What is Textile Reinforced Concrete (TRC)?
Textile reinforced concrete (TRC) is a combination of fine-grained concrete and multi-axial textile fabrics, that has been fundamentally researched over the past decade. It is a cementitious‐based material where reinforcement consists of high‐strength noncorrosive textile fabrics. TRC is light, stable and also sustainable. This can make an important contribution to sustainable construction. TRC makes slim components that mean less building material required. Slim TRC components with enormous load-bearing capacity, low weight and high durability even under extreme environmental conditions. Thus, conserves natural resources and low emissions in the production of building materials.
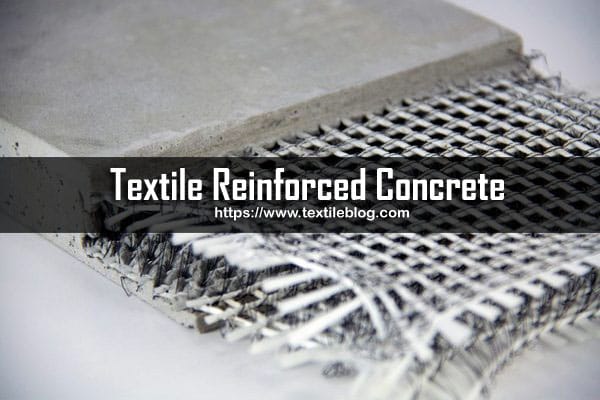
Characteristic features of TRC:
The characteristic features of textile reinforced concrete, are its thin structure and malleable nature, as well as its ability to retain a high tensile strength. Another important aspect of TRC is the permeability in the textile. Special attention should be paid to its structure, such that the textile is open enough for the concrete to flow through while remaining stable enough to hold its own shape, since the placement of the reinforcement, is vital to the final strength of the piece. The TRC material must also have a high tensile strength, a high elongation before breaking, and a higher Young’s Modulus than the concrete surrounding it.
Components of TRC:
To manufacture the TRC, depending on the process. Fiber strands (roving’s) are first produced from up to 10,000 continuous filaments with a diameter of a few micrometres. The textile fabrics with a grid in the desired mesh size created on knitting machines.
TRC is described as a strain-hardening composite. Strain-hardening composites use short fiber reinforcements. There are many different types of yarns, textiles weaves, and shapes that can be used in TRC. The textile begins with a yarn that is made of a continuous strand of filaments.
Textile concrete or textile-reinforced concrete is an innovative composite material made of a fine concrete matrix and high-performance fiber materials made of carbon, alkali-resistant glass: AR glass or basalt are especially good materials for this process.
Application of Textile Reinforced Concrete:
Concrete is a building material with very high compressive strength. But the high bending tensile strength required for many tasks only gives it reinforcement. In classic reinforced concrete, this is steel reinforcement. With its alkaline environment, concrete provides protection against corrosion, without which steel reinforcement would rust. But this requires a large and dense concrete covering for the steel reinforcement.
Application of TRC are extensively increasing in modern days in combination with materials science and textile technology. Textile-reinforced concrete can be used to create full structures, like Bridges, Pillars and Road Guards are prepared by Kevlar or jute reinforced concretes to withstand vibrations, sudden jerks and torsion (mechanics).
The application of reinforced concrete construction in the modern world, stems from the extensive availability of its ingredients, reinforcing steel as well as concrete. Reinforced concrete fits into every form, is extremely versatile and is therefore widely used in the construction of buildings, bridges, etc. Due to the thin, cost effective, and lightweight nature of TRC, it can be easily used to create many different types of structural components.
Best Structure Made from Textile Reinforced Concrete:
1. RWTH Aachen University’s pavilion:
Large scale textile-reinforced concrete in Germany, at RWTH Aachen University, where a pavilion was constructed using a textile-reinforced concrete roof. The roof was engineered using four TRC pieces. Each piece was thin and double curved in the shape of a hyperbolic paraboloid.
