. Moreover, foreign suppliers often supply low-quality materials, which result in low-quality products.
2.3.2 Unskilled workers:
Most of the illiterate women workers employed in garments are unskilled and so their products often become lower in quality.
2.3.3 Improper working environment:
- Taking the advantages of workers’ poverty and ignorance the owners forced them to work in unsafe and unhealthy workplaces overcrowded with workers beyond the capacity of the factory floor and improper ventilation.
- Most of the garment factories in our country lack the basic amenities where our garment workers sweat their brows from morning to evening to earn our countries the major portion of our foreign exchange. Anybody visiting the factory the first impression he or she will have that these workers are in a roost.
- Improper ventilation, stuffy situation, filthy rooms are the characteristics of the majority of our factories. The owners’ profit is the priority and this attitude has gone to such an extent that they do not care about their lives.
2.3.4 Lack of managerial knowledge:
There are some other problems which are associated with this sector. Those are- lack of marketing tactics, absence of easily on-hand middle management, a small number of manufacturing methods, lack of training organizations for industrial workers, supervisors and managers, autocratic approach of nearly all the investors, fewer process units for textiles and garments, sluggish backward or forward blending procedure, incompetent ports, entry/exit complicated and loading/unloading takes much time, time-consuming custom clearance etc.
2.3.5 The gendered division of labor:
In the garment industry in Bangladesh, tasks are allocated largely based on gender. This determines many of the working conditions of women workers. All the workers in the sewing section are women, while almost all those in the cutting, ironing and finishing sections are men. Women workers are absorbed in a variety of occupations from cutting, sewing, inserting buttons, making buttonholes, checking, cleaning the threads, ironing, folding, packing and training to supervising.
Women work mainly as helpers, machinists and less frequently, as line supervisors and quality controllers. There are no female cutting masters. Men dominate administrative and management-level jobs. Women are discriminated against in terms of access to higher-paid white collar and management positions.
When asked why they prefer to amply women for sewing, the owner and managers gave several reasons. Most felt that sewing is traditionally done by women and that women are more patient and more controllable than men.
2.3.6 Wages:
The government of Bangladesh sets minimum wages for various categories of workers. According to Minimum Wage Ordinance 1994, apprentices’ helpers are to receive Tk500 and Tk930 per month respectively. Apprentices are helpers who have been working in the garment industry for less than three months. After three months, Apprentices are appointed as helpers. Often female helpers are discriminated against in terms of wages levels, and these wages are also often fixed far below the minimum wage rate. A survey conducted in 1998 showed that 73% of female helpers, as opposed to 15% of their male counterparts, did not receive even the minimum wage.
2.3.7 Insufficient for loan:
Insufficiency of the loan in time, the uncertainty of electricity, delay in getting materials, lack of communication, the problem in taxes, etc. Often obstruct the industry. In the world market, 115 to 120 items of dress are in demand whereas Bangladesh supplies only ten to twelve items of garments. India, South Korea, Hong Kong, Singapore, Thailand, Taiwan, etc, have made remarkable progress in garments industries. Bangladesh is going to challenge the garments of those countries in the world market.
2.3.8 Unit labor cost:
Bangladesh has the cheapest unit labor cost in South Asia. It costs only 11 cents to produce a shirt in Bangladesh, whereas it costs 79 cents in Sri Lanka and 26 cents in India. Bangladesh’s comparative advantage lies in having the cheapest unit labor cost.
2.3.9 Working hours:
Though the wages are low, the working hours are very long. The RMG factories claim to operate one eight-hour shift six days a week. The 1965 factory Act allows women to work delivery deadlines; however, women are virtually compelled to work after 8 o’clock. Sometimes they work until 3 a.m. and report back to start work again five hours later ar at 8 o’clock. They are asked to work whole months at a time the Factory Act, which stipulates that no employee should work more than ten days consecutively without a break.
2.3.10 Safety Problems:
Because of the carelessness of the factory management and for their arrogance factory doors used to be kept locked for security reason-defying act.
Safety need for the worker is mandatory to maintain in all the organization. But without the facility of this necessary product, a lot of accidents is occur incurred every year in most of the company.
Some important cause of the accident is given below-
- Routes are blocked by storage materials.
- The machine layout is often staggered.
- Lack of signage for an escape route.
- No provision for emergency lighting.
- Doors, opening along escape routes, are not fire-resistant.
- Doors are not self-closing and often do not open along the direction of escape.
- Adequate doors, as well as adequate staircases, are not provided to aid quick exit.
- Fire exit or emergency staircase lacks proper maintenance.
- Lack of proper exit route to reach the place of safety.
- Parked vehicles, goods and rubbish on the outside of the building obstruct exits to the open air.
- Fire in a Bangladesh factory is likely to spread quickly because the principle of compartmentalization is practiced.
2.4 Compliance Audit
A compliance audit is an independent evaluation to ensure that an organization is following external laws, rules, and regulations or internal guidelines, such as corporate bylaws, controls, and policies and procedures. Compliance audits may also determine if an organization is conforming to an agreement, such as when an entity accepts government or other funding. Although most people are familiar with financial audits, such as those for public companies through the Sarbanes-Oxley Act (SOX) or individual or corporate tax audits through the Internal Revenue Service (IRS), compliance audits are not merely financial. Audits may also review IT and other security issues, compliance with HR laws, quality management systems, and other areas. Compliance is one leg in the tripod of GRC, which stands for governance, risk, and compliance.
Compliance is important for many reasons. Aside from signifying levels of professional standards, like the ISO 9000, ISO 14000, and other guidelines, noncompliance with regulatory guidelines may bring sanctions and penalties. Penalties for noncompliance with federal regulations, such as Sarbanes-Oxley, are specified through the Federal Sentencing Guidelines Act and apply fines based on a formula that calculates the most recent offenses and determines whether the organization employs a compliance officer who communicates regulatory needs to the organization.[5]
Boards of directors are also often accountable for operations and need to see audit reports. If a regulatory agency does investigate, proof of a compliance program is important to show that the organization has controls and other mechanisms that can detect deficiencies and even illegal activity.
Depending on the circumstances, the audit may be conducted by an employee, such as an internal auditor, a certified public accountant, a third-party auditor, or a government auditor. In many circumstances, auditors may seek expert advice from outside specialists, such as lawyers.
Audits provide recommendations on ways to make improvements or corrective actions and to prevent future deficiencies or nonconformities. Audits review for effectiveness to determine the number of compliant versus non-compliant processes. Audits also help organizations to stay in compliance with frequently changing federal regulations. Also, audits identify areas of risk for noncompliance within the organization and report these appraisals to management and the appropriate regulatory entity as applicable.
2.4.1 BSCI
The BSCI is the European social monitoring system for ethical sourcing initiated by the Brussels-based Foreign Trade Association (FTA). BSCI is a business-driven initiative for companies committed to improving working conditions in the global supply chain. BSCI unites hundreds of companies around one common Code of Conduct and supports them in their efforts to build an ethical supply chain by providing them with a step-by-step development-oriented system, applicable to all sectors and all sourcing countries.
BSCI Code of Conduct is built on the most important International Conventions protecting workers’ rights, notably the ILO Conventions and recommendations. All BSCI participants commit to implement the Code in their supply chains. BSCI supports companies by providing them with a range of interlinked activities and tools to achieve a socially compliant supply chain.[6]
The 11 Principles of the Code of Conduct that BSCI participants commit to implement in their supply chains are:
- The rights to Freedom of Association and Collective Bargaining
- No Discrimination
- Fair Remuneration
- Decent Working Hours
- Occupational Health and Safety
- No Child Labor
- Protection of Young Workers
- No Precarious Employment
- No Bonded Labour
- Protection of the Environment
- Ethical Business Behavior
2.4.2 ILO
The International Labour Organization (ILO) is a United Nations agency whose mandate is to advance social justice and promote decent work by setting international labor standards. It was the first specialized agency of the UN. The ILO has 187 member states: 186 of the 193 UN member states plus the Cook Islands are members of the ILO. The tripartite structure is unique to the ILO where representatives from the government, employers, and employees openly debate and create labor standards. [7]
The International Labour Office is the permanent secretariat of the International Labour Organization. It is the focal point for the International Labour Organization’s overall activities, which it prepares under the scrutiny of the Governing Body and the leadership of the Director-General.
The ILO employs some 2,700 officials from over 150 nations at its headquarters in Geneva, and in around 40 field offices around the world. Among these officials, 900 work in technical cooperation programmers and projects.
In 1969, the ILO received the Nobel Peace Prize for improving fraternity and peace among nations, pursuing decent work and justice for workers, and providing technical assistance to other developing nations. Fifty years later to mark the organization’s centenary, it convened a Global Commission on the Future of Work, whose report, published in January 2019, made ten recommendations for governments to meet the unprecedented challenges of a changing world of work. Those included a universal labor guarantee, social protection from birth to old age and entitlement to lifelong learning.
The International Labour Organization has developed a system of international labor standards aimed at promoting opportunities for women and men to obtain decent and productive work, in conditions of freedom, equity, security, and dignity.
