Perhaps the development of world civilization is going on along with the development of textiles. Textile fibers have been developed over many hundred years and most suitable fibers have been selected for the textile industries. Fibers have traditionally been used by human in all cultures of the world to meet their basic requirements i.e. clothing, home and especially technical purposes. Worldwide gradual development of textile industries meets the increasing demand of textile materials. The demand of natural fibers is constantly increasing due to their environmental friendly, hygienic, comfortable character, thermal insulation, breathability and softness in feelings. Some synthetic fibers are also important for safety and technical purpose.
Fiber is the first elementary raw material of textile manufacturing. It is either natural or manmade, staple or filaments. Natural fibers are those fibers that are directly produced at nature, usually at plants, animals or minerals.
Textile fibers:
Textile fiber is a class of materials, which are natural or manufactured, can take tensile, friction and bending forces not compression and spun into yarn by twisting together or also converting into fabric (non-woven) direct from fiber. If two fibers are twisted together is stronger than both individual without increasing its tenacity.
Fiber is the smallest visible a substance which is extremely thin in relation to its width. Any substance, natural or manufactured will be considered as a textile fiber, if it has posses the following parameters:
- High length to width ratio, at least 500 times longer than it’s lateral dimension i.e, L (Length)/d (Diameter of fiber) > 500 (called slenderness ratio)
- Flexibility/stiffness (can give any shape)
- Dye ability
- Good strength and elongation (elastic, i.e, not rigid)
Formation of textile fiber:
Most of fibers are constructed by long chain of polymer molecules which lay alongside each other and are cemented together by different bonds. A polymer is a large molecule (macromolecule) composed of hundred to thousand repeating structural units. The molecular weight of a polymer is proportional to degree of polymerization and structure of monomer (smallest structural unit).
Cotton, flax, silk and wool fiber is formed in nature by natural way of polymerization. Generally natural polymer has long chain, which means it constructed with many repeating units. The structure of natural polymer depends on cultivation and environment of growing up period.
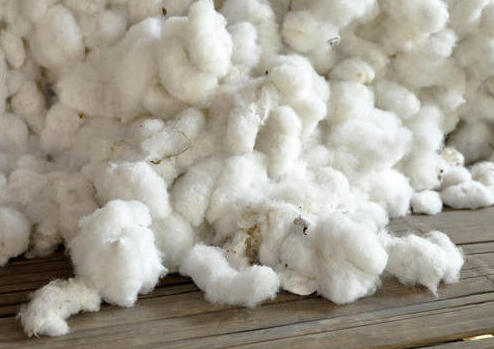
Synthetic fibers are formed by polymerization process of one or more than one monomer. Thousands of monomers are coupled together by poly-addition (e.g. polypropylene) or poly-condensation (e.g. polyester) process. The structure of synthetic polymers depends on manufacturing processes and the character and origin of monomer.
Regenerated fibers are formed from natural polymer through a suitable man-made process. The structure of regenerated fiber depends on manufacturing processes and the character and origin of natural polymer. Cellulosic man-made fibers (viscose, cuprammonium, acetate and lyocell) are made from natural cellulosic polymers, which are collected from plants. The macromolecule which has been synthesized by nature may be used as such or may be chemically modified for regenerated fiber production. To enable cellulose to be spun, it has to be dissolved by appropriate solvent.
The principles of man-made fiber production are as following steps:
- Conversion of the fiber-forming substance into a fluid by solution or melting.
- Extrusion of the fluid through spinnerets.
- Solidification of the extruded filaments.
Standard construction model of a textile fiber:
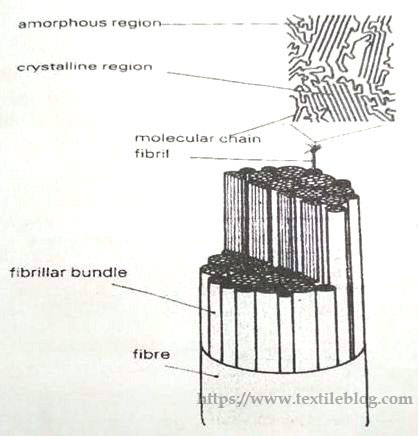
Fig-2 shows a standard construction model of a textile fiber. It is clear that a fiber is composed of many fibrillar bundles and each fibril is constructed by many polymer chains. These polymer chains are arranged in different orders. Some are oriented and parallel arranged and some are disoriented, which are known as crystalline and amorphous region of fiber respectively.
Characteristics of fiber forming polymers:
Fiber forming polymers should have the following properties:
- Optimum mol mass and its distribution.
- Possible linear polymer chain and avoiding branching of them.
- Interactions of inner molecular chain.
- Shear, tensile/axial, compression forces, elongation/deformation.
- Functional groups (responsible for affinity and absorption).
- Visco-elastic nature.
Morphology of textile fibers:
The long polymer chain (macromolecule) of a fiber is constructed by many small repeated units. The average number of repeating unit of a polymer chain is called degree of polymerization (DP). A fibril is composed of 50-20000 repeating units, which is a long-chain of macromolecules and the bulk of fibril bundle contains amorphous and crystalline regions, depending on the arrangement of the polymer chain molecules. Finally the fiber strand is constructed with many fibrillar bundles. Physical properties i.e. fiber strength, flexibility, moisture and dye behavior etc. depends on this inner structure of the fiber. All fibers, whether vegetable, animal or man-made are mainly constructed by linear polymers which lie alongside each other and are stayed together by several bonds.
Crystalline and amorphous:
In crystalline region, where polymer chains are arranged in regular order and the amorphous region is a region where polymer chain is stayed in disorder form, which is also a weak part of the fiber.
Sources and origin of textile fibers:
Solar energy is the basis of life. The plants are produced by the combination of soil, CO2, H2O and solar energy. Plants, petroleum and minerals are basic sources of fiber. Cellulose is the basic structural element of natural fibers which are extracted from plants. It is formed through photosynthesis of carbohydrates by green plants from carbon dioxide using solar energy and water. This food is taken by animal and transformed into fiber-forming proteins within animal body.
Cellulosic manmade fibers are regenerated from the polymer of plants (wood, bamboo etc). The cellulosic substances are dissolved and then forced through spinning jets, later they solidify by chemical reaction. Synthetic manufactured fibers are derived from petroleum products.
Classification of textile fibers:
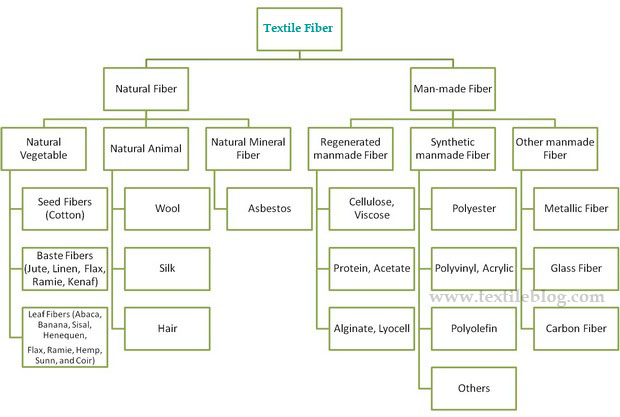
Application of textile fibers:
Generally the following textile fibers are used in following purposes:
- Apparel textile: Cotton, viscose, flax, wool, silk, polyester, polyamide and acrylic fibers are used in making apparel.
- Home textile: Cotton, jute, polyester, polyamide and acrylic fiber are used in home textile.
- Industrial or Technical textile: Cotton, jute, polyester, polyamide, glass, carbon, ceramic fiber are widely used in technical or industrial textiles.
Difference between textile fibers and other materials:
Textile fiber | Other materials |
1. They are formed by polymerization processes. (natural or synthetic) | 1. They are not so formed. |
2. There are composed of millions of molecular chains. | 2. They are not so composed. |
3. They have large molecular weight. | 3. They have relatively small molecular weight. |
4. The molecules are formed (join) by the attractive forces, called H-bond, Vander wall forces etc. | 4. The molecules are joined by electrovalent bond, covalent bond and co-ordinate covalent bond. |
5. Molecular structure can be changed i.e. jute, cotton etc. | 5. Molecular structure cannot be changed i.e. soda, salt, etc. |
6. Insoluble in water. | 6. Soluble/Insoluble in water. |
Primary key properties of textile fibers:
A fiber has to the following physical and chemical properties to meet some specific requirements. There are several primary and key properties necessary for a polymeric material to make an adequate fiber and these are:
- Fiber length
- Length to width ratio
- Tensile properties (strength/elongation)
- Elasticity (modulus of elasticity)
- Flexibility (bending and knitter)
- Elastic recovery from strain
- Cohesiveness
- Chemical composition, structure and molecular arrangement
- Wet-ability or moisture absorption
- Dye-ability
- Density
- Comfort to human skin
Secondary and auxiliary properties of fiber:
Certainly other fiber properties increase process efficiency, value and desirability in its intended end-use but are not necessary properties, which are also essential for a fiber. Such secondary properties include:
- Resiliency
- Toughness
- Work of rupture
- Uniformity
- Crimp
- Fineness (MIC)
- Color/Luster (reflecting index)
- Maturity ratio/Index
- Fiber friction
- Low glass transition temperature (0C)
- High Melting/Burning/Decomposition Temperature (0C), i.e. Low flammability and heat resistance are expected
- Moisture content/region%
- Capillarity
- Surface tensions and interface
- Drapes
- High abrasion resistance
- Chemical resistance
- Solubility (normally fiber in insoluble)
- Electrostatic properties
Some general properties of textile fibers:
Staple and filament fibers:
On the basis of length, fibers have two categories: staple and filament. Filament further classified as mono filaments and multi-filaments.
Any fiber with a practically limited or finite length is called staple fiber. These are small length fiber like cotton, wool, jute etc. Most natural fibers are staple fibers. Natural fibers are those fibers that are directly collected from nature usually from plants or animals. The common natural fibers are cotton, wool, silk, jute and flax. Fibers from plants and animals are constructed directly in nature have very large molecule of polymers.
Filament is a fiber that manufactured is continuous to near continuous lengths for use. All fibers having a practically unlimited or infinite and endless-fiber length are called filaments. Filament fibers may be produced as mono (single) or multi (10-100) filament type. Most manufactured fibers are produced at filaments form. The length of filament may range from a few hundred meters to several kilometers. Filaments can be converted into staple fiber by cutting of specified length. Staple polyester and viscose are available in market for blending with staple cotton fiber.
Microfiber and nano fiber:
Microfiber refers to a (normally synthetic) fiber as fine as less than one denier per filament. The most common types of microfiber are made from polyesters, polyamides and also conjugation of polyester and polyamide. Nanofiber refers to a synthetic/inorganic fiber which is fine nano dimension.
Length:
Length is the most important factor for assessing the value of a fiber. Most natural fiber is of limited length, commonly a few millimeters to several centimeters. Silk is the exception, being formed as filament, which may be 500-2000 meter in length.
Strength and elongation:
This is the breaking strength of any material which is commonly expressed as force per unit cross-sectional area (N/mm2). When a single fiber is being considered, the strength of the fiber is commonly described as tenacity (gm/tex), which is a measure of specific stress or tenacity at break, i.e. breaking load/tex.
During force F is applied on the fiber length (L) then the length variation ∆L is increased from force the rated stress becomes σ with the cross-section area of a fiber A.
Elastic limit:
This is the limit up to which the fiber is elongated during loading and recovers its elongation after relaxation of load. Simply fiber returns its original length without any stretching. The deformation up to elastic limit is called elastic deformation.
Permanent elongation:
The length which extended during loading does not recover during relaxation. It is also called plastic deformation.
Breaking elongation:
This is the maximum extension at which the fiber, yarn or fabric breaks.
Rigidity or stiffness:
Rigidity or stiffness of a material is measured by its Young modulus and measures how much a material deflects under transverse directional stress.
Difference between natural and man-made fibers:
Parameters | Natural fibers | Man-made fibers |
Definition | Natural fibers are those fibers that are collected directly from nature. | Man-made fibers are those that are made artificially by human. |
Sources | Solar energy, CO2, H2O, seeds soil and minerals. | Plants, petroleum and minerals. |
Types | Vegetable, animal or mineral in origin. | Regenerated, synthetic, high-performance. |
Sizes | Natural fibers are staple fibers expect silk. | Manufactured fibers are filaments and made as staple fibers. |
Uniformity | Do not have a uniform size. | Have a uniform size. |
Texture | Have more texture. | Have less or no texture. |
Comfort | Comfortable | Non-comfortable |
Absorption | High moisture absorption. (hydrophilic) | Low moisture absorption. (hydrophobic) |
Impact on nature | Biodegradable and environmental friendly. | Not biodegradable and makes environmental pollutions. |
Economy | Low production cost as low investment. | High initial investment cost. |
Strength | Moderate tensile and good bending. | Low (regenerated), high (carb on), tensile low bending. |
Durability | Lower durability. | Higher durability. |
Example | Cotton, jute, flax, wool and silk. | Viscose, cupro, lyocell, polyester, polyamide, elastan and acrylic. |
Modern instruments for textile fibers testing:
There are many science, technology and instrument are used to determine and analysis the property of fibers. The following instruments are used for measurement the different property of textile fiber.
S.N. | Name of the instrument | Measured property |
1 | HVI (High Volume Instrument) | Fiber length, strength, fineness, color and trash grade. |
2 | AFIS (Advanced Fiber Information System) | Fiber length, trash and neps. |
3 | X-Ray Diffraction System | Amorphous and crystal part of a fiber. |
4 | Vibromate | Individual strength of fiber. |
5 | UV-Spectroscope | Chemical composition and structures. |
6 | IR or FTIR-Spectroscope | Chemical composition and structures with functional groups. |
7 | GPC (Gel-Permeation-Chromatography) | Mass-molecular distribution. |
8 | DSC (Differential Scanning Calorimeter) | Thermal properties of fiber. |
9 | NMR Spectroscopy | Structure of fiber. |
10 | TGA (Thermo-Gravimetric Analysis) | Thermal properties of fiber. |
11 | SEM and AFM | Surface topography of a fiber. |
12 | Zeta potential meter | Charge on fiber surface. |
References:
- Natural Fibers by Dr. Abu Bakr Siddique & Dr. Hosne Ara Begum
- Introduction to Textile Fibres by H. V. Sreenivasa Murthy
- Handbook of natural fibres, Volume 1: Types, properties and factors affecting breeding and cultivation Edited by Ryszard M. Kozłowski
- Handbook of natural fibres, Volume 2: Processing and Applications Edited by Ryszard M. Kozłowski