Effect of Pretreatment Process on Dyeing of Viscose Fabric with Reactive Dyestuff
Mohammod Habibur Rahman & Ataur Rahman
Department of Textile Engineering
Dhaka University of Engineering & Technology (DUET)
Gazipur-1700, Bangladesh
The pretreatment process significantly affects the dyeing performance of viscose fabric with reactive dyes. Proper pretreatment enhances dye uptake, color fastness, and overall fabric quality.
Objects:
- To increase quality of dyed fabric.
- Cost minimization
- Best process selection
- Observation of different pretreatment process
- Compare various pretreatment process
Operational activities:
1. Scouring & bleaching:
- Different amount of wetting agent use.
- Different amount of detergent use.
- Different types of detergent use.
- Different amount of caustic soda (NaOH) and soda ash (Na2CO3) apply.
- Different amount of Hydrogen peroxide (H2O2) use.
- Various liquor ratio use.
Note: When one parameter change then others parameter will remain constant.
2. Dyeing:
Our main object is to observation of different pretreatment process effect for same dyeing recipe. Which process gives us better result.
3. Finishing:
Methodology:
The methodology is as follows-
Planning & budgeting
↓
Collection of viscose fabric
↓
Collection of chemicals & dyes
↓
Various pretreatment & dyeing procedure
↓
Observation of results
↓
Compare of results
↓
Select best alternative
Chemicals and Dyes:
- 1.Wetting agent
- Detergent
- Sequestering agent
- Caustic soda (NaOH)
- Soda ash (Na2CO3)
- Stabilizer
- Anti creasing agent
- Antifoaming agent
- Salt
- Hydrogen per oxide (H2O2)
- Acetic acid
- Leveling agent
- Softener
- Enzyme
- Peroxide killer
- Lubricant
- Dyes
- Bicromate or fitcary
- Copper sulphate
Modal fabric dyeing (Deep Shade):
Fabric construction: 40/s Modal cotton S/J & 20D Lycra, GSM =150, 3424, SL = 2.9 mm Dia = 75″ (open)
Chemicals/ mlt | Recipe | Process | Dozing /inject | Running & pH |
Materials | Batch | Heat setting | 190°c to 200°c through stentering | |
Material | Batch | Loading | Take water before start m/c at 1:10 | |
Detergent (NOPS) | 1 g/l | Cold wash | Normal temp. | 40˚C – 10´ |
Stabilizer & sequestering (CONL) | 0.5 g/l | |||
Anti creasing (NC) | 0.5 g/l | |||
Anti forming | 0.5 g / l | |||
Viscose color | 3 g/l | Scouring & bleaching | Dozing 40˚C – 7´ | 70˚C – 60´ |
BD | Before BD absorbency check | |||
Per oxide killer (Biokil) | 0.3 g/l | Inject | 40˚C – 10´ | |
Hot | – | Washing | – | 80˚C -10´ |
Acetic acid | 0.5 g/l | Neutralization | Inject | 50˚C – 10´ for pH = 6.00 ~ 7.00 |
Wash | – | |||
Leveling ( REB) | 1 g/l | Leveling | Temperature Increase at 60˚c | 60°C – 10 ´ |
Sequestering (CONL) | 0.5 g/l | |||
Anti creasing ( NC ) | 0.5 g/l | |||
Salt | 80 g/l | Migration | 5 % dozing 60˚c – 10´95% doz. 10´ | 60˚C – 10´ 60˚C – 10´ pH below 7 |
Salt |
R/T orange ME – 2RL | 3.46% | Color | Dozing 60˚C – 20´ | 60˚C – 10´ |
EVR. Red 3BS | 2.76 % | |||
Cotton blue | 0.0044% | |||
Soda ash | 20 g/l | Fixation | 1% dozing 60˚C – 20´5% – 20´94% – 20´ | 60˚C – 10´ 60˚C – 10´ pH 10.5 60˚C – 10´ |
Soda ash | ||||
Soda ash | ||||
BD | Before BD sample check (Shade) | |||
Acetic acid | 0.5 g/l | Neutralization | Inject | 40˚C – 10´ |
BD | Before BD/rinse sample check (Shade) | |||
RSK | 1 g/l | Soaping | Inject | 80˚C – 10´ |
BD | Before BD /rinse sample check (Shade & soft) | |||
Fixer | 1 g/l | Fixing | Inject | 40˚C -10´ |
Materials | Unloading |
Table: Modal fabric dyeing process with Reactive dye
N.B: Viscose fabric dyeing process is same as to Model fabric dyeing process. Do not use caustic & peroxide, viscose color is a multifunctional chemical which perform scouring & bleaching. Viscose fiber has more absorbency than cotton so liquor ratio uses 1:10. So possibility to uneven dye to prevent it used high liquor ratio & carefully dozing salt and soda.
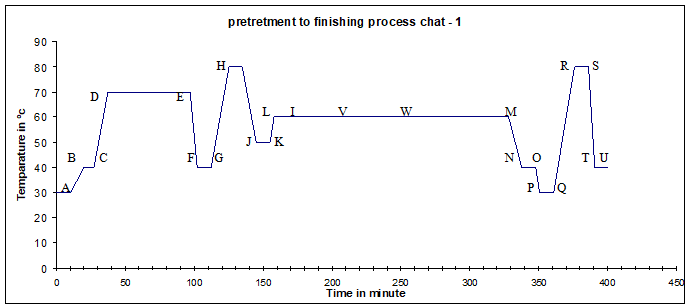
Where,
A= Cold water loading
B= Fabric, Detergent, Stabilizer, sequestering, Anti creasing, Anti forming Inject.
C= Viscose color (Scouring & Bleaching Agent) dozing then temperature increase at 3ºc/min.
D= Scouring and bleaching running
E = Scouring and bleaching bath drain
F= Peroxide killer Inject
G= Temperature Increase 3ºc/min
H= Hot wash
J= Neutralization to remove residual alkali
K= Fresh water taken for dyeing then temperature Increase
L= Leveling, Sequestering, Anti creasing, dozing.
I= Salt dozing,
V= Color dozing
W= Soda ash dozing
M= Color bath drain
N= Fresh water taken and Neutralization
O= Acid Bath drain
P= Fresh water taken for soaping
Q= Soaping agent Inject then temperature increase 3ºc/min
R= RSK (soaping) running
S= Soap bath drain
T= Fixer Inject
U= Fabric Unloading
You may also like: General Dyeing Procedure of Cotton Fabric with Recipe