Air Jet Weaving Machine:
Air jet weaving machine is one type of modern weaving machine with the highest weft insertion performance and are considered as the most productive in the manufacturing of light to medium weight fabrics, preferably made of cotton and certain man made fibers (sheets, shirting fabrics, linings, taffetas and satins in staple yarns of manmade fibers); it has anyway to be pointed out that technically positive results are obtained at present also with heavy weight fabrics (denims) and that some manufacturers produce also machine models for terry production. These machines are the ideal solution for those who want to produce bulk quantities of customized fabric styles. The weaving widths range generally from 190 to 400 cm. As regards the multicolor weft carrier, up to 8 different wefts can be fed. Figure 1 shows a modern air jet weaving machine.

It has however to be considered that a air jet weaving machine requires a high energy consumption to prepare the compressed air and that this consumption rises definitely with increasing loom width and running speed. The reduction in the energy consumption is in fact one of the main concerns of the manufacturers, and builds for the user an important selection criterion.
Features of Air Jet Weaving Machine:
- The air jet weaving machines are the weaving machines with the highest weft insertion performance.
- This loom is most productive in the manufacturing of light to medium weight fabrics.
- Preferably made of cotton and certain man-made fibers (sheets, shirting fabrics, linings, taffetas and satins in staple yarns of man-made fibers).
- The air jet loom has technically positive results are obtained at present also with heavy weight fabrics (denims) and that some manufacturers produce also machine models for terry production.
- These machines are the ideal solution for those who want to produce bulk quantities of customized fabric styles.
- The weaving widths range generally from 190 to 400 cm.
- As regards the multicolor weft carrier, up to 8 different wefts can be fed.
- The air jet weaving machines require a high energy consumption to prepare the compressed air.
- To build compressed air, this consumption rises definitely with increasing loom width and running speed.
- The air jet loom also has the robust frame structure.
- Productivity is an essential factor of air jet looms. For its smooth warp shed, a well-balanced beating system, the best weft insertion system.
- Another most important feature is the machine has low vibrations.
- Free drum pooling system provided with the yarn-advancing reel as standard. It stabilizes insertion with less yarn break age even at high-speed weaving or extra-wide weaving. Computerized controlling system that can be easily operated or supervision.
Working Principle of Air Jet Weaving Machine:
Air jet weaving is a type of weaving in which the filling yarn is inserted into the warp shed with compressed air. Figure 2 shows a schematic of air jet weaving utilizing a multiple nozzle system and profiled reed which is the most common configuration in the market. Yarn is drawn from a filling supply package by the filling feeder and each pick is measured for the filling insertion by means of a stopper. Upon release of the filling yarn by the stopper, the filling is fed into the reed tunnel via tandem and main nozzles. The tandem and main nozzle combination provides the initial acceleration, where the relay nozzles provide the high air velocity across the weave shed. Profiled reed provides guidance for the air and separates the filling yarn from the warp. A cutter is used to cut the yarn when the insertion is completed.
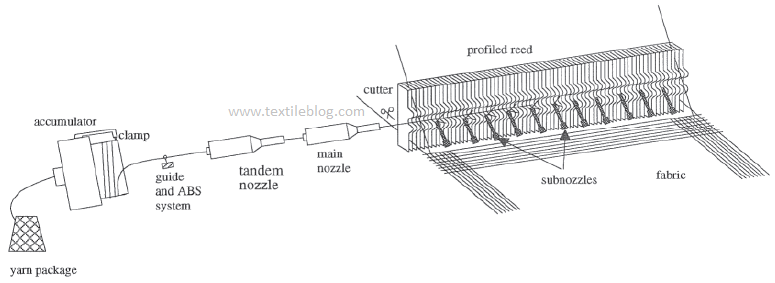
The operation principle is the following: the thread, prepared in a given length (corresponding to the reed width) by pre-measuring weft carriers (Figure 3), is launched through the shed by a jet of compressed air. The typology of the weft inserting medium (no mass in motion) permits high weft insertion rates (on an average 2000-2500 meters/min and 1000 strokes/min).
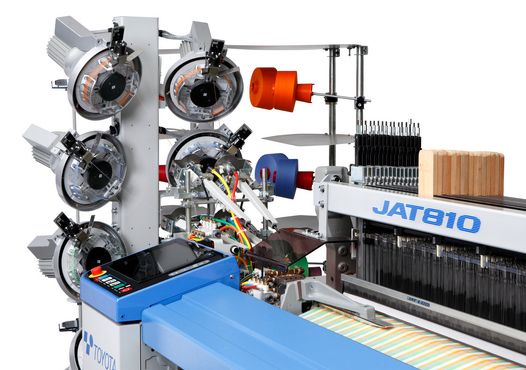
The air jet weaving machines require air ducts capable of maintaining an effective air flow on the whole weaving width. To obtain this, the machine manufacturers prefer today to use the system with profiled reed, in which the air and the thread are guided through a tunnel-shaped reed (Figure 4).
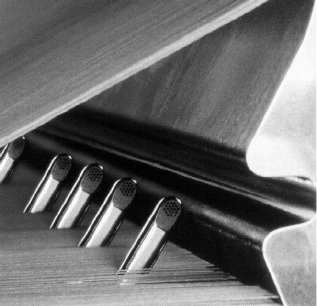
The weft is placed in the groove formed by the reed’s profiled dents, in which it remains until the reed stroke. In the air jet weaving machines, the impulse causing weft launch is provided by a main nozzle (Figure 5), but the jet of compressed air, being blown in a room of same kind, looses very quickly its own energy. Consequently, if the weft has to be transported along reasonable widths, the use of additional gears, that is of secondary or auxiliary (or relay) nozzles is necessary; these, besides pushing the weft forward, have also the task of keeping it inside the guide channel.
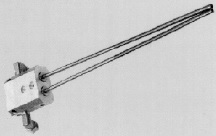
The auxiliary nozzles are stationed along the whole reed width and operate according to the relay principle; the nozzle holder blocks are connected groupwise to the distributors of compressed air by means of flexible pipes. The multi-hole relay nozzles (Figure 6) applied on modern air jet weaving machines accelerate the weft motion in the best way, at the same time reducing the stress on the yarn and helping towrds increasing machine yield and performance.
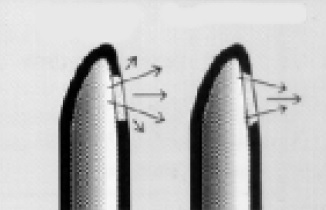
The manufacturers are increasingly installing on the weft delivery side of the shed a suction nozzle which has the function of maintaining stretched the weft pending the stroke of the slay and the consequent weft binding in the fabric. This ensures a perfect stretching of the weft inside the shed with any kind of yarn, even with the most critical yarns.
Among the various optional devices offered by some manufacturers, we point out in particular the auxiliary main nozzle; the combination of an auxiliary main nozzle with the main nozzle accelerates the weft motion but under low pressure, thus avoiding damaging the yarn.
A particular characteristic of the last models of weaving machines is the automation and the supervision of the machine with the aid of microprocessors. An automatic regulation system optimizes the air pressure in the machine, adjusting it to the variations of yarn characteristics. Thanks to this system, the pressure of the main nozzles and of the relay nozzles is self-adjusting depending on the yarn structure and on the resistance opposed by the yarn to its unwinding from the bobbin, which resistance varies with the changing of the balloon shape during the progressive emptying of the bobbin. This self-adjustment of the launch parameter takes place on basis of the weft arrival time, which is detected by the sensor of the weft stop motion. The weft arrival time needs to be constant in order to get always the same tension in the yarn; otherwise the yarn gives up its ideal way of operating, causing defects in the fabric and a higher number of machine stops. This way, besides avoiding machine stops and unnecessary adjustments, the consumption of compressed air is reduced to a minimum.
The warp let-off, the pick finding device or the levelling-off device of the heald frames to avoid defects on the fabric when restarting the loom, are anyway electronically controlled. Electronic and computer controlled systems are used also for weft color selection and to prevent formation of starting marks.
Automatic weft repair:
An important characteristic of these weaving machines is also the automatic repair of weft breakages, which on some loom models is standard equipment, while on other models is optional.
We stress the fact that air jet weaving machines are the only weaving machines which permit to repair reliably most weft defects. The automatic weft repair contributes to reduce the global down time of the machine (the automatic repair device is always ready on place, contrarily to what happens with the weaver) and improves the quality of the product. At the same time it permits to increase the number of machines allocated to the single weaver, and consequently to reduce labor costs.
The scheme of Figure 7 illustrates the sequence of the automatic weft repair proposed by an Italian manufacturer. The scheme shows how the faulty short weft is released from the fabric while a new additional weft is inserted (and the thread trimmer is temporarily disconnected); later the additional weft is cut and the relay nozzles in combination with the suction nozzle throw out the additional weft and the short weft.
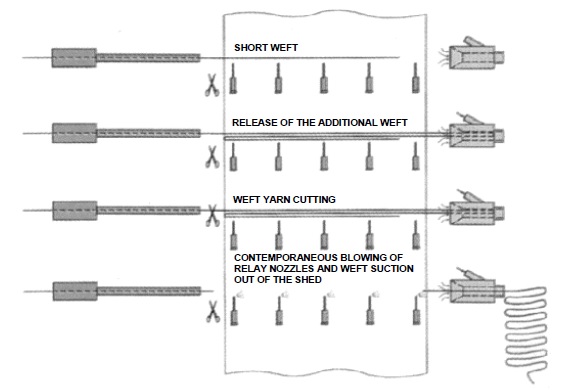
Conclusion:
To sum up, we can say that the production flexibility of the air jet weaving machines has been definitely improved thanks to the possibility of weaving an increasingly wide range of yarns (spun yarns, glass fiber yarns, continuous filament yarns) and of using Jacquard machines for the shed formation, as today by most machine models.
Air jet weaving machines are the easiest to be automated, as all main mechanical functions are controlled by a microprocessor. This last controls and stores efficiently the production data and provides a bi-directional communication between the machines and the main production computer. This way also the transfer of operational data, designs and adjustments can be performed on-line besides by memory card.
Finally we wish to stress the present trend of the manufacturers to develop their air jet weaving machines on the basis of their own rapier loom. This way the two machines have in common about 65% of the electronic elements, most of the accessories and make use of the same user interface.
The servicing and maintenance personnel works on machines which, apart from the different insertion systems, present a unitary structure. The possibility of exchanging the accessories and the quasi identity of the spare parts permits to save money and to reduce storage. By using both loom types (of same manufacturer), the weaver creates in the weaving room a natural integration to the advantage of versatility, productivity and quality.
References:
- Handbook of Weaving by Sabit Adanur
- Automation in Textile Machinery: Instrumentation and Control System Design Principles By L. Ashok Kumar, M Senthil kumar
- Reference Books of Weaving (ACIMIT) by Giovanni Castelli, Salvatore Maietta, Giuseppe Sigrisi, Ivo Matteo Slaviero
You may also like: Conversion of Chittaranjan Hand Loom into Power Loom