2.4.3 BGMEA
The Bangladesh Garment Manufacturers and Exporters Association (BGMEA) is one of the largest trade associations in the country representing the readymade garment industry, particularly the woven garments, knitwear and sweater sub-sectors with equal importance. Starting its journey in 1983 today BGMEA takes care of an industry that is at the backbone of Bangladesh’s economy. Since its inception, BGMEA is dedicated to promote and facilitate the apparel industry through policy advocacy to the government, services to members, ensuring workers’ rights and social compliance at factories.[8]
2.4.3.1 Mission and Vision
BGMEA works with the vision to develop the RMG industry of Bangladesh and the economy of the country. Having such vision BGMEA chalked out the following missions and its strategic direction is paved accordingly –
Firstly, to protect and promote the interests of the industry; thus ensuring sustained growth in the foreign exchange earnings of the country.
Secondly, BGMEA is committed to ensuring all legitimate rights and privileges of the garment workers. The association also strives toward the betterment of society and the environment.[9]
2.4.3.2 Members
BGMEA started with only 12 members in the early 1980’s and presently has around 4500 member factories. Around 40% of BGMEA member factories are knitwear and sweater manufacture, and the rest 60% are woven garment manufactures. BGMEA member factories account for 100% woven garment exports of the country and more than 95% of sweater exports, while around half of the light knitwear exports are made by them.
2.4.3.3 How BGMEA Runs
BGMEA is being run by a 35-member elected Board of Directors. The Board of Directors is elected for a two-year term. Seven Vice Presidents having important portfolios, along with a secretariat of experienced officials, assists the President in formulating and executing vital policies and programs of the organization. The President is the highest executive authority of the association. The Board of Directors takes assistance from different Standing Committees headed by a Chairman and composed of members having vast experience in the related fields. Strict adherence to democratic norms and code of conduct are being maintained in the BGMEA elections, which has been regarded as a trendsetter in trade body elections of Bangladesh for its pre-election projection caucus and election-day discipline.
2.4.4 BOND
As per Customs Act, 1969, 100% export-oriented businesses are eligible to get bond facilities. Bond facilities were present from the early year of Customs act enactment. Initially, Bond benefits were monitored by the concern Custom Houses. Then one company has to go all Custom Houses through which he import or export. It was a very complex work for the reconciliation of import and export quantities. To avoid such a situation and encouraging export businesses, in November 2000, the Customs Bond Commissionerate started is a journey. There are different types of Bond Licenses issued by this office for facilitating exporters. Now, most of the 100% export industries are running under the direct supervision of Bond Commissionerate.
2.4.5 CSR
Corporate social responsibility (CSR) is a self-regulating business model that helps a company be socially accountable—to itself, its stakeholders, and the public. By practicing corporate social responsibility, also called corporate citizenship companies can be conscious of the kind of impact they are having on all aspects of society, including economic, social, and environmental.
To engage in CSR means that, in the ordinary course of business, a company is operating in ways that enhance society and the environment, instead of contributing negatively to them.
2.4.5.1 Key Takeaway
Corporate social responsibility is important to both consumers and companies.
Starbucks is a leader in creating corporate social responsibility programs in many aspects of its business.
Corporate responsibility programs are a great way to raise morale in the workplace.
2.4.5.2 Understanding Corporate Social Responsibility (CSR)
Corporate social responsibility is a broad concept that can take many forms depending on the company and industry. Through CSR programs, philanthropy, and volunteer efforts, businesses can benefit society while boosting their brands.
As important as CSR is for the community, it is equally valuable for a company. CSR activities can help forge a stronger bond between employees and corporations; boost morale, and help both employees and employers feel more connected with the world around them.
2.4.5.3 Example of Corporate Social Responsibility
Long before its initial public offering (IPO) in 1992, Starbucks was known for its keen sense of corporate social responsibility, and commitment to sustainability and community welfare.
According to the company, Starbucks has achieved many of its CSR milestones since it opened its doors. As per its 2018 “Global Social Impact Report,” these milestones include “reaching 99% of ethically sourced coffee, creating a global network of farmers, pioneering green building throughout its stores, contributing millions of hours of community service, and creating a groundbreaking college program for its partner/employees.”
Starbucks’ goals for 2020 and beyond include hiring 10,000 refugees across 75 countries, reducing the environmental impact of its cups, and engaging its employees in environmental leadership. Today there are many socially responsible companies whose brands are known for their CSR programs, such as Ben & Jerry’s ice cream and Everlane, a clothing retailer.
2.4.5.4 Special Considerations
In 2010, the International Organization for Standardization (ISO) released a set of voluntary standards meant to help companies implement corporate social responsibility. Unlike other ISO standards, ISO 26000 provides guidance rather than requirements because the nature of CSR is more qualitative than quantitative, and its standards cannot be certified.
Instead, ISO 26000 clarifies what social responsibility is and helps organizations translate CSR principles into practical actions. The standard is aimed at all types of organizations, regardless of their activity, size, or location. And, because many key stakeholders from around the world contributed to developing ISO 26000, this standard represents an international consensus.
2.4.6 BSCI
The Business Social Compliance Initiative (BSCI) is a business-driven initiative for companies committed to improving working conditions in their international supply chains. BSCI unites hundreds of companies around one common Code of Conduct and supports them in their efforts towards building an ethical supply chain by providing them with a development-oriented system, applicable to all sectors and all sourcing countries.
2.4.6.1 The BSCI code of conduct is based on:
ILO core labor standards of the International LabourOrganisation. United Nations Conventions on children’s rights. United National Conventions to eliminate all forms of discrimination. The United Nations Universal Declaration of Human Rights. The code does explicitly name these conventions.
The living wage is partly covered in the phrase: ‘In situations in which the legal minimum wage does not cover living wage expenses and provide some additional 7 disposable income, companies shall strive to provide employees with adequate compensation to meet these needs’ (emphasis added).
BSCI member-supplier contracts: Recognition and application of the BSCI code is part of BSCI members-suppliers contracts. Suppliers and their subcontractors must accept and implement these standards as a condition of these contracts.
Request for an audit: Request for an audit is made by a BSCI Member Company or by the supplier. This audit is based on the BSCI Audit Questionnaire, the BSCI Audit Report and the BSCI Audit Guidelines.
The audit is comprised of three parts:
- Master data
- BSCI Social Requirements. Best Practice for Industry such as SA8000 or equivalent certification
Deficiencies: If deficiencies are found during an audit, corrective actions must be agreed upon. Corrective actions arising from non-compliance with issues in part B of the Audit questionnaire are compulsory; implementation of corrective actions arising from issues in part C is voluntary. Corrections and improvements: Corrections and improvements to supplier situations will be carried out by the BSCI members, their representatives, and/or the suppliers themselves. The time frame and intensity of corrective action lie within the BSCI member’s discretion and depends in part on the specific nature of the actions required. Termination of a contract is considered a last resort. The audit procedure is repeated every three years, beginning with the start of the initial audit. Suppliers that are certified according to SA8000 are exempted from the BSCI auditing process.
Costs: Costs related to audits, improvement actions, and implementation control of necessary corrective action is negotiated between BSCI members and their suppliers.
Complaints mechanism: The BSCI will set up a complaints mechanism and local round table discussions for interested parties will also be established. These will serve as forums for discussion and the airing of any complaints from BSCI monitoring system activities.
Assessment of the Social audit: Reports The auditor prepares a Social Audit Report, which assesses the social audit and indicates the corrective action that one is required to implement (Part B of the questionnaire ‘Minimum Social Requirements’) or that one chooses to implement (part C of the questionnaire ‘Best practice for Industry
EXPERIMENTAL DETAILS
For Garments A:
3.1 BSCI Audit Report:
Table 3.1 – BSCI Report of 2009
Name of the Law | Correct | Not Correct | Improvement | Marks |
Management Practice | Y | 1 | ||
Documentation | Y | 1 | ||
Working Time | Y | 2 | ||
Compensation | Y | 1 | ||
Child Labour | N/R | 1 | ||
Forced Labour | Y | 2 | ||
Freedom of Association | N/R | 1 | ||
Discrimination | Y | 2 | ||
Working Condition | N/R | 1 | ||
Health Facilities | Y | 1 | ||
Occupational Health and Safety | Y | 1 | ||
Dormitories | N/R | 1 | ||
Environment | N/R | 1 |
Table 3.1 shows that the BSCI audit report of 2009 of Sicily garments, where it was shown that, their management practice is correct but some obligations are found and they can easily solve this problem. Documentations are quite good in this industry. Working time is perfect and BSCI is pleased with their working time. Compensation is quite good. Child labor is funded in that period and they give a short notice latter to the company. No forced labor was founded in the garments. There are some obligations are found in the freedom of the association, and they improve the objective. Discriminations are not founded in the company. The working condition is not good enough. They need to improve their working conditions. Health and facilities are quite good. The environment is related to working conditions.
3.1.1 Report of 2013 on Morshed Limited:
1. Law and Factory Policy
Table 3.2- Law and factory policy 2013
Name of the law | Correct | Not Correct | Improve Needed | Grading Mark |
Posted current rules and regulations | Yes | 2 | ||
Employee handbook | Needed | 1 | ||
Employee Personal files | Yes | 1 | ||
Appointment letter and ID card | Needed (ID card not found) | 1 |
Table 3.2 shows the BSCI audit report of Morshed Limited. Where it was shown that they have posted their rules and regulations in the garments factory and they posted the same things on every floor. Employee handbook was missing and some are incomplete. Employee personal files are also missing and some corrections needed. An appointment letter is found but the ID card is missing.
