Dyeing of Cotton Fabric with Reactive Dyes
Mustafizur Rahman
Department in Textile Engineering
Port City International University
Email: mdmustafiz898@gmail.com
The Development of Reactive Dyes:
The dyeing of cotton with direct dyes has poor washing fastness. Because it has a weak bond with the dye molecules to the cellulose polymer chains. So direct dyes can easily come out from the fabric molecules. For best washing fastness a insoluble pigment is attaching it with the cotton fibers. This type of dyeing process of vat and azoic dyes is much more difficult than direct dyeing.
The idea of forming a dye molecule covalent bond with the reactive group in a fiber originated in the early 1900s. Various chemicals were found that reacted with the hydroxyl group of cellulose and eventually, they converted into colored cellulosic derivatives. Cellulose was a relatively unreactive polymer. As a result, a number of dyes are known to be capable of forming bonds with wool. Initially, cotton was not considered as fiber-reactive dye, although it has good washing fastness.
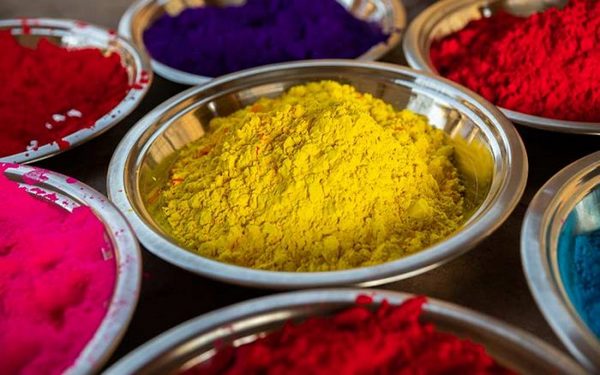
In 1955, developed a procedure for dyeing cotton with fiber-reactive dyes. They established that dyeing cotton with these dyes under mild alkaline conditions resulted in reactive chlorine atom. The role of alkali is to cause acidic dissociation of some of the hydroxy groups of cellulose and it is the cellulosate ion that reacts with the dye.
The dyeing has very good washing fastness. The only possibility of bleeding dye from the cotton is after the hydrolysis of the covalent bond between the dye and the cellulose. Within five years of this development, all the major dyestuffs manufacturers were marketing reactive dyes of cotton and also for wool. Because of their good washing fastness, their bright shades, versatile batch and continuous dyeing method, reactive dyes have become one of the major classes of dye.
Reactive Dyes for Cotton:
Structure of reactive dyes for cotton:
The molecular structure of reactive dyes resemble those of acid and simple direct cotton dyes, but with an added reactive group. Typical structures such as azo a) anthraquinone b) triphenodioxazine or copper phthalocyanine chromophores
The structural key features of reactive dyes are the chromophore system, the sulphonate group for water solubility, the reactive group and the bridging group that attaches the reactive group either directly to the chromophore group or to some other part of the dye molecule. Each of these structural features can influence the dyeing and fastness properties in dyeing textile manufacturing process.
Most commercial range of reactive dyes have a complete gamut of colors, many of which are particularly bright. Reactive dyes often have simple structures that can be synthesized with a minimum of colored isomers and byproducts that tend to dull the shade of the more complex polazo direct dyes. Some colors are difficult to obtain with simple chromophores. Dark blue and navy reactive dyes are often rather dull copper complexes of azo dyes and the production of bright green reactive dyes remains a problem.
A whole range of possible fiber reactive groups has been examined and evaluated by the dyestuff manufacturers. The final choices for commercial dyes are limited by a number of constraints. The reactive group must exhibit adequate reactivity towards water that can deactivate it by htdrolysis. The hydrolysis of the dye’s reactive group is similar to it’s reaction with cellulose but involves a hydroxyl ion in water rather than a cellulose ion in the fiber. In addition, the dye fiber bond, once formed should have adequate stability withstand repeated washing. Other factors involved are the ease of manufacture, the dye stability during storage and the cost of the final reactive dye
HO-+ Dye -Cl = Dye-OH + Cl-
Types of Reactive Dyes:
- Those reacting with cellulose by nucleophilic substitution of a chlorine, florine, methyl sulphone or nicotinyl leaving group activated by an adjacent nitrogen atom in a heterocyclic ring.
- Those reacting with nucleophilic addition to a carbon-carbon double bond, usually activated by an adjacent eletron attacking sulphone group. This type of vinyl sulphone group is usually generated in the dyebath by elimination of sulphate ion from a 2- sulphatoethylsulphone precursor group with alkali.
Although many of the early reactive dyes had only one reactive group in the dyestuff molecule, many of the newer reactive dyes are bifunction with two or more identical or different reactive groups. Some typical fibers in reactive groups and the commonly used abbreviations for these groups. Dyes with nicotinyltriazine reactive groups react with cotton on heating under neutral conditions.