2. Pedestrian and cycle path bridge:
In 2015, the world’s first bridge that is reinforced with carbon is the pedestrian and cycle path bridge in the Albstadt Ebingen.
3. Facades made of textile concrete:
The world’s largest sandwich facade made of textile concrete realized in 2015 at “East side VIII” in Mannheim.
4. Bosphorus Bridge in Istanbul:
In 2016, a curtain wall made of textile concrete protects and designs up to 320 m high pylons of the third Bosphorus Bridge in Istanbul.
5. Repair of Aachen Cathedral:
In 2016, UNESCO World Heritage Sites Aachen Cathedral, the repair carried out using a textile-reinforced concrete TRC mortar bandage.
Why should Textile Reinforced Concrete in Sustainable Construction?
Concrete is the second most used material in the world, after water. According to a report of World Business Council for Sustainable Development, global concrete production was estimated to be approximately 25 billion per year.
Raw concrete is increasing in popularity. But the increasing use of concrete, has a significant impact on the environment. The uses of steel reinforcement represent a significant proportion of this impact. The most significant environmental impact, especially due to CO2 emissions. The global production of cement is responsible for 7-9% of all CO2 emissions, which has a significant effect on global warming and climate change. Worldwide cement production increased more than 12 times in the past 50 years.
Textile reinforced concrete can contribute to a solution by providing two advantages: steel replacement and considerable concrete savings. This significantly reduces the consumption of concrete. That’s why, TRC in sustainable construction is very important.
Sustainability of Textile Reinforced Concrete:
The building construction industry is in need of the sustainable materials and solutions. A novel building material Like textile-reinforced concrete (TRC), could be used to meet this demand.
TRC is thinner than traditional steel-reinforced concrete. Steel reinforced construction is 100 to 300 mm thick, while TRC structure is generally 50 mm thick. It has much thinner due to an extra protective layer. Due to this thinner structure, less material is used, which helps to reduce the price of using concrete. As a result, the amount of concrete needed is also reduced.
TRC can also be used to extend the life of existing structures, it cuts down on the cost of materials and man power needed to tear down these existing structures, in order to create new ones. Instead of replacing old structures, they can now be repaired to add years of service to the lives of their construction.
Conclusions:
In future, the use of textile reinforced concrete will bring greater choice and flexibility in the design and manufacture of supporting components of structures. By replacing conventional steel reinforcement with innovative textile fiber in the design of the structure, additional architectural projects can be realized which were previously considered impossible. We should be aimed to compare the subtle TRC facade elements made of three different types of technical textile roving’s like: glass, carbon, and basalt, with ordinary facades reinforced by steel reinforcement.
In conclusion, after a detailed analysis of the whole TRC, textile reinforced concrete facades appear to be more environmentally friendly in comparison to the ordinary solution. So, it can be said that, TRC will be the construction material for future generations.
References:
- Textile Reinforced Concrete by Alva Peled, Barzin Mobasher, and Arnon Bentur
- https://en.wikipedia.org/wiki/Textile-reinforced_concrete
- Curbach, M.; Schladitz, F.; Müller, E.: Carbon concrete – from research to practice.
- Groz-Beckert KG: the textile-reinforced concrete bridge.
- https://framcos.org/FraMCoS-5/haeussler.textile.pdf
- http://www.jeccomposites.com/knowledge/international-composites-news/textile-reinforced-concrete-high-performance-carbon-fibre
- RWTH Aachen Competence Center Textile Concrete
Author of this Article:
Md Mahedi Hasan
B.Sc. in Textile Engineering
Textile Engineering College, Noakhali.
Email: mh18.bd@gmail.com
Admiring the hard work you put into your blog and in depth information you provide.
It’s great to come across a blog every once in a while that isn’t the same outdated rehashed information. Excellent read!
I’ve saved your site and I’m adding your RSS feeds to my Google account.
Here is my webpage :: xxx yandex