2. Child Labour Policy:
Table 3.3- Child Labour Policy 2013
Name of the law | Correct | Not Correct | Improve Needed | Grading Mark |
Legal minimum working age in this country (18 years old) | Needed | 1 | ||
Verify the age of job applicants | Yes | 2 | ||
Maintain an age record for all employee | Needed | 1 | ||
Protect from the child labour | Needed | 1 |
Table 3.3 shows the BSCI audit report of Morshed Limited. Where it was shown that they have to work with their minimum working age, the report shows that they did not maintain the minimum age of the workers and BSCI give improvement needed. Morshed limited verify their worker job application very hard, they send their team to workers area to collect the worker’s local profile. Age record was not perfectly done at that time, so they need to improve. They have some child labor. So BSCI code of conduct says that “no child labor in garments”
3. Health and Safety:
Table 3.4- Health and Safety 2013
Name of the law | Correct | Not Correct | Improve Needed | Grade |
Exit doors should open | Yes | 2 | ||
Exit signs | Yes | 2 | ||
Exit marks | Improve | 1 | ||
Emergency light should be battery backup | Improve | 1 |
Emergency Diagram | Yes | 1 | ||
Fire extinguishers should sufficient and appropriate | Improve | 1 | ||
Fire Fighting training | Yes | 2 | ||
Fire extinguishers should clearly mark and visible | Improve | 1 | ||
Fire drills should be conducted at least twice a year with records and photos | Improve | 1 | ||
Fire alarm system | Yes | 2 | ||
Electrical Channel are covered | Improve | 1 | ||
Machine maintains | Yes | 2 | ||
Machine and high temperature machines kept distance from work station | Yes | 2 | ||
Employee should wear appropriate personal protective equipment | Improve | 1 | ||
Doctor and Nurse | Improve | 1 | ||
Accident Record | Yes | 2 |
Table 3.4 shows the BSCI audit report of Morshed Limited. Where it was shown that Garments exit doors always open for everyone. When an emergency, workers go outside easily. Morshed Limited arrange their factory as a compliance factory. They sign exit point to everywhere. And they need to improve to exit marks in the industry. They need a battery backup to emergency light. They have an emergency diagram but they need to improve this because the paper is getting old. Fire extinguishers need to a place. They have completed 2 times of year Fire Fighting training in the factory. They take fire drills to workers, but they have no photos. The factory has a 100 percent fire alarm and all are active. The electrical channel is not covered, so any kind of accident can happen. The machine maintains and high-temperature machines are kept away from the worker’s zone. They need a good doctor for workers. They have collected all records of the accident.
4. Freedom of Association:
Table 3.5- Freedom of Association in 2013
Name of the law | Correct | Not Correct | Improve Needed | Grade |
Worker elected committee | Improve | 1 | ||
Safety committee | Improve | 1 | ||
Worker welfare committee | Yes | 2 |
Table 3.5 shows the BSCI audit report of Morshed Limited. Where it was shown that they have no correct elected committee in the factory but they have a committee that is selected by a compliance audit, who is best for the workers. They have a safety committee but the committee needs some improvements, like a fire drill, etc. they have a strong welfare committee to share their needs and wants to
5. Others:
Table 3.6- others rules 2013
Name of the law | Correct | Not Correct | Improve Needed | Grade |
Factory License | Yes | 2 | ||
EPB | Yes | 2 |
Trade license | Yes | 2 | ||
ERC | Yes | 2 | ||
IRC | Yes | 2 | ||
Compressor Machine | Yes | 2 | ||
No Discrimination | Yes | 2 | ||
Working Hours maintain | Yes | 2 |
Table 3.6 shows the BSCI audit report of Morshed Limited. Where it was shown that Morshed limited has all important certificates and many important papers. And all papers are up to date.
3.1.2 Report of 2018 on Morshed Limited:
A. Law and Factory Policy
Table 3.7- Law and Factory Policy 2018
Name of the law | Correct | Not Correct | Improve Needed | Grading Mark |
1. Posted current rules and regulations | Yes | 2 | ||
2. Employee handbook | Yes | 2 | ||
3. Employee Personal files | Yes | 2 |
4. Appointment letter and ID card | Yes | 1 |
Table 3.7 shows the BSCI audit report of Morshed Limited. Where it was shown that They posted current rules and regulations in the factory notice board and give the subreport to the full factory. They give employee handbook to every worker, where they note the worker’s salary and their personal data. Personal files are up to date for every worker. In the files, they keep some records. Like- personal information, medical data, joining date, etc. Appointment letters and ID cards are handed over to every worker. But some left their job so they do not return their ID cards.
B. Child Labor Policy:
Table 3.8- Child Labour Policy 2018
Name of the law | Correct | Not Correct | Improve Needed | Grading Mark |
Legal minimum working age in this country (18 years old) | Yes | 2 | ||
Verify the age of job applicants | Yes | 2 | ||
Maintain an age record for all employee | Yes | 1 | ||
Protect from the child labor | Yes | 1 |
Table 3.8 shows the BSCI audit report of Morshed Limited. Where it was shown that Morshed Limited check National Identity Card in every worker. So the law of Bangladesh government, every citizen can found his/her NID card when his/her age is 18. So Morshed Limited ensures the legal age of the works. Morshed limited has a verification committee to verify workers. So they can verify the worker’s age by NID card and birth certificate. Morshed limited has workers file to collect all the records of workers. And the ensure the “No child labor in garment
C. Health and Safety:
Table 3.9- Health and Safety 2018
Name of the law | Correct | Not Correct | Improve Needed | Grade |
1. Exit doors should open | Yes | 2 | ||
2. Exit signs | Yes | 2 | ||
3. Exit marks | Yes | 2 | ||
4. Emergency light should be battery backup | Yes | 2 | ||
5. Emergency Diagram | Yes | 2 | ||
6. Fire extinguishers should sufficient and appropriate | Yes | 1 | ||
7. Fire Fighting training | Yes | 1 | ||
8. Fire extinguishers should clearly mark and visible | Yes | 1 | ||
9. Fire drills should be conducted at least twice a year with records and photos | Yes | 1 | ||
10. Fire alarm system | Yes | 2 | ||
11. Electrical Channel are covered | Yes | 2 | ||
12. Machine maintains | Yes | 2 | ||
13. Machine and high temperature machines kept distance from work station | Yes | 1 | ||
14. Employee should wear appropriate personal protective equipment | Improve | 1 | ||
15. Doctor and Nurse | Yes | 1 |
16. Accident Record | Yes | 1 |
Table 3.9 shows the BSCI audit report of Morshed Limited. Where it was shown that every rule is perfectly arranged. But they need to improve personal protective equipment, like apron, gloves, hood cap, and finger guard. And every section is done perfectly.
D. Freedom of Association:
Table 3.10- Freedom of Association 2018
Name of the law | Correct | Not Correct | Improve Needed | Grade |
Worker elected committee | Yes | 2 | ||
Safety committee | Yes | 2 | ||
Worker welfare committee | Yes | 2 |
Table 3.10 shows the BSCI audit report of Morshed Limited. Where it was shown that Morshed limited has worker elected committee, safety committee and worker welfare committee in a good position.
E. Others:
Table 3.11- Others Certification in 2018
Name of the law | Correct | Not Correct | Improve Needed | Grade |
Factory License | Yes | 2 | ||
EPB | Yes | 2 | ||
Trade license | Yes | 2 | ||
ERC | Yes | 2 | ||
IRC | Yes | 2 | ||
Compressor Machine | Yes | 2 |
No Discrimination | Yes | 2 | ||
Working Hours maintain | Yes | 2 |
Table 3.11 shows that BSCI audit report of Morshed Limited. Where it was shown that Morshed limited keep update their all certificate.
3.2 ILO (International Labour Organization) Audit Report:
A. Worker Safety Report (A)
Table 3.12- Worker safety report 2013 (A)
Name of the law | Yes | No | Improvement | Note |
Working Hours | √ | Good 8 hours | ||
Conditions of employment | √ | Need some instruments | ||
Accommodation | √ | Some rest rooms needed | ||
Recreation Facilities | √ | Good. Arrange festival program | ||
Food and Catering | √ | Good | ||
Accident Prevention | √ | Enough medical kit |
Heath Protection | √ | Need some elements for workers | ||
Medical Care | √ | Need Doctor in the factory | ||
Security | √ | Good |
Table 3.12 shows the ILO audit report of Morshed Limited. Where it was shown that They have fulfilled maximum criteria but they need to develop some sector. Conditions of employment are one of the major points. They need to improve the conditions of employment. They also develop health protection and medical care. They need some extra first aid box and regular doctor.
B. Worker Safety report (B)
Table 3.13- Worker Safety report 2013 (B)
Name of the law | Yes | No | Improvement | Note |
Minimum Age | √ | Need to update | ||
Medical Certification | √ | Need Update | ||
Qualifications of workers | √ | Good | ||
Employee Agreements | √ | Good | ||
Hours of working rest | √ | 1 hour |
Worker certificate (NID or Local Certificate) | √ | Good | ||
Document of safety | √ | Need update | ||
Accommodation | √ | Need update | ||
Recreational Facilities | √ | Good | ||
Food | √ | Good | ||
Safety | √ | Good | ||
Medi Care | √ | Improvement Needed | ||
Compliant Procedure | √ | Improvement Needed | ||
Payment | √ | Good |
Table 3.13 shows the ILO audit report of Morshed Limited. Where it was shown that they need to improve – Minimum Age, Medical Certification, Document of safety, Accommodation, MediCare, Complaint Procedure. In 2013, they look at this topic and they try to change the result.
Table 3.14- Worker Safety report 2018
Name of the law | Yes | No | Improvement | Note |
Working Hours | √ | Good 8 hours | ||
Conditions of employment | √ | Good | ||
Accommodation | √ | Good | ||
Recreation Facilities | √ | Good. Arrange festival program | ||
Food and Catering | √ | Good | ||
Accident Prevention | √ | Enough medical kit | ||
Heath Protection | √ | Good | ||
Medical Care | √ | Good | ||
Security | √ | Good |
Table 3.14 shows the ILO audit report of Morshed Limited. Where it was shown that Morshed limited fulfill all code of conduct of the ILO. And ILO recommended keeping non- changeable their activities.
Table 3.15- Worker safety report 2018
Name of the law | Yes | No | Improvement | Note |
Minimum Age | √ | Good | ||
Medical Certification | √ | Good | ||
Qualifications of workers | √ | Good | ||
Employee Agreements | √ | Good | ||
Hours of working rest | √ | 1 hour | ||
Worker certificate (NID or Local Certificate) | √ | Good | ||
Document of safety | √ | Good | ||
Accommodation | √ | Good | ||
Recreational Facilities | √ | Good | ||
Food | √ | Good | ||
Safety | √ | Good |
Medi Care | √ | Good | ||
Compliant Procedure | √ | Good | ||
Payment | √ | Good |
Table 3.15 shows the ILO audit report of Morshed Limited. Where it was shown that Morshed limited fulfill all code of conduct of the ILO. And ILO recommended keeping non-changeable their activities.
3.3 BOND Certificate
Table 3.16- Bond Certificate 2013
Name of documents | YES | NO |
Article of memorandum | Y | |
TIN certificate | Y | |
Owner TIN Certificate | Y | |
Trade License | Y | |
Vat Registration certificate | Y | |
Money Exchange Certificate | Y | |
IRC | Y | |
ERC | Y | |
BGMEA certificate | Y | |
EPD certificate | Y | |
Building Plan | Y | |
Fire License | Y | |
Fire Insurance | Y | |
Boiler License | Y | |
List of machines | Y |
Back to back L/C | Y | |
Bank Solvency Certificate | Y | |
Machine Certificate | Y | |
Factory Profile | Y | |
Risk Bond | Y | |
Lean Bank Report | Y | |
Owner TIN Copy | Y |
Table 3.17- Bond certificate 2018
Name of documents | YES | NO |
Article of memorandum | Y | |
TIN certificate | Y | |
Owner TIN Certificate | Y | |
Trade License | Y | |
Vat Registration certificate | Y | |
Money Exchange Certificate | Y | |
IRC | Y | |
ERC | Y | |
BGMEA certificate | Y | |
EPD certificate | Y | |
Building Plan | Y | |
Fire License | Y | |
Fire Insurance | Y | |
Boiler License | Y | |
List of machines | Y | |
Back to back L/C | Y |
Bank Solvency Certificate | Y | |
Machine Certificate | Y | |
Factory Profile | Y | |
Risk Bond | Y | |
Lean Bank Report | Y | |
Owner TIN Copy | Y |
Table 3.16 and 3.17 shows that ILO audit report of Morshed Limited. Where it was shown that for bond certifications Morshed Limited full fill all criteria of the BOND certificate. And they keep their paper up to date.
3.4 BGMEA Certificate
A. BGMEA Certificate in 2013
Table 3.18- BGMEA Certificate in 2013
Requirements | Yes | No |
Application on company letter head pad to Secretary General, BGMEA for Provisional Membership | Yes | |
Duly filled up Prescribed Application for Membership Form of BGMEA. | Yes | |
Registration of DOT (Department of Textile) / BOI (Board of Investment) | Yes | |
Specimen Signature of Board of Directors /Managing Partners/ Proprietor with 2 Copy passport size Photographs of each attested by Lien Bank. | Yes | |
Copy of Memorandum & Articles of Association & Incorporation Certificate for Pvt. Limited Company. | Yes | |
Copy of National ID / Passport (Board of Directors /Managing Partners/Proprietor). | Yes | |
Copy of up to date Trade License. | Yes | |
Copy of Fire License. | Yes | |
Copy of TIN Certificate. | Yes | |
List of Machineries (On Company letter head pad). | Yes | |
Copy of L/C of Machinery, Commercial Invoice, Bill of Lading & Bill of Entry | Yes |
( if available). | ||
Copy of Deed Agreement with Land Owner/ Land ownership documents | Yes | |
Copy of Soil Test Report & details of issuing company | Yes | |
Copy of Approved Building Plan.( Architectural Design) | Yes | |
Copy of Structural Design signed by IEB registered Engineer | Yes | |
Completion Certificate provided by IEB registered Engineer (May be partial/Full) | Yes | |
Factory Lay-Out Plan | Yes |
Table 3.18 shows the ILO audit report of Morshed Limited. Where it was shown that Morshed limited completed their all criteria to achieve BGMEA certifications in provisional steps. They have legal documents to show BGMEA.
B. BGMEA Permanent Certificate in 2013
Table 3.19- Permanent membership of BGMEA
Requirements | Yes | No |
Application on company letter head pad to Secretary General, BGMEA for Permanent Membership | Yes | |
Copy of VAT registration Certificate. | Yes | |
Copy of ERC Certificate. | Yes | |
Copy of IRC Certificate. | Yes | |
Workers BIO Metric database certificate (provided by BGMEA). | Yes | |
Worker Group Insurance Certificate (provided by BGMEA), {If required} | Yes |
Bond License | Yes |
Table 3.19 shows the ILO audit report of Morshed Limited. Where it was shown that when they pass all the criteria of the provisional stage then BGMEA promotes to permanent membership.
A. BGMEA certificate in 2018
Table: 3.20- BGMEA membership 2018
Requirements | Yes | No |
Application on company letter head pad to Secretary General, BGMEA for Provisional Membership | Yes | |
Duly filled up Prescribed Application for Membership Form of BGMEA. | Yes | |
Registration of DOT (Department of Textile) / BOI (Board of Investment) | Yes | |
Specimen Signature of Board of Directors /Managing Partners/ Proprietor with 2 Copy passport size Photographs of each attested by Lien Bank. | Yes | |
Copy of Memorandum & Articles of Association & Incorporation Certificate for Pvt. Limited Company. | Yes | |
Copy of National ID / Passport (Board of Directors /Managing Partners/Proprietor). | Yes | |
Copy of up to date Trade License. | Yes | |
Copy of Fire License. | Yes | |
Copy of TIN Certificate. | Yes | |
List of Machineries (On Company letter head pad). | Yes | |
Copy of L/C of Machinery, Commercial Invoice, Bill of Lading & Bill of Entry (if available). | Yes | |
Copy of Deed Agreement with Land Owner/ Land ownership documents | Yes | |
Copy of Soil Test Report & details of issuing company | Yes | |
Copy of Approved Building Plan.( Architectural Design) | Yes | |
Copy of Structural Design signed by IEB registered Engineer | Yes | |
Completion Certificate provided by IEB registered Engineer (May be | Yes |
partial/Full) | ||
Factory Lay-Out Plan | Yes |
Table 3.20 shows the ILO audit report of Morshed Limited. Where it was shown that they stable their position and every year BGMEA sends a representative to a garments to check it. All files up to date or not.
B. BGMEA Permanent Certificate in 2018
Table 3.21- BGMEA permanent report 2018
Requirements | Yes | No |
Application on company letter head pad to Secretary General, BGMEA for Permanent Membership | Yes | |
Copy of ERC Certificate. | Yes | |
Copy of IRC Certificate. | Yes | |
Workers BIO Metric database certificate (provided by BGMEA). | Yes | |
Worker Group Insurance Certificate (provided by BGMEA), {If required} | Yes | |
Bond License | Yes |
Table 3.21 shows the ILO audit report of Morshed Limited. Where it was shown that BGMEA has done the provisional audit and they stay their certificate to Morshed Limited.
For Garments B:
3.5 BSCI audit report:
Table 3.22 BSCI audit report 2018
Name of laws | Correct | Not- correct | Improvement | Remarks |
Social management system and cascade effect | Y | N/R | 3(C) | |
Workers involvement and protection | Y | N/R | 3 (C) | |
Te rights of freedom of association | Y | 5(A) | ||
No discrimination | Y | 5(A) | ||
Fair Remuneration | Y | 5(A) | ||
Decent working hours | Y | 5(A) | ||
Occupational Health and safety | Y | N/R | 2(D) | |
No child labour | Y | 5(A) | ||
Special protection for young workers | Y | 5(A) | ||
No precarious employment | Y | 5(A) | ||
No bonded labour | Y | 5(A) | ||
Protection of the environment | Y | 5(A) | ||
Ethical business behavior | Y | 5(A) |
Table 3.22 shows that the BSCI audit report of 2018 of Clamoon Garments, where it was shown that, their management practice is needed to improve Documentations are quite good in this industry. Working time is perfect. Compensation is quite good. Child labor isn’t funded. No forced labor was founded in the garments. Discriminations are not founded in the company. The working condition is good enough. Health and facilities are quite good. The environment is related to working conditions.
3.6 BSCI Report of 2019
1. Law and Factory Policy
Table 3.23- Law and factory policy 2019
Name of the law | Correct | Not Correct | Improve Needed | Grading Mark |
Posted current rules and regulations | Yes | 5 | ||
Employee handbook | Yes | 5 | ||
Employee Personal files | Yes | 5 | ||
Appointment letter and ID card | Yes | 5 |
Table 3.23 Overall observation shows that the facility partially complies with the requirements of this performance area. Facility provides contract letter to all employees upon employment no false apprenticeship contract used by the facility etc. However few gaps have been identified during implementation of this performance area.
2. Child Labour Policy:
Table 3.24 – Child Labour Policy 2019
Name of the law | Correct | Not Correct | Improve Needed | Grading Mark |
Legal minimum working age in this country (18 years old) | Yes | 5 |
Verify the age of job applicants | Yes | 5 | ||
Maintain an age record for all employee | Yes | 5 |
Table 3.24 Observation shows that they have to work with their minimum working age, the report shows that they maintain the minimum age of the workers and BSCI give excellent ratting.
3. Health and Safety:
Table 3.25- Health and Safety 2019
Name of the law | Correct | Not Correct | Improve Needed | Grade |
Exit doors should open | Yes | 5 | ||
Exit signs | Yes | 5 | ||
Exit marks | Yes | 5 | ||
Emergency light should be battery backup | Improve | 3 | ||
Emergency Diagram | Yes | 5 | ||
Fire extinguishers should sufficient and appropriate | Yes | 5 | ||
Fire Fighting training | Improved | 3 | ||
Fire extinguishers should clearly mark and visible | Yes | 5 | ||
Fire alarm system | Yes | 5 | ||
Electrical Channel are covered | No | 2 | ||
Machine maintains | Yes | 2 | ||
Machine and high temperature machines kept distance from work station | Yes | 2 |
Employee should wear appropriate personal protective equipment | No | 2 | ||
Doctor and Nurse | Yes | 5 | ||
Accident Record | Yes | 5 |
Table 3.25 The overall observation shows that the factory has established a complete ‘health & safety’ policy & procedures. The production floor was quite clean & spacious. Evacuation maps were available in all areas. Sufficient drinking water was provided on the production floors. Fire extinguishers were also properly charged and ready for use. However, the overall health & safety condition of the factory was found to be satisfactory and the issues identified during the visit which are detailed in the below point.
- The overall observation shows that the factory has established a complete ‘health & safety’ policy & procedures. The production floor was quite clean & spacious. Evacuation maps were available in all areas. Sufficient drinking water was provided on the production floors. Fire extinguishers were also properly charged and ready for use. However, the overall health & safety condition of the factory was found to be satisfactory and the issues identified during the visit which are detailed in the below point.
- The facility has no washing facility available in the child care room. There is no exhaust fan in the children’s room and there is no window.
- The factory is keeping a record of injury but no system in place to analyze the injury & take corrective action by identifying root cause which will improve occupational health and safety.
4. Freedom of Association:
Table 3.26- Freedom of Association in 2019
Name of the law | Correct | Not Correct | Improve Needed | Grade |
Legal rights | No | 3 |
Safety committee | Yes | 5 | ||
Worker welfare committee | Yes | 5 |
Table 3.26 Workers are not well aware of their legal rights responsibilities. Noted that the factory did not provide a complete job description to the workers for informing them about their responsibility.Workers also do not have any idea about their entitlement of leave in a year gratuity/service benefit and annual leave settlement during the completion of the job.
5. Others:
Table 3.27- others rules 2019
Name of the law | Correct | Not Correct | Improve Needed | Grade |
Factory License | Yes | 5 | ||
EPB | Yes | 5 | ||
Trade license | Yes | 5 | ||
ERC | Yes | 5 | ||
IRC | Yes | 5 | ||
Compressor Machine | Yes | 5 |
No Discrimination | Yes | 5 | ||
Working Hours maintain | Yes | 5 |
Table 3.27 The overall observations shows that the factory has maintained a record-keeping system and was provided necessary documents to the audit team for review. The factory has legal licenses and permits to operate the facility approved by the concerned authority. Management was transparent during the entire period of audit and they showed a positive attitude and was supportive to the auditor during the site visit. They were dedicated to maintaining good business relations with their business partners and we’re committed to fulfilling their expectations.
3.7 BSCI full audit report:
Table 3.28 BSCI audit full report 2019
Name of laws | Correct | Not- correct | Improvement | Remarks |
Social management system and cascade effect | Y | N | 4(D) | |
Workers involvement and protection | Y | N | 4(D) | |
Te rights of freedom of association | Y | 5(A) | ||
No discrimination | Y | 5(A) | ||
Fair Remuneration | Y | 5(A) | ||
Decent working hours | Y | 5(A) | ||
Occupational Health and safety | Y | N | 4(B) | |
No child labour | Y | 5(A) | ||
Special protection for young workers | Y | 5(A) | ||
No precarious employment | Y | 5(A) |
No bonded labour | Y | 5(A) | ||
Protection of the environment | Y | N/R | 3(C) | |
Ethical business behavior | Y | 5(A) |
Shows that the BSCI audit report of 2019 of Clamoon Garments, where it was shown that, their management system needs to be improved and workers protection performance also needs to be improved. Documentations are quite good in this industry. Working time is perfect. Compensation is quite good. Child labor isn’t funded. No forced labor was founded in the garments. Discriminations are not founded in the company. The working condition is good enough. Health and facilities are not quite good because environment performance is also needed to be improved.
3.8 BOND certificate
Table 3.29- Bond Certificate 2017-2019
Name of documents | YES | NO |
Article of memorandum | Y | |
TIN certificate | Y | |
Owner TIN Certificate | Y | |
Trade License | Y | |
Vat Registration certificate | Y | |
Money Exchange Certificate | Y | |
IRC | Y | |
ERC | Y | |
BGMEA certificate | Y | |
EPD certificate | Y | |
Building Plan | Y | |
Fire License | Y | |
Fire Insurance | Y | |
Boiler License | Y | |
List of machines | Y | |
Back to back L/C | Y | |
Bank Solvency Certificate | Y | |
Machine Certificate | Y | |
Factory Profile | Y | |
Risk Bond | Y | |
Lean Bank Report | Y | |
Owner TIN Copy | Y |
Received an application along (1) Treasury chalans (original copy) showing the bond license renewal fee of 10,000/- (2) 15% vat (Tk. 1,500/-) (3) IRC/ERC (4) Trade license (5) House rent agreement copy (6) Building ownership document duly notarized.
3.9 BGMEA Certificate
A. BGMEA certificate in 2019
Table: 3.30- BGMEA membership 2019
Requirements | Yes | No |
Application on company letter head pad to Secretary General, BGMEA for Provisional Membership | Yes | |
Duly filled up Prescribed Application for Membership Form of BGMEA. | Yes | |
Registration of DOT (Department of Textile) / BOI (Board of Investment) | Yes | |
Specimen Signature of Board of Directors /Managing Partners/ Proprietor with 2 Copy passport size Photographs of each attested by Lien Bank. | Yes | |
Copy of Memorandum & Articles of Association & Incorporation Certificate for Pvt. Limited Company. | Yes | |
Copy of up to date Trade License. | Yes | |
Copy of Fire License. | Yes | |
Copy of TIN Certificate. | Yes | |
List of Machineries (On Company letter head pad). | Yes | |
Copy of L/C of Machinery, Commercial Invoice, Bills | Yes | |
Copy of Deed Agreement with Land Owner/ Land ownership documents | Yes | |
Copy of Soil Test Report & details of issuing company | Yes | |
Copy of Approved Building Plan.( Architectural Design) | Yes | |
Copy of Structural Design signed by IEB registered Engineer | Yes | |
IEB registered Engineer (May be partial/Full) | Yes | |
Factory Lay-Out Plan | Yes |
Table 3.30The overall observations shows that the factory has maintained a record-keeping system and was provided necessary documents to the audit team for review. The factory has legal licenses and permits to operate the facility approved by the concerned authority. Where it was shown that Clamoon garments ltd have their all criteria to achieve BGMEA certifications in provisional steps. They have legal documents to show BGMEA.
B. BGMEA Permanent Certificate in 2019
Table 3.31- BGMEA permanent report 2019
Requirements | Yes | No |
Application on company letter head pad to Secretary General, BGMEA for Permanent Membership | Yes | |
Copy of ERC Certificate. | Yes | |
Copy of IRC Certificate. | Yes | |
Workers BIO Metric database certificate (provided by BGMEA). | Yes | |
Worker Group Insurance Certificate (provided by BGMEA), {If required} | Yes | |
Bond License | Yes |
Table 3.31 Shows that the ILO audit report of Clamoon garments ltd. Where it was shown that BGMEA has done the provisional audit and they stay their certificate.
RESULTS AND DISCUSSION
BSCI Audit Report:
Table 4.1-Law and Factory Policy: (Garments A, B)
Name of the law | Factory A | Factory B | |||
2009 | 2013 | 2018 | 2018 | 2019 | |
Posted current rules and regulations | 1 | 2 | 2 | 5 | 5 |
Employee handbook | 1 | 1 | 2 | 5 | 5 |
Employee Personal files | 1 | 1 | 2 | 5 | 5 |
Appointment letter and ID card | 1 | 1 | 1 | 5 | 5 |
From table 4.1, here we are observed that,
- Garments A have some issue in rules and regulations in 2009, and Garments B has not issued is rules and regulations. But garments A have improved their rules and regulation in 2013-2018
- Garments A have some issue in the handbook, some are missing in workers but, Garments B has fulfilled their handbook issue.
- Garments A have some issue in personal files, some are missing in workers but, Garments B has fulfilled their personal files issue.
- Garments A have some issue in Appointment letter and ID card issue, some are missing in workers but, Garments B has fulfilled their Appointment letter and ID card issue.
B. Child Labour Policy:
Table 4.2- Child Labour Policy (Garments A, B)
Name of the law | Factory A | Factory B | |||
2009 | 2013 | 2018 | 2018 | 2019 | |
Legal minimum working age in this country (18 years old) | 1 | 1 | 2 | 5 | 5 |
Verify the age of job applicants | 1 | 2 | 2 | 5 | 5 |
Maintain an age record for all employee | 1 | 1 | 1 | 5 | 5 |
Protect from the child labor | 1 | 1 | 1 | N/A | N/A |
From table 4.2, here we have seen the two garments child and labor policy
- Legal minimum working age in this country (18 years old)- In 2009 and 2013, their performance is good at working age. But in 2017 they try to develop this point and start the “No child labor” campaign. And the result of the 2018 audit is satisfactory. Garments B have not any issue in these sections.
- Verify the age of job applicants- First 2009, they take the chairman certificate. But this certificate is not enough to verify age. Then they improve their criteria. Only a national identity cardholder can apply for the job or birth certificate holder. Then they can verify the age easily. 2013 and 2018 they improve this sector. Garments B have not any issue in these sections.
- Maintain an age record for all employee- Factory workers are non-stable in their working sector. To maintain all records is quite impossible. But they have a file storage room too. But this is very difficult for garments. Garments B have not any issue in these sections.
- Protect from the child labor- This factory is protected from child labor. They maintain the government rules. Garments B have not any issue in these sections.
C. Health and Safety:
Table 4.3- Health and safety (Garments A, B)
Name of the law | Factory A | Factory B | |||
2009 | 2013 | 2018 | 2018 | 2019 | |
Exit doors should open | 2 | 2 | 2 | 5 | 5 |
Exit signs | 1 | 2 | 2 | 5 | 5 |
Exit marks | 1 | 1 | 2 | 5 | 5 |
Emergency light should be battery backup | 1 | 1 | 2 | 2 | 3 |
Emergency Diagram | 1 | 2 | 2 | 5 | 5 |
Fire extinguishers should sufficient and appropriate | 1 | 1 | 1 | 5 | 5 |
Fire Fighting training | 1 | 2 | 2 | 4 | 3 |
Fire extinguishers should clearly mark and visible | 1 | 1 | 2 | 5 | 5 |
Fire drills should be conducted at least twice a year with records and photos | 1 | 1 | 1 | 5 | 5 |
Fire alarm system | 1 | 2 | 2 | 2 | 2 |
Electrical Channel are covered | 1 | 1 | 2 | 2 | 2 |
Machine maintains | 1 | 2 | 2 | 2 | 2 |
Machine and high temperature machines kept distance from work station | 1 | 2 | 2 | 2 | 2 |
Employee should wear appropriate personal protective equipment | 1 | 1 | 1 | 5 | 5 |
Doctor and Nurse | 1 | 1 | 1 | 5 | 5 |
Accident Record | 1 | 2 | 2 |
Table 4.3 shows that, health and safety report of the two garments.
- Exit doors should open- When Morshed Limited builds their permanent building, they design their factory with exit doors. And doors always open. This door always maintains security and CCTV. And Clamoon garments ltd have no issue in exit doors.
- Exit signs: Exit sing is a mark that indicates the doors. In 2009, some doors have without exit signs but in 2013 and 2018 they develop their all doors with exit signs. And Clemson garments ltd have no issue in exit signs.
- Exit marks- Exit marks are one kind of sign which indicates the path of the exit doors. In 2009 and 2013 they have some miss marks but in 2018 developed this point. And Clamoon garments ltd have no issue in exit marks.
- Emergency light should be battery backup- In 2009 and 2013, they work with direct electricity but they realized that they need an extra battery. If any kind of accident happens then the battery can help to run out all workers. So 2018 they generate extra battery. And Clamoon garments ltd has some issues in 2018 and 2019. They have not properly in enough emergency light in their garments.
- Emergency Diagram- 2009, there was an exit point only sewing section. But in 2013 they fixed every floor emergency diagram. And Clamoon garments ltd have no issue in the exit diagram.
- Fire extinguishers should sufficient and appropriate- Morshed limited is about 14000 square meter feet. So they need lots of the number of fire extinguishers in the factory. They have all the equipment. But some fire extinguisher is out of order. And Clamoon garments ltd have no issue in the fire extinguisher.
- Fire drills should be conducted at least twice a year with records and photos- Every year they create fire drills. And make a fire team. And Morshed limited carry the same result in 2009,2013 and 2018. And Clamoon garments ltd have no documents in fire drills.
- Fire alarm system- In 2009, their fire alarm works in the sewing and cutting section. But in 2013 and 2018 they improve their system. They ensure fire alarm in full factory. And Clamoon garments ltd have no issue in the fire alarm system.
- Electrical Channel is covered- the Electrical channel is covered means no electric equipment is shown open in the factory. morshed limited ensure all electrical types of equipment are covered. And Clamoon garments ltd have some issues in these points, they need to be improving.
- The machine maintains- At least one hour given to every machine rest. Because sewing or other machines run continuously in the factory. If the machines do not find any maintains time then any kind of accident will be created. 2009,2013 and 2018 Morshed limited pass the criteria. And Clamoon garments ltd have some issue in this sector and need a machine maintains the room.
- Machine and high-temperature machines kept a distance from work station- Morshed limited runs boiler which is produce high temperatures. In 2009, they have no extra boiler room but they keep it in a safe position. But in 2013 they make an extra boiler room in the factory. And Clamoon garments ltd have to need to improve in this sector.
- The employee should wear appropriate personal protective equipment- Worker uses their protective equipment when they work high-temperature machine. Otherwise, they do not wear types of equipment. And Clamoon garments ltd have to need to improve in this sector.
- Doctor and Nurse- Doctor comes to the garments one day in a week, but the nurse is working continuously. And they arrange a room for all workers. And Clamoon garments ltd have good quality doctor and nurse.
- Accident Record- Morshed limited carry all accident records in a file. In 2009 they record only worker accident but in 2013 and 2018 they take also machine accidents (if any needle brake then it should be collected for the replace) And Clamoon garments ltd have all accident records in all years.
D. Freedom of association
Table 4.4- Freedom of association (Garments A, B)
Name of law | Factory A | Factory B | |||
2009 | 2013 | 2018 | 2018 | 2019 | |
Worker elected committee | N/R | 1 | 2 | 3 | 3 |
Safety committee | 1 | 1 | 2 | 5 | 5 |
Worker welfare committee | 1 | 2 | 2 | 5 | 5 |
Table 4.4 shows that, the situation of freedom of association of Morshed limited.
- Worker elected committee- At first audit 2009, their worker committee do not ready yet. So they can present the worker committee. But in 2013 and 2018 they have worker committee and 2018 the committee going very strong position. And Clamoon garments ltd has good in worker elected committee.
- Clamoon garments ltd has developed legal rights in their garments.
- Safety committee- They have a safety committee to create fire drill, safety campaign, etc. in 2009 they have done it once a time in a year but 2018 they turn into 2 times in a year. Clamoon garments in good positions in the safety committee.
- Worker welfare committee- In 2009 they haven’t any proper committee; they break their committee and reunion WWC in 2012 and present the full committee in the 2013 audit and also 2018 audit. Clamoon garments in good positions in the Worker welfare committee.
E. Others
Table 4.5- Other certificates (Garments A, B)
Name of the law | Factory A | Factory B | |||
2009 | 2013 | 2018 | 2018 | 2019 | |
Factory License | 2 | 2 | 2 | 5 | 5 |
EPB | 2 | 2 | 2 | 5 | 5 |
Trade license | 2 | 2 | 2 | 5 | 5 |
ERC | 2 | 2 | 2 | 5 | 5 |
IRC | 2 | 2 | 2 | 5 | 5 |
Compressor Machine | 2 | 2 | 2 | 5 | 5 |
No Discrimination | 2 | 2 | 2 | 5 | 5 |
Working Hours maintain | 2 | 2 | 2 | 5 | 5 |
From table 4.5 Here are mentioned some certificates which are play very important roles in the garments factory.
Morshed limited and Clamoon Garments ltd has all license, tax token and certificates up to date. And BSCI audit has no complained in those sections. BSCI oriented picture:
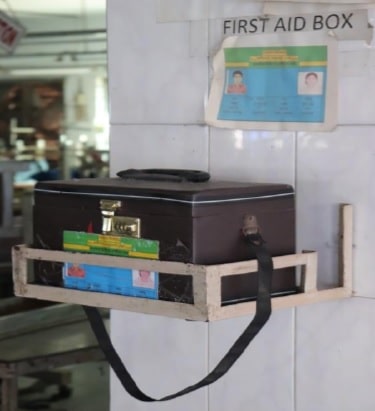
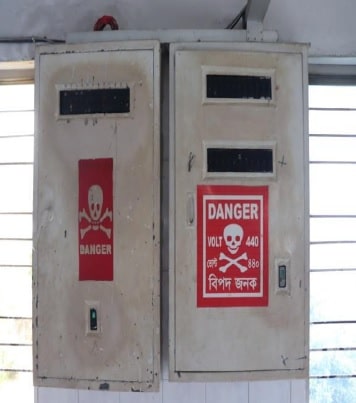
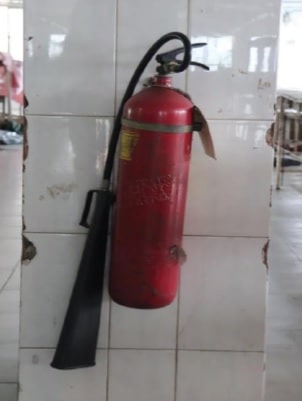
BSCI report:
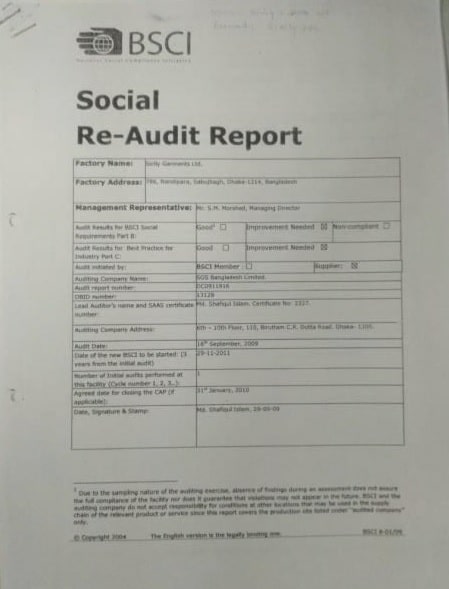
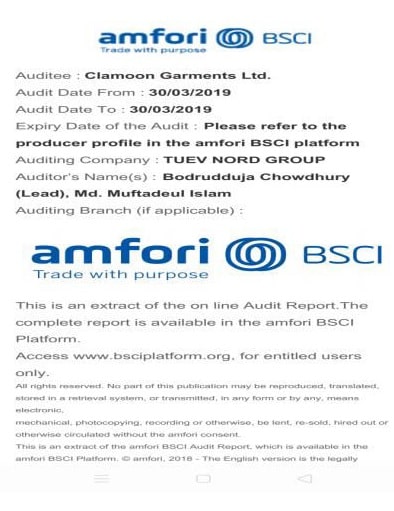
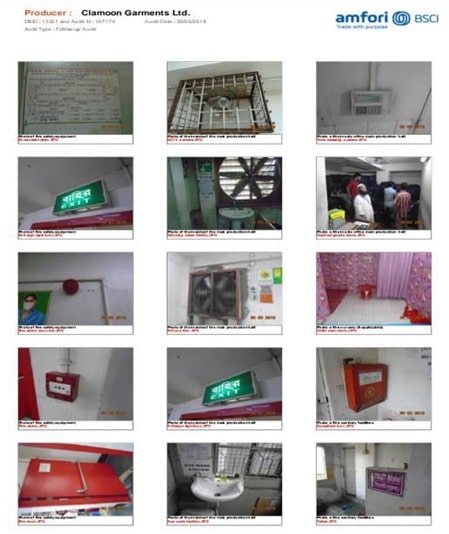
ILO Audit Report:
Table 4.6- ILO audit report (Garments A):
Here Y=Yes. N=No, I= Improvement
Name of the law | 2013 | 2018 |
Working Hours | Y | Y |
Conditions of employment | I | Y |
Accommodation | I | Y |
Recreation Facilities | Y | Y |
Food and Catering | Y | Y |
Accident Prevention | Y | Y |
Heath Protection | I | Y |
Medical Care | I | Y |
Security | Y | Y |
From table 4.6, Here I am observing the ILO audit report in Morshed Limited.
- Working Hours- They maintain 8 hours working hours with a 1-hour lunch break and 2 hours overtime.
- Conditions of employment- In 2013, they face some limitations in the factory. and they do not fulfill the criteria of the employment conditions. But in 2018 they overcome their situations and perform better than previous times.
- Accommodation- This law is made for worker children. In 2013 there haven’t any room for children and babies but in 2017 they develop babies care rooms and they present to ILO 2018 audit.
- Recreation Facilities- Every year they organize a picnic and new year celebrations.
- Food and Catering- They have kitchen room facilities in the factory, and also have a canteen in the factory with is open for all.
- Accident Prevention- Morshed limited ensure the fast aid box to every floor and doctor treatment in the factory.
- Heath Protection- They organize many free seminars for workers in Heath Protection. How to protect their health in garment conditions.
- Medical Care- They have own doctor. But in 2013 they haven’t any good doctor. They ensure the good doctor in 2017 and pass the 2018 ILO audit.
- Security- They ensure all kinds of instruments for workers’ security. Fire drills, emergency exit and hose pipe for fire. And CCTV for maintains.
Table 4.7- ILO audit report B (Garments A):
Name of the law | 2013 | 2018 |
Minimum Age | I | Y |
Medical Certification | I | Y |
Qualifications of workers | Y | Y |
Employee Agreements | Y | Y |
Hours of working rest | Y | Y |
Worker certificate (NID or Local Certificate) | Y | Y |
Document of safety | I | Y |
Accommodation | I | Y |
Recreational Facilities | Y | Y |
Food | Y | Y |
Safety | Y | Y |
Medi Care | I | Y |
Compliant Procedure | I | Y |
Payment | Y | Y |
From table 4.7, Here I am observing the ILO audit report in Morshed Limited.
- Minimum Age- They ensue minimum age 18 properly in 2018
- Medical Certification- They ensure to all workers medial certification in 2018
- Qualifications of workers- They prefer minimum class five for job
- Employee Agreements- They have agreements in their files
- Worker certificate (NID or Local Certificate)- They ensure the worker certificates (NID)
- Document of safety- They ensure valid third-person data, who can give the safety of workers.
- Accommodation-This law is made for worker children. In 2013 there haven’t any room for children and babies but in 2017 they develop babies care rooms and they present to ILO 2018 audit.
- Recreational Facilities- Every year they organize a picnic and new year celebrations.
- Food and Catering- They have kitchen room facilities in the factory, and also have a canteen in the factory with is open for all.
- Food- They have kitchen room facilities in the factory, and also have a canteen in the factory with is open for all.
- Safety- They ensure all kinds of instruments for worker’s security. Fire drills, emergency exit and hose pipe for fire. And CCTV for maintains.
- Medi Care- They have own doctor. But in 2013 they haven’t any good doctor. They ensure the good doctor in 2017 and pass the 2018 ILO audit.
- Complaint Procedure- every floor has a compline box. Which is open for all.
- Payment- They give workers payment in 5th working days in a month.
Bond Certificate
Table 4.8- Bond Certificate (Garments A, B)
Name of documents | Factory A | Factory B | ||
2013 | 2018 | 2017 | 2019 | |
Article of memorandum | Y | Y | Y | Y |
TIN certificate | Y | Y | Y | Y |
Owner TIN Certificate | Y | Y | Y | Y |
Trade License | Y | Y | Y | Y |
Vat Registration certificate | Y | Y | Y | Y |
Money Exchange Certificate | Y | Y | Y | Y |
IRC | Y | Y | Y | Y |
ERC | Y | Y | Y | Y |
BGMEA certificate | Y | Y | Y | Y |
EPD certificate | Y | Y | Y | Y |
Building Plan | Y | Y | Y | Y |
Fire License | Y | Y | Y | Y |
Fire Insurance | Y | Y | Y | Y |
Boiler License | Y | Y | Y | Y |
List of machines | Y | Y | Y | Y |
Back to back L/C | Y | Y | Y | Y |
Bank Solvency Certificate | Y | Y | Y | Y |
Machine Certificate | Y | Y | Y | Y |
Factory Profile | Y | Y | Y | Y |
Risk Bond | Y | Y | Y | Y |
Lean Bank Report | Y | Y | Y | Y |
Owner TIN Copy | Y | Y | Y | Y |
From table 4.8 show that, Two garments has up to date bond license in their factory. And they are regularly renew it.
Bond license:
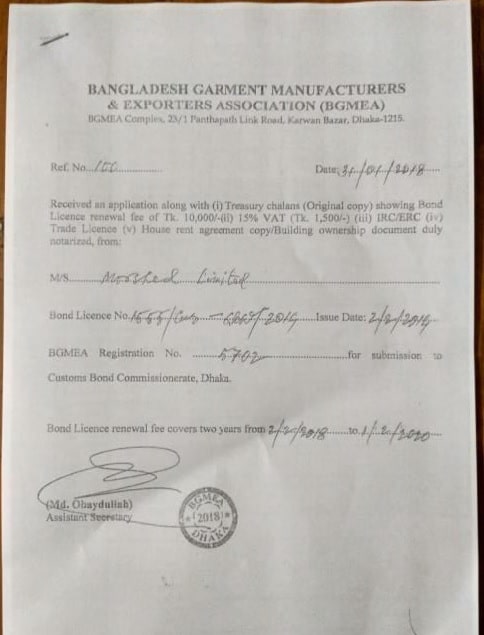
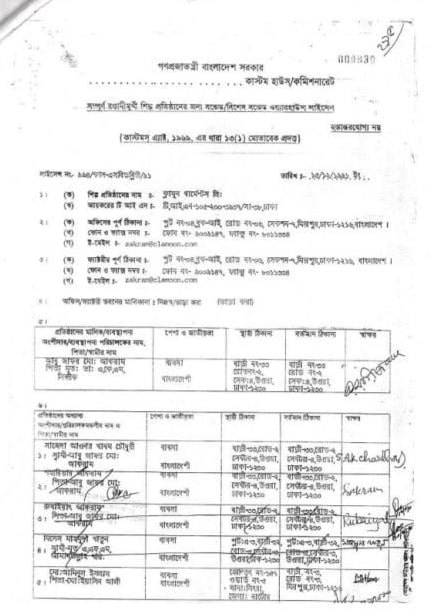
BGMEA Certificate
Table 4.9- BGMEA Certificate (Garments A, B)
Requirements | Factory A | Factory B | ||
2013 | 2018 | 2013 | 2018 | |
Application on company letter head pad to Secretary General, BGMEA for Provisional Membership | Yes | Yes | Yes | Yes |
Duly filled up Prescribed Application for Membership Form of BGMEA. | Yes | Yes | Yes | Yes |
Registration of DOT (Department of Textile) / BOI (Board of Investment) | Yes | Yes | Yes | Yes |
Specimen Signature of Board of Directors /Managing Partners/ Proprietor with 2 Copy passport size Photographs of each attested by Lien Bank. | Yes | Yes | Yes | Yes |
Copy of Memorandum & Articles of Association & Incorporation Certificate for Pvt. Limited Company. | Yes | Yes | Yes | Yes |
Copy of National ID / Passport (Board of Directors /Managing Partners/ Proprietor). | Yes | Yes | Yes | Yes |
Copy of up to date Trade License. | Yes | Yes | Yes | Yes |
Copy of Fire License. | Yes | Yes | Yes | Yes |
Copy of TIN Certificate. | Yes | Yes | Yes | Yes |
List of Machineries (On Company letter head pad). | Yes | Yes | Yes | Yes |
Copy of L/C of Machinery, Commercial Invoice, Bill of Lading & Bill of Entry ( if available). | Yes | Yes | Yes | Yes |
Copy of Deed Agreement with Land Owner/ Land ownership documents | Yes | Yes | Yes | Yes |
Copy of Soil Test Report & details of issuing company | Yes | Yes | Yes | Yes |
Copy of Approved Building Plan.( Architectural Design) | Yes | Yes | Yes | Yes |
Copy of Structural Design signed by IEB registered Engineer | Yes | Yes | Yes | Yes |
Completion Certificate provided by IEB registered Engineer (May be partial/Full) | Yes | Yes | Yes | Yes |
Factory Lay-Out Plan | Yes | Yes | Yes | Yes |
Table 4.10- BGMEA Certificate(Garments A, B) (Permanent)
Requirements | Factory A | Factory B | ||
2013 | 2018 | 2013 | 2018 | |
Application on company letter head pad to Secretary General, BGMEA for Permanent Membership | Yes | Yes | Yes | Yes |
Copy of ERC Certificate. | Yes | Yes | Yes | Yes |
Copy of IRC Certificate. | Yes | Yes | Yes | Yes |
Workers BIO Metric database certificate (provided by BGMEA). | Yes | Yes | Yes | Yes |
Worker Group Insurance Certificate (provided by BGMEA), {If required} | Yes | Yes | Yes | Yes |
Bond License | Yes | Yes | Yes | Yes |
From table 4.9 – 4.10Morshed limited and Clamoon Garments ltd collect all the licenses and insurance to achieve BGMEA certificates. These rules and regulations are basically for new BGMEA membership. But every year they need to ensure these things first. Then they can apply for permanent membership or renew the certificates.
BGMEA certificate:
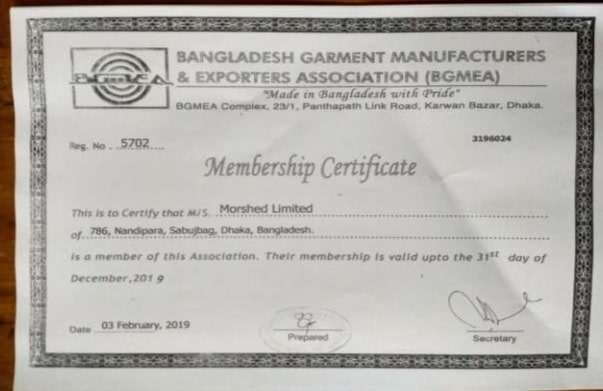
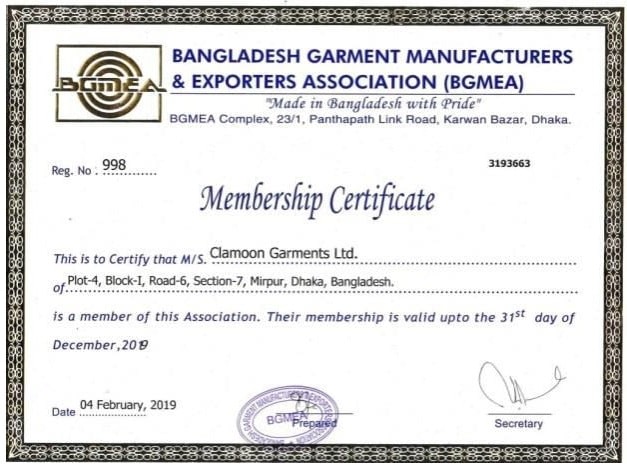
Others:
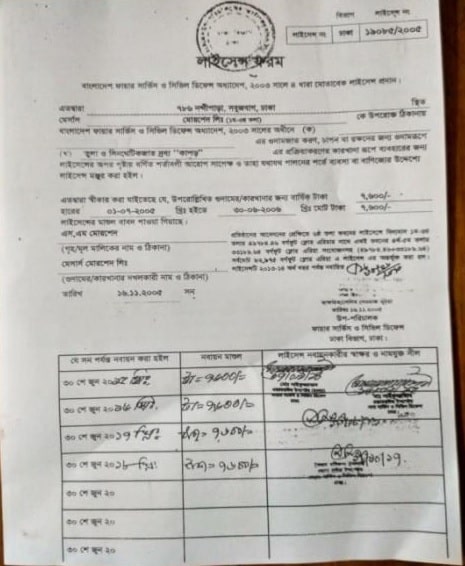
Fig: 12 IRC certificate
CONCLUSION
This report shows analytical audit data on factory policy, labor policy, child labor policy, BGMEA, ILO, and BOND. And the report indicates the different garments industry’s situations. This paper is concluded as-
- Factory and garments policy in garments B is better than garments A.
- Child labour policy in garments A is better than garments B.
- Both garments need improvements in health and safety.
- ILO is a good position in garments A.
- BGMEA report is a good condition in both garments.
- BOND certificates are up to date in both garments.
Further study regarding this report helps to find out the rules and regulations of BSCI, BGMEA, ILO, and Bond. And find out the development area
REFERANCES:
- https://textilelearner.net/garment-industry-compliance-system/
- https://bellatory.com/fashion-industry/Ready-to-Wear-A-Short-History-of-the-Garment-Industry
- https://bellatory.com/fashion-industry/Ready-to-Wear-A-Short-History-of-the-Garment-Industry
- https://en.wikipedia.org/wiki/Jamdani
- https://qz.com/577024/the-problem-in-bangladeshs-garment-industry-is-three-times- bigger-than-anyone-suspected/
- https://bizfluent.com/about-6701168-iso-compliant-.html
- https://www.isocertificationconsultants.co.in/pages/bsci-certification
- https://www.ilo.org/global/about-the-ilo/lang–en/index.htm
- http://www.bgmea.com.bd/home/faq/faqs