Basic Principle of Dyeing Cotton with Reactive Dyes:
The relatively simple procedure for batch dyeing of cotton materials with reactive dyes is still used for all types of reactive dyes irrespective of their particular reactive group. Dyeing is commenced in a neutral solution, often in the presence of salt to promote exhaustion of the dye onto the cotton. During this period, the dye does not react with the fiber and migration from fiber to fiber is possible. Then, an appropriate alkali is added to the dyebath to increase its pH. This initiates the desired dye fiber reaction. The hydroxyl group in cellulose are weakly acidic and absorption of hydroxide ions causes some dissociation, forming cellulosate ions. It is these that react with the dye by nucleophilic addition or substitution. In general, the lower the reactivity of the reactive groups towards the alkaline cellulose, the higher the final dyeing temperature and the higher the PH of the dye bath.
Unfortunately, under alkaline conditions, hydroxide ions also react with the reactive group of the dye. This produces the hydrolyzed dye, which is incapable of reacting with the fiber. Hydrolysis of the dye is slower than the reaction with the alkaline cotton but it is significant and reduces the efficiency of the fixation process. After dyeing, an unreacted and hydrolyzed dye present in the cotton must be removed by through washing. This ensures that no color will bleed from the cotton on subsequent washing during use. The higher the substantivity of the reactive dye for the cotton, the more difficult to wash out unfixed dye from the material. Many of the first reactive dyes had quite simple molecular structures and low substantivity for cotton, so that the removal of hydrolysed dye from the material by washing was relatively easy. This is not necessarily true for reactive dyes of more complicated molecular structure.
Dye Reactivity, Storage and Application of Reactive Dyes:
The reactive groups of various types of dye have different chemical structures and show a wide range of reactivities. They were originally divided into cold and hot dyeing types but many current ranges would be better called warm dyeing. The most reactive dye such as DCT reactive dyes are applied at lower temperature (20-40)°C and only require a weak alkali such as NaHCO3 or Na2CO3 for fixation. The less reactive dyes such as MCT dyes, need higher temperatures (80-90)°C and stronger alkali such as Na2CO3 Plus NaOH. Many dyestuff manufacturers now market several ranges of reactive dyes for cotton, each with its own particular recommended dyeing procedure. Below are some examples based on the type of reactive grouping:
- Reactive Group (DCT)- Commercial name: (Procion MX) BASF – Reactivity(High) – Temp(25-40)°C
- Reactive Group (MCT)- Commercial name: (Procion H, Basilen) BASF & Cibacron (Ciba) – Reactivity- (Low) Temp(80-85)°C
- Reactive Group (MFT)- Commercial name: (Cibacron F) Ciba – Reactivity (Moderate)- Temp(40-60)°C
- Reactive Group (DCQ)- Commercial name: (Levafiz E) Dystar- Reactivity (Low) – Temp(50-70)°C
- Reactive Group (DFCP)- Commercial name: (Drimarene K) Clarient, (Levafix EA) Dystar- Reactivity (moderate to high) – Temp(30-40)°C
- Reactive Group (VS)- Commercial name: (Remazol) Dystar -Reactivity- (Moderate)- Temp(40-60)°C
- Reactive Group (TCP)- Commercial name: (Drimarene X) Clarient- Reactivity- (Low) – Temp ( 80-95)°C
- Reactive Group (NT)- Commercial name: (Kayacelon React) Nippon Kayaku- Reactivity- (Moderate to High) – Temp (100-130)°C
Above reactive group are reacting under neutral conditions. Because most reactive dyes are prone to hydrolysis, their handling and use requires care. Most are readily water soluble and the dye solution is prepared in the usual way by pasting it with water and then adding more water. The temperature of the water used depends upon the ease of solution and the reactivity of the dye. Hot water is not recommended for dissolving dyes of high reactivity, because the risk of the hydrolysis of the reactive group, but it is suitable for the less reactive dyes. Once the dye solution has been prepared, it cannot be stored for later without some risk of hydrolysis of the reactive group. This decreases its fixation ability and it is a particular problem with most of the reactive dye. Dyes containing 2- sulphatoethylsulphone group, however can be dissolved in neutral water in the boil without risk of hydrolysis. Formation of the reactive vinyl sulphone group requires the addition of an alkali.
Reactive dyes for printing are usually dyes of low reactivity so that the print paste can be stored for some time at room temperature without deterioration from hydrolysis of the reactive group. Reactive dyes of low reactivity and relatively high substantivity are valuable for dyeing using long liquor ratios, using a winch machine. Exhaust dyeing with low reactivity dyes at the higher temperature required for fixation allows better penetration of the dyes into the cotton fibers. For continuous dyeing of reactive dyes stabilized liquid forms are available. Although these contain special PH buffers and stabilizers to minimize the hydrolysis reaction, they only have a limited shelf life
Many commercial reactive dyes are dusty powders but all physical forms must be handled with care. These dyes react with the amino groups in proteins in the skin and on mucous surfaces. Inhalation of the dust is dangerous and a dust mask is obligatory during handling. Reactive dye powders and grains are sometimes hygroscopic and drums must be carefully resealed. Most reactive dyes have a limited storage period, after which some deterioration can be expected. Standardization and comparison of reactive dye powders or liquids cannot be done by the usual spectrophotometric procedure involving absorbance measurements of standard solutions. Both the reactive dyes and its hydrolyzed forms are equally colored. But only the former is capable of reacting with the cellulose during dyeing. Chromatographic techniques usually allow separation and quantitative measurements of the relative amount of a reactive dye and its hydrolysis product in a given dye.
