What is Marker?
Generally marker is meant to a piece of paper, on which all sizes patterns of a garment are drawn so that the required number of garments can be made using the minimum quantity of fabrics (minimum wastage of fabrics). Marker width is taken as the minimum fabric width and the length of the marker depends on how many sizes of patterns are used for making the pattern. Some other factors are involved with marker length:
- How many garments will be made with one lay of fabric.
- The length of the cutting table.
- Production planning, etc.
A marker and fabric lay/spread is shown in figure.
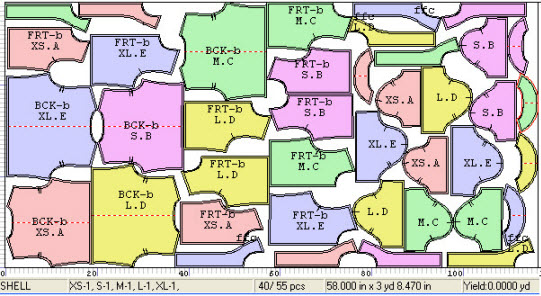
Marker Efficiency:
The success of the jobs a marker man is determined by the marker efficiency. The expression in percentage of the occupied area by the patterns used in a marker in relation to the total area of a marker is called the marker efficiency. Marker efficiency can be measured by the following formula:
…………………………………The area of the patterns used in the marker
Marker Efficiency = —————————————————————– x 100
………………………………………………….The area of the marker
The greater the marker efficiency the lower is the fabric wastage. This means that for making a specific number of garments, comparatively less fabric will be required. About 50% of the cost of a garment is spent for fabric purpose. The meaning of 1% increase of marker efficiency is the addition of the cost of that fabric (less used due to 1% marker efficiency) with the profit. For these reasons the increase of marker efficiency is very much important. So, making marker is an important task in apparel manufacturing process.
The factors which are involved with the marker efficiency are as follows:
a) Marker maker:
Marker efficiency mainly depends on the skill, effort, honesty, sincerity, experience and technical knowledge of the marker man. For making a marker, the greater the number of times the marker will be made, the higher the possibility of better marker efficiency.
b) Garment size:
During marker making, the greater the number of sizes of garments are included, the higher the possibility of better marker efficiency. But if the sizes are too many then the reverse situation may happen.
c) Marker length:
The marker length is involved with various factors. Greater the length of the marker, greater the chances of higher marker efficiency and the production of cutting room will also be increased. But if the marker length is too long, then reversed result may happen.
d) Pattern engineering:
Marker efficiency can be increased by changing pattern designs of some of the parts of a garment or by dividing the pattern or by fragmenting any small part of a pattern.
e) Fabric characteristics:
There are some fabrics which are seen as same from any side, this is called symmetrical fabric. In case of these fabrics, the greater marker efficiency can be achieved during making of marker. But the fabrics which are not symmetrical, that means which are asymmetrical fabric, there is a chance of getting less marker efficiency. Especially for matching of stripes or checks in fabrics, there is tendency of getting less marker efficiency.
f) Marker making method:
Mainly there are two methods for marker making, i.e. 1. Manual marker and 2. Computer aided marker. If the computer aided marker is done, the efficiency becomes greater than manually done marker, but it takes much time. If the marker is made by experienced marker man, then in less time the greater efficiency of marker can be obtained.
g) Marker width:
Generally the marker width depends on the fabric width. It has been found in study that greater the width of a marker, easier for the marker man to plan the marker. As a result there remain chances of getting greater efficiency of a marker. This logic may not be right in case of tubular fabrics.
h) Garment type:
The garments where big sizes patterns are greater than small sizes patterns such as slacks of men’s and ladies, overcoat, etc. less marker efficiency is obtained. Because, after placing the big sizes patterns, the small patterns are not available for placing at those gaps, so fabric wastages are big. But in the garments where the number of small size patterns are big, comparatively the higher efficiency is obtained during making marker of these garments.
Constraints of Marker Making:
For making an efficient marker such a system is required so that the marker man can see the full length and width of the marker easily. The marker man usually places the bigger patterns first and then tries to place the smaller patterns in the gaps of the bigger patterns. This way the fabric wastage can be minimized, this means that the marker efficiency can be increased. Then the marker man tries to place the patterns by turning or moving them so that the length of the marker can be reduced, this means efficiency can be increased.
The factors which prevent the marker man to make the efficient marker are listed and reviewed below:
a) Grain line:
On each pattern the grain line is marked. Grain line indicates the warp side of fabric. During marker making, the grain line of pattern must be placed in parallel with the warp side of woven fabric and the wales of knitted fabrics. Based on garments designs/styles, sometimes patterns are placed in 45 degree angles. The drape and hang of garments depend on the matching of grain line of fabric and the grain line of pattern. For increasing marker efficiency the fabric grain line can be placed at 2 degree angle with the pattern grain line. But need to keep observation so that there happens no appreciable harm in the designs/styles of garments. To keep eye on grain line matching and to abide by that rule, acts as a constrain to the marker maker.
b) Fabric characteristics:
Some fabrics are seen as same if they are rotated at 180 degree angle. This is called the symmetrical fabric. In case of symmetrical fabric, there is no problem during marker making. But some fabrics are seen different when they are rotated at 180 degree angle. These are called the asymmetrical fabric, such as: pile fabric, some special type of printed fabrics etc. During marker making for asymmetrical fabric, special attention should be given otherwise the garments look may be defective. For this reason, in case of marker making for asymmetrical fabric, the pattern cannot be moved randomly as per wish, which is considered as an constrain during fabric spreading for asymmetrical fabrics.
c) Garment design characteristics:
In those garments where special designs are must such as mirror image, this means that the left and right side along the center front line will be looked as same. During fabric spreading and marking special attentions is to be given so that after making the garments the desired designs are obtained in each garment.
d) Cutting quality:
In most of the cases the patterns are cut separate from the fabric lay with the help of knife blade. The normal width of knife blade in the middle of the fabric spread creates problem in rotating the blade at 90 degree angle. For this reason, precautionary measures should be taken during marker making so that for moving the knife for cutting the patterns, no problems arise, otherwise chances of defective pattern cutting will be seen.
Just after making the marker, need to count that how many total patterns are there. For example, need to make pants for six sizes, in each size there are sixteen patterns, then there will be 6×16 = 96 pieces of patterns. For any reason, if a single or a number of patterns are found short during sewing after cutting of the fabric that will bound to accept wastage or much time and money. For this reason, just after marker making, the total number of patterns in the marker must be counted. Code numbers need to be used in each pattern of a marker so that the pattern can be separated easily after the cutting of fabric and pattern of one size is not mixed with the pattern of the other size. Otherwise for adding one error, two additional errors will be evolved causing wastage of much time and money.
e) Production planning:
When production order from any garments order is given, generally the number of garments in that order is given in dozen and in addition to that the number of garments in dozen for each size, each color etc. are also mentioned. Specially the sizes of the garments are given in ratio. An example of an order of 1500 dozen of ladies dress is given where there will be 600 dozen white, 600 dozen blue and 300 dozen cream color garments, the ratio of the sizes 15, 16, 17 and 18 will be 2:4:4:2.
For the above mentioned order, production planning can be done in different ways and markers can also be done in different ways as per the planning. Firstly, taking the patterns of all the sizes as per ratio, a marker can be made. This means in this case 2 sets for the size 15, 4 sets for 16, 4 sets for 17 and 2 sets for the size 18 which means taking total 12 sets of patterns, a marker can be made. In this case greater marker efficiency may be achieved but it takes much time to make the marker. On the other hand, due to the larger length of marker, there is a possibility of not accommodating the fabric spread or lay in the cutting table. In addition to that, more fabric rolls are required for making fabric lay of certain height. As ther may happen color shade variations among the fabric rolls, the shade variations in garments increase. Without this, among the fabric spread, the number of fabric ply in each color becomes less for each color that means the number of bundles increase. For a larger number of bundles, greater handling costs happen.
Secondly, two markers can be made for this order. For the first marker, the marker can be done taking 2 sets for the size 15, 2 sets for 16 and 2 sets for size 17 that means the marker can be done with six sets of patterns. In the second marker, the marker can be done taking 2 sets for the size 16, 2 sets for 17 and 2 sets for size 18 that means the marker can be done with six sets of patterns. This way, with multiple use of the two markers, the required total fabric for the order can e cut. In the second system marker, there are both advantages and disadvantages. Such as for each marker the length will be almost half of the previous marker. As a result, it is comparatively helpful to do smaller length marker and prompt production. The smaller length of marker is suitable for small cutting table. The possibility of being shade variations of garments is also less. But in this case there is a chance of attaining less marker efficiency.
Therefore, from the above mentioned discussion, it is easily understandable that marker making and its efficiency are related with the production planning.
Methods of Marker Making:
After making patterns of any garments (all the required sizes) marker is made. At the very beginning of marker making, the marker width is determined. The minimum width of the fabric with which garments will be made is taken as the width of the marker. Generally marker is made on white paper or newsprint paper. First the big patterns are placed and then the small patterns are placed in the gaps of the big patterns. As a result, the marker efficiency is increased. The marker making is a very skilled and technical job. Markers are made mainly in two ways.
- Manual marker making (with full size patterns and with small size patterns)
- Computer aided marker making
1. Manual marker making:
in this method, markers are made with physical and mental labor. Manual marker can be done with full sizes patterns as well as with the small sizes patterns. Both methods are discussed below:
a) With full sizes patterns:
in this method, all the patterns are in full sizes as per the normal measurements. Comparatively hard patterns are placed on the papers or on fabrics. Then all the patterns are tried to place by moving in various direction in order to get the better marker efficiency. Marker making in this method is usually suitable for making the marker of small length. Because the marker man can easily see and control all the patterns within a small length. In cases where markers are made with patterns of many sizes are generally long in length, as a result for making long marker, this method is not suitable. Because it is very difficult for the marker man to place the patterns efficiently in full length. The top of the table on which the marker paper or fabrics are placed and marker is made, may be fixed or tilting. The tilting table top may be placed in various angles so that it becomes suitable for marker making. Moreover under the table top there is arrangement for making vacuum system, as a result, the patterns can be placed fixed in their own positions.
b) With small sizes patterns:
In this method also markers are made with physical labor. In the beginning, the patterns are made smaller in 1/5th scale or in 1/25th scale with the help of Pantograph. Then in 1/5th scale the marker is made in smaller table. The systematic explanation of marker making in this method is given below:
- With the help of a pantograph the full length patterns are made smaller in the 1/5 scale. The smaller patterns made with pantograph are generally made with plastic sheet or coarse and hard board paper.
- With the help of smaller size patterns, marker making planning is made. The table on which marker planning with smaller patterns are made, that table is generally 50cm wide, 2 meter long and it is marked with 1/5 scale on both sides. As a result, it becomes comparatively easier to place, move or plan the small patterns in the small area.
- After making the marker, the photograph of it is taken with a camera. If time is available, again marker is made and its photograph is taken.
- How much area of a marker has been covered by the patterns is determined with the help if a planimeter. Then the marker efficiency is determined with the marker area and patterns area.
- The marker photograph and the concise patterns are kept well preserved in a cabinet.
Seeing the photograph of the efficient marker made with reduced sizes patterns, placing the full size patterns on paper or fabrics, full size marker can be made. Sometimes reduced sizes patterns are faulty due to the faults in pantograph. When a full size marker is made seeing the photograph marker, sometimes the efficiency of the full size marker is found comparatively more efficient. For making garments on a bulk scale, this method is suitable but for making garments in smaller quantity, this is not suitable because of using much time and cost.
2. Computer aided marker making:
For making computer aided marker, first of all, the production patterns need to be stored in the computer memory. For entering the production pattern into the computer, generally digitizing or scanning methods are used. For digitizing or scanning, full size production patterns are used and in the computer memory also the full size patterns are stored, but reduced size patterns are seen in the computer screen. After entering all the production patterns, required for a garment in the computer memory, using the grade rule previously stored in the computer, the required patterns for all sizes are obtained. The computer aided marker man generally uses computer screen, key-board and light pencil. Then the marker man gives some instructions to the computer, such as: the marker width, pattern sizes to be used, check matching and all the obstacles to marker making, which the computer will always maintain during marker making. In this process the computer itself can make the marker, also the marker man can make the marker with the help of the computer.
If a computer does the marker itself, then it is called the automatic marker making. In case of automatic marker making, if the computer is provided with some preplanned required instructions, then based on it, the computer make the marker itself. In this process the most efficient marker is obtained, but computer takes much more time to make the marker, because computer makes the marker using permutation and combination methods.
When the marker man makes the marker with the help of a computer, it is called the interactive making apparel marker. In this method all the pieces of patterns are seen in smaller dimension on the top part of the computer screen. In the middle of the screen two horizontal parallel lines are seen which indicates the width of the marker. A vertical line remains at the left side of the horizontal parallel lines which indicated the beginning or starting of the marker and initially the right side remains open. There remains some data below the horizontal parallel lines, for example: identification of the marker, marker length, marker efficiency (which changes regularly) etc.
For making marker in interactive method, a data pen is used and a tablet is used for removing the pattern. Generally tablets represent the display screen. There is a pointer in the data pen which has pressure sensitive point. Using this pen, patterns can be placed in any place of the screen. The pattern to be removed will be marked with the help of the cursor of the screen. For removing the marked pattern, the pen is lightly pressed on the tablet and then the pen is moved on the tablet, as a result the pattern comes on the screen and it is placed in the suitable place in the marker by moving the pen. Again if the pen is lightly pressed it leaves the pattern, this means the pattern takes its prescribed place in the marker. This way, all the patterns are arranged in the marker. Within a very short time in this way an efficient marker creating is possible. If the making apparel marker is complete, below the marker in the screen, the data of marker efficiency, marker length, marker width, pattern count, etc. are obtained instantly. If the marker making is complete, it is saved in the computer memory and if the print out facility is available, the print out is taken.
The standard and efficiency of the marker made in computer is far better than the manually made marker. In computer the marker can be obtained fastest and the number copies of the marker can be obtained as much as per wish. In a word, computer aided marker has many positive sides. But in this method of computer, the initial investment is high. Computer aided marker can save at least 2% of fabrics.
Methods of Drawing and Duplicating a Marker:
I have published an article on “Marker Drawing and Duplicating Techniques”. Before going to next portion you should read this article first.
Fabric Wastage Outside Marker:
The maximum use of fabric mainly depends on marker efficiency. Nevertheless, some more fabrics are wasted which sometimes goes beyond the control of marker planning. For the benefit of controlling such wastage, a discussion is made here on the reasons which cause this type of fabric wastage.
a) Ends of ply losses:
Due to the fabric extensibility and the limitations of the fabric spreading machines, some allowance should be kept at the end of each lay during fabric spreading. The amount of this allowance is generally kept 2 cm in each side, as a result, for each lay of fabric total 4 cm of fabric is kept extended, which is included in the fabric wastage list. Based on the stability of the dimension of the fabric, the quantity of such type of wastage may be more or less than the mentioned. Therefore, this type of wastage can be minimized if it is observed and controlled with due importance that what amount of allowance should be kept for what fabric.
Moreover, if the marker length is big, such type of wastage decreases and if the marker length is small such type of wastage increases.
b) Loss of fabric ends:
Fabrics used in garments industry generally comes in rolls. In each fabric roll there is fabric length limitation. Fabric lay is made based on the marker length. In most of the times it is seen that fabric lengths varies in quantity more or less than the multiple of lay length. As a result, during fabric laying, at the end of fabric of almost all rolls, spice or remnants, the fabric wastage increase which is beyond the control of marker planning. This type of wastage cannot be stopped, but can be reduced, such as, greater the length of fabric roll, lower will be the rate of fabric wastage. With proper identification and control of the place of splice in the marker, by full utilizing of remnant etc.
c) Selvedge losses:
In each fabric there are two selvedges along the width of the fabric. Generally, in most of the cases, the selvedge of fabric is left out. This left out quantity is generally taken as 3% along the fabric width. But if the fabric is highly stable in dimension, then it can be taken as 2% as left out. How much quantity of fabric width could be used that depends on the quantity of the fabric selvedge, uniformity of the fabric width and the alignment of selvedge during the time of fabric spreading. Width way fabric wastage is out of marker planning and it is not possible to stop this wastage but it can be reduced. Greater the width of the fabric lower will be the rate of such type of wastage.
d) Purchase loss:
Generally fabrics are bought in length. Normally the fabric length is marked on the fabric roll by the fabric manufacturer and the supplier. Sometimes it is seen that the lower length of fabrics than the marked length on the roll are found in some rolls of fabrics. After buying the fabrics if this shortage of fabrics in rolls are not detected then in most of the cases the buyer seems to bear the shortage. For this reason, fabrics should be examined before the fabric buying and receiving of the supply.
References:
- Garments & Technology by Prof. M. A. Kashem
- Garment Manufacturing Technology by Md. Shafiul Azam, Md. Abu Saleh & Khondokar Abu Nafiz
- Apparel Manufacturing Technology by T. Karthik, P. Ganesan, D. Gopalakrishnan
- Garment Manufacturing Technology Edited by Rajkishore Nayak and Rajiv Padhye