Fabric cutting is the most important step in garment manufacturing. It is totally different from general cutting. This term, fabric cutting is only applicable for garments manufacturing technology. Garment quality depends on accurate fabric cutting. Besides, fabric wastage also depends on accurate fabric cutting. For fabric cutting process, various types of fabric cutting machines are used. Different types of fabric cutting machines are shown in below figure-1.
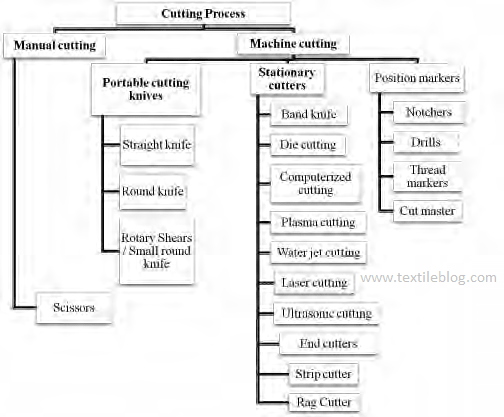
Fabric Cutting Machines:
Fabric cutting machines are classified mainly in two classes. The names of the machines of both classes are listed below:
A. Manual method or manual fabric cutting machines:
- Hand operated scissor
- Round knife
- Straight knife
- Band knife
- Die cutting
- Notcher
- Drill
B. Computerized method or computer controlled fabric cutting machines:
- Knife cutting
- Cutting by water jet
- Laser cutting
- Plasma torch cutting
Above types of fabric cutting machines are described below:
1. Hand operated scissor:
This is the first of all and the most ancient method of cutting of fabric. Scissors are generally used for cutting of one or two plies of fabrics. After good practice fabric can be cut perfectly and accurately. There are separate scissors for handling the scissors with right hands or with left hands. It is possible to cut almost all types of fabrics with scissors. It takes much time to cut fabrics with scissors and the fabric cutting cost for each garment comes higher. For this reason, the use of scissors is very much limited in the garments industry. But in tailoring shops or in houses only the scissors are used mostly for cutting of fabrics.
2. Round knife:
It is a knife like a round circle. The end of this knife is very sharp and it is operated at very high speed with the help of motor and electrical power. The round knife is operated at a speed of 1000 to 3500 RPM. The diameter of the blade may be from 6cm to 30cm. the main parts of this machine are: base plate, electric motor, handle, blade guard etc. The round knife machine is shown in figure-2. The edge of the blade may be of three types, such as: waved, toothed and circular. The capacity of fabric cutting of a round knife is ten times greater than the capacity of a straight knife of the same RPM.
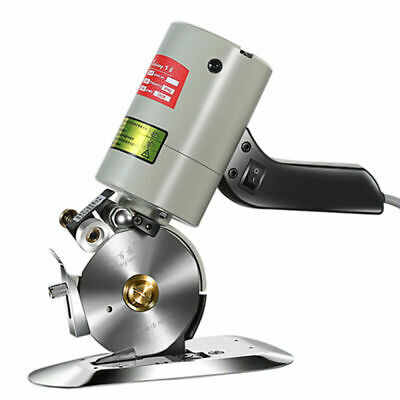
For the round knife there are a number of disadvantages which have been discussed here. A fabric lay of up to the 40% height of the diameter of the round knife blade can be cut. It is very much unsuitable to cut the small parts of the garments from the fabric lay, specially to move the blade along the curved lines with such type of blade. Like the straight knife, fabric cannot be cut with this machine from a lay made at 90 degree angle with the base. As a result, well experienced man of fabric cutting is required to cut the parts of garments from the fabric lay with this type of machine. Round knife is used to cut and separate the bigger parts of the garments and for cutting and separate the blocks of the fabrics from the fabric lay of comparatively low height.
3. Straight knife:
Among all fabric cutting machines, stright knife is widely used knife in the garments industry is meant to be the straight knife. The main parts of this machine are a base plate at the bottom of which there are small wheels attached, with the help of which this machine can be moved on the cutting table easily. With the help of stand on the base plate an electric motor is set on the stand. There is handle with the motor with the help of which the machine can be operated in various directions. The straight knife is set inside the stand or the upright. There is a knife guard in the front of the knife. There is a grinding wheel at the side of the straight knife with the help of which time to time the knife is sharpen during the cutting of the fabric.
Two types of power are required to cut the fabrics with such type of fabric cutting machines, such as: the straight knife is made running speedily up and down (reciprocally) by a motor and the cutting knife is operated manually in various directions in the fabric lay. The required power of the motor depends on the height of the fabrics lay, construction of the fabric, the amount of the curved line the fabric will be required to cut and on the stroke of the blade. The greater the power required for the motor the heavier will be the cutting machine. The greater the height of the blade, so will be the thick and the housing or the standard of the blade. The height of the blade is generally from 10cm to 33cm and the stroke from 2.5cm to 4.5cm. The greater the speed the blade, the greater the amount the fabric cutting will be done. Again the heavier the cutting machine will be, the greater the amount of energy will be required for the cutting man to operate it. The sharp side of the cutting knife may be of various shapes which are shown in figure-3. Generally the straight edge is used most and is used for cutting the soft and light lay of fabric. The wave edge is used for cutting of plastic, the saw edge is used for cutting of canvas fabric and the serrated edge is used for cutting of hard and coarse cotton fabric. For cutting of various types of fabrics, various speeds are set in the same machine. This type of cutting machine is shown in figure-3.
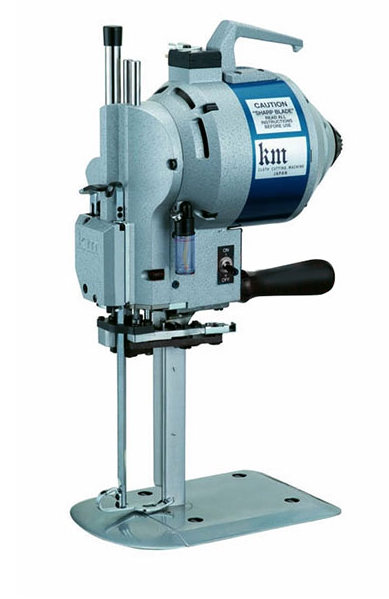
Presently the straight knife machine has been made more improved. The machine has been adjusted with a hanging hand from a stand at the side of the cutting table and the big and heavy base plate of the cutting machine has been replaced with a small thin base plate. The hanging arm bears the total weight of the machine and the motor. As a result, it has been possible to use comparatively the thin standard of the straight knife. Due to these changes, with the help of the improved straight knife, it is becoming much easier and more speedy to cut the fabric by the cutter man. This type of machine is also shown in figure-3. The advantages and the disadvantages of a straight knife cutting machine are listed below:
Advantages:
- As comparatively cheap, can be moved easily and fabric of maximum height lay can be cut for this reason, this is a widely used cutting machine.
- Fabric can be cut in more curved line than the round knife.
- Suitable for much production because fabric can be cut up to the lay height of 10 inch.
- Fabric can be cut rapidly.
- The garments parts can be separated directly from the fabric lay.
- During the running of fabric cutting, the arrangement for sharpening of the blade is attached with the machine.
- Fabric can be cut in any angle.
Disadvantages:
- During the cutting of fabric, due to the knife deflection caused by the weight of the motor, fabric cutting along the specified line may be troublesome.
- The greater the height of the fabric lay will be, the greater the trouble due to the cause of knife deflection will arise.
- The greater possibility of accident.
4. Band Knife:
This machine resembles much with the wood cutting machine but it is smaller in size. The endless loop shaped with thin steel blade is set with the help of a few pulley. Then the endless knife is operated with the help of a motor. Through the specific slot on the cutting table of the band knife the cutting blade continuous to round at the specific speed and at the same direction. The cutter man places the block of the fabric lay along the blades and cuts the parts of the garments through moving. The blade of the band knife cut the fabric lay at 90 degree angle. For the cutting small parts accurately, this machine is used in many garments factories. The templates are used often for cutting accurately. The picture of the band knife machine is shown in figure-4. The advantages and the disadvantages of this machine are listed below:
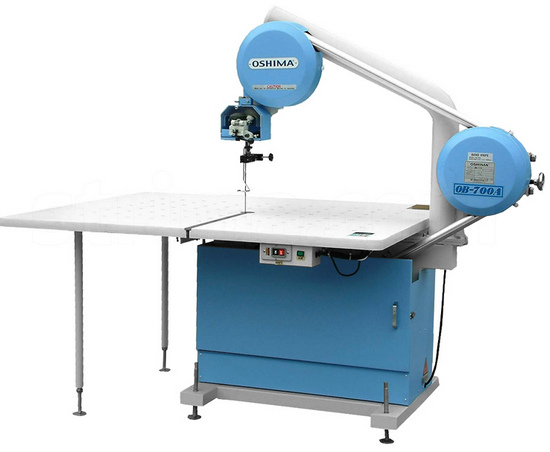
Advantages:
- Fabrics are cut more accurately and perfectly.
- Suitable for cutting the small parts of garments accurately.
- It is easy to cut the fabrics in