Fastness Properties of Reactive Dyes on Cellulosic Fibers:
In general, reactive dyes on cellulosic fibers give good dyeing with very good washing fastness and other wet processes. Apparent inferior fastness to washing is usually because of incomplete removal of unreacted and hydrolysed dye from the material by washing after dyeing. The presence of unfixed dye can easily be tested for by hot pressing a wet sample of the dyeing sandwiched between two pieces of dry white cotton. Color transfer to the white material indicates the presence of unfixed dye in the dyeing. It is more likely to be a problem for deep dyeing.
The use of reactive dyes is growing rapidly, faster than for any other dye application class. This is because these dyes also give dyeing of moderate to good washing fastness, allow relatively simple and diverse dyeing methods and are available in a range of bright colors. They have contributed significantly to the decline of direct cotton dyes. Their fastness properties, though generally good, do not match those of pigmented cotton dyed with vat dyes. In particular, the fastness to bleaching by chlorine and to a lesser extent by peroxide present in modern household detergnets, is often only moderate.
Evidence for Covalent Bond Formation of Reactive Group with Cellulose:
The good fastness to washing of dyeings with reactive dyes on cellulosic fibers is a consequence of the stable covalent bond formed between the dye’s reactive group and the cellulosic polymer. There is considerable evidence to support the formation of this dye-fiber bond. Dyeing is resistant to color stripping with hot aqueous pyridine, a solvent that effectively removes direct dyes from cotton. The dyeing of cotton obtained with bifunctional dyes often exhibit reduced swelling and decreased solubility in cuprammonium solution. A dye molecule with two reactive groups crosslinking two different cellulose chains would explain this. If the color of dyeing obtained with an azo-reactive dye is destroyed by chemical reduction with alkaline sodium hydrosulfite, which cleaves the azo dye into two primary aromatic amines, the amine remaining attached to the celllulose can be diazotized and coupled with an appropriate phenol to reform a colored fiber. Finally, bacterial degradation of reactive dyes cotton that depolymerizes the cellulose, but avoids breaking the dye-fiber bond, gives colored products containing the original dye still bonded to glucose.
Batch Dyeing of Cotton with Reactive Dyes in Textile Engineering:
Preparation for Dyeing of Reactive Dyes:
Level well-penetrated dyeings require careful preparation of the material. All sizing chemicals capable of reacting with the dye, such as starch or polyvinyl alcohol, must be removed from the material and any traces of residual alkali must be uniformly neutralized. Good alkali boiling to remove wax is essential for goods to be dyed with cold dyeing reactive dyes because the penetration of the dyes into the fibers is more difficult at lower dyeing temperatures. Reactive dyes often give such bright colors that bleaching may not be necessary. Once size has been removed, grey cotton goods can sometimes be simultaneously scoured and dyed using hot dyeing reactive dyes and an effective detergent. Because of the sensibility to bleaching by chlorine of some reactive dyes, over-chlorinated water must be avoided or treated with a reducing agent such as sodium bisulfite or thiosulphate.
The Three-Step Exhaust Dyeing Process of Reactive Dyes:
A typical exhaust dyeing process for cellulosic materials using reactive dyes has three distinct processes;
1. The initial exhaustion phase:
Dyeing is started in a neutral solution so that there is little likelihood fo the dye reacting with the cellulose. During this stage of dyeing, some reactive dyes will be absorbed by the fibers, the amount depending upon their substantivity. This dye is capable of migration to level dyeing. Sodium chlorite or sulphite will often be present initially or be added gradually to the dye bath during this phase to promote exhaustion. The temperature of the dyebath may be gradually increased to aid penetration of the dye into the fibers and to assist migration
2. The fixation phase:
After the initial exhaustion phase, the PH of the dye bath is increased by the complete or gradual addition of the appropriate type and amount of alkali. This caused the dissociation of some of the hydroxyl groups in the cellulose and in the nucleophilic cellulosate ions begin to react with the dye. The fixation process then results in additional dye absorption, to re-establish the dyeing equilibrium. Dye absorption from solution and reaction with the fiber then progress until no further dye is taken up. The variation of the dyebath exhaustion and the extent of fixation during a typical exhaust dyeing.
3. The post dyeing washing:
The rinsed dyieng contains dye bonded to the cellulose, absorbed but unreacted dye, as well as hydrolysed dye. There will also be residual alkali and salt. The latter are relatively easy to remove by successive rinsing in cold and then warm water. As much unfixed dye as possible must be washed out before dyeing. If this is not done, desorption of this dye during washing by the consumer can cause staining of other materials in the wash. Some unfixed dye is eliminated during the initial rinsing that removes alkali and salt. Through washing of the dyeing using a boiling detergent solution eliminated the remainder. The dyeing is finally rinsed in warm water. Soaping must often be repeated for deep dyeings or the residual unfixed dye must be complexed with a cationic agent.
You may also like: