The process of joining fabric with the help of needle and thread is very ancient and till date it is the most widely used process for joining of fabrics all over the world. But there has study been going on for years whether fabrics can be joined without needle and thread; and a number of alternative ways have been evolved too. But in case of joining fabrics in alternative ways, there are a number of limitations, such as, the inconveniences of the speed of joining, the appearance of seam, the performance of seam etc. By researching with a long time some alternative methods are invented for joining fabrics. But the processes that are presently being used for alternative use of joining fabric though are not used for general sewing, but they are very much convenient and important for some special cases. In this article I will discuss different alternative methods of joining fabric.
Alternative Methods of Joining Fabric:
The alternative processes that are presently being used for joining of fabrics are as follows:
- Fusing
- Welding and adhesive
- Moulding
1. Fusing:
The three processes that are presently being used for alternative use of joining fabrics, among them fusing is the most used process. Specially, the job of joining of interlining with sewing has almost been entirely replaced by fusing. In this process, the side of the base fabric of the interlining, where exists the resins or polymer, is placed at the underside of the fabrics of the garments properly and joined by applying heat and pressure. The polymer layer or resin in the interlining is melted by heat and the melted polymers entesr into the fibers of the fabrics of garments and the fabrics of interlining by pressure and the melted polymers become hard, when it is cooled and the two fabrics that means, the fabric of the garment and the fabric of the interlining are bonded perfectly and rigidly.
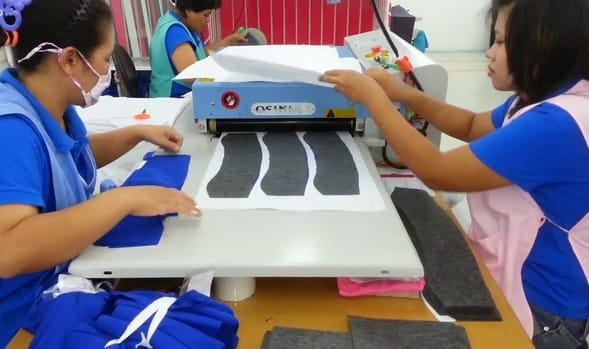
Only the interlining can be jointed in fusing process but this process cannot be used for general sewing. Interlining cannot be joined with all kinds of fabrics or garments in the above mentioned process, for which it is not being possible to totally discard the process of joining of interlining by sewing.
2. Welding and Adhesives:
The join that is given between the fabric of the garments and the interlining, as per the previously discussed fusing process is not used for bearing any sizeable strength or weight. But the join or the sewing of the fabric, produced by using welding or adhesive are used for bearing strength or weight. In the join or the seam of the fabric produced in this process, has some disadvantages, such as, flexibility, stretch and recovery are very poor. Specially, if there happens any defects in seams, there is no opportunity to rectify it. Without this, there are some other disadvantages for which the use of this process is very limited. But the use of this process is very important and essential in the cases, where the process is used. Presently this process is being used in three cases as mentioned below:
- For using decorative motif in garments
- For sealing off the cutting edge of the fabric cut for making of the garments.
- For temporarily joining of some parts of a garment which are permanently joined later on by top stitching.
a) Welding:
In case of garments making also, joining of fabrics or sewing is done in a very limited quantity in welding process. In this process, the fabrics where seam produced by welding, should have at least 65% of thermoplastic fiber. Taking two or more layers of fabrics together, heat and pressure are applied along the wanted seam line. As a result of applying the required amount of heat, the thermoplastic present in fabrics melts, and joined. In this process, heat is not applied from any external physical source, instead, heat is generated in the fabric by ultrasonic process.
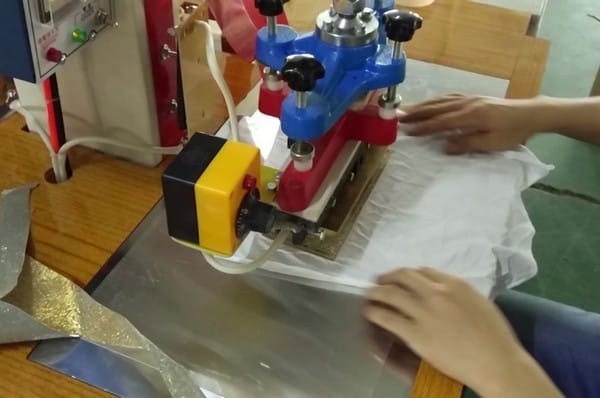
If two materials are rubbed strong with one another, then heat will be generated in the place where the rubbing will take place. If multiple layers of fabrics with thermoplastic fiber are kept together at the place where rubbing will take place, then heat will be generated in that place due to the cause of rubbing and if the heat is generated in sufficient amount, then thermoplastic fibers in fabrics will melt and the melted polymers are joined by applying required amount of pressure. A transducer is used in welding machine for converting the electrical power to mechanical functions or vibrations. Heat is generated with the help of mechanical vibrations produced by transducer. If the mechanical vibration is below 18,000 cycles per second, then sound will be audible by ear. So generally the vibration is kept at 20,000 cycles per second.
For joining of fabric in welding process, the mechanical vibration produced by transducer is send to a horn. Heat is generated at the place between the vibrated horn in high speed and the fixed anvil. Both heat and pressure are generated by horn. Horn may be in rectangular or in round shape. If rectangular, its measurement may be up to 25 cm x 4 cm, and for round, its diameter may be up to 9 cm. the shape of the horns may be in different forms based on the various types of welding.
The amount of heat generation depends on amplitude of vibration, frequency, pressure and the time of vibration. The amount of amplitude of vibration is determined on the types of fabrics and the types of welding, pressure is determined in the light of practical experience and generally it takes two seconds. The horn or the anvil always remains cold during welding in this process. After doing welding of a limited length, again welding is done in a limited length, that means, batch wise welding is done.
This process is used for neatening of the edges of fabrics for joining of motifs (thermoplastic fiber is must in the motif), for sealing off the cut ends of ribbons or tapes for making ties, for shaping of the parts of garments, for button holing, for shaping and sealing off the waist band ends etc. The seams produced in this process are to some extent rigid and rough, for which they may seem prickled in touch with the body, for which it should not be used in those places which come directly in touch with the body. The joining of fabrics in this process is given priority for making of water or rain repellant garments. Because, water cannot penetrate through this type of seam or joining.
Generally, this process is used in a limited case of making of garments of cheaper price, as there are many disadvantages in joining of fabrics in this process. Those fabrics, where the percentage of presence of thermoplastic fibers is less than 65, can also be joined, but then polythene film is to be used between the two layers of fabrics.
b) Adhesives:
Adhesive is generally meant to any sticky material by which something is joined. The adhesives that has been meant in case of making of garments, is to some extent different in qualities than the ordinary adhesive.
The adhesive used for fabric joining are mainly of two types:
- Thin layer of adhesive remains on silicon paper which just after transferring on fabrics, fabrics are joined
- One kind of material which melts in heat and helps in joining of fabrics.
The difference between the second type of adhesive and the welding is that, in case of welding, heat is generated within the fabrics, but in case of adhesive, heat is applied from physical source. Besides this, in welding, the materials in the fabric of the garments melt and joined, but in adhesives, the separate or different materials are used for joining of fabrics.
This process is used in a very limited amount for making of seams by joining of fabrics. For edge neatening of fabrics, an adhesive thread is used as a looper thread, and folding the neaten edge properly for making of hem, when heat and pressure are applied, the adhesive thread melts and attached with the fabric rigidly. As a result, hemming can be done without sewing. But the disadvantage is that, no change of hemming or of this kind of seam can be made. In separate process, attaching the stripes of adhesive along the edge of the pocket, patch pockets can be joined with the garment. But top stitching is required for strengthening of the seam.
3. Moulding:
In this process, though fabrics of multiple layers cannot be joined or are not joined, nevertheless, this process has been kept as an alternative process for joining of fabrics. Because, a specific shape is made by sewing, but in moulding process, a specific shape can be given without sewing, for this reason, it is considered as an alternative process of it.
In this process, the fabrics which can be given specific shape, should have at least 65% of thermoplastic fiber. Generally moulding is done in knitted fabrics, because it is suitable for stretching and shrinking. By stretching and shrinking of fabrics, the desired shape is given and the thermoplastic fiber is softened by applying heat, the temperature of the fabric is gradually brought to normally. As a result, the new shape of the fabric is fixed.
A few years back large quantities of ladies trousers were manufactured in moulding process. Making the knitted fabrics in tubular form in the volume of the leg of the trousers and wearing the tube in the shape of a leg forma, the volume would be set by moulding. Then by cutting the two tube shaped set in the similar way along the seat seam and then by sewing, the trousers were made. But presently the ladies trousers are being made in a very limited quantity, because in case of changing the fashions or styles and in case of increasing the beauty, this process has some limitations.
The moulding process is being used most in making the brassieres for the ladies. This process is used for making the cups of the brassieres. Then by joining the two cups by sewing, brassieres are made. The brassieres made in this process are beautiful to look at and comfortable to wearing, for which a sizable part in making brassieres are made in this process.
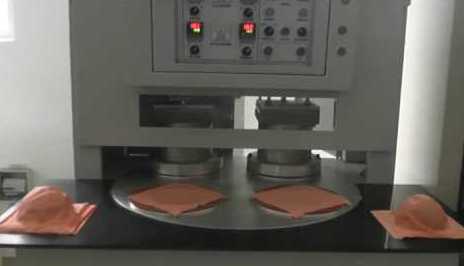