Garment Checking:
Checking is an activity where the stitched garments will be visually inspected for any defects or poor workmanship which will not meet the required quality parameters. The defects which are identified will be rectified if possible or if cannot, they will be marked with the help of arrow sticker and that particular piece will be rejected. Only good quality pieces will be passed for the next process. Here the uncut protruding sewing threads also will be trimmed in the checking activity. In this article I will discuss both checking and packing cost in apparel industry.
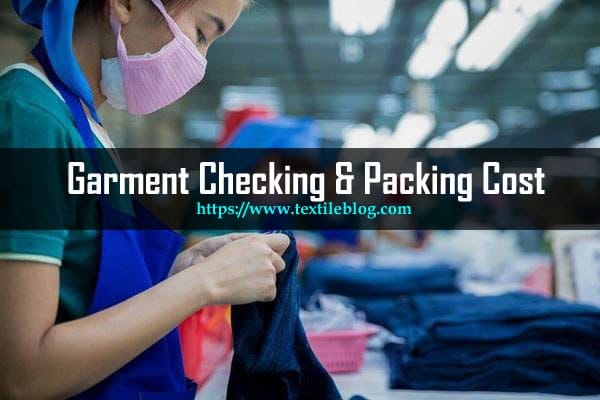
The process sequence in the checking process is as given below:
Checking or inspection
↓
Defects identification
↓
Rectification (if possible)
↓
↓
Bundling
Formula:
The formula to find out the checking cost is as follows:
Cost elements:
The cost elements involved in the checking process is as follows:
DM = Size stickers (if possible)
DL = Checking persons
DE = Cost of re-checking
OH = Power, rent, transportation charges, salary etc.
Cost factors:
The various factors which influence the checking cost are as follows:
- Style of garment
- Garment details
- Quality level
Cost examples:
The approximate checking cost for various garments are as follows:
T-shirt = BDT3.00
Shorts = BDT2.00
Brief = BDT1.00
Garment packing cost calculation:
Packing includes the activities of designing and producing the container for a product. This includes two levels of packing, first is the primary or inner packing in which the garment is packed in a poly bag or transparent pouch or inner carton box and the second is the secondary or outer packing in which the primary packing is packed in a corrugated carton box which facilities the easy and safe transportation of the products.
There are certain other garment packing materials are also attached to the garment for the purpose of good appearance or identification or giving information to the customers. These include tags, barcode stickers, insert card, size and color stickers, hangers, hologram stickers etc.
The garments are packed as per the requirements of the buyer which may be a single or combo or bulk packing. Assortment ratio is also an important factor in the outer packing which means the ratio of sizes and colors to be packed in one carton box.
There are four types of assortment:
- Solid size and solid color – in which carton box will have only one color and one size;
- Solid size and assorted color – in which the carton box will have one size but all colors;
- Assorted size and solid color – in which the carton box will have all sizes but only one color and
- Assorted size and assorted color – in which the carton box will have all sizes and all colors
The process sequence involved in packing process in as follows:
Tagging
↓
Folding
↓
Inner/Poly bag packing
↓
Outer/carton packing
↓
Strapping the carton
Formula:
The formula to calculate the packing cost is as follows:
Cost elements:
The cost elements involved in the packing process are as follows:
Direct Material (DM) = Tags, poly bags, labels, hangtags, hangers, pouches, barcode stickers, hologram stickers, insert card, inner box, carton box, packing strap, gum tape, tag bullets, color stickers, price stickers, size stickers etc.
Direct Labor (DL) = Packing labors
Direct Expenses (DE) = Cost of re-packing, hiring charges of carton-strap packing machine
Over Heads (OH) = Power, salary, transport etc.
Cost factors in packing cost:
The various factors which influence packing cost are as follows:
- Style of garment
- Types of packing – single, combo, bulk packing
- No. of packing material
- Type of assortment
Cost examples:
Depends on the packing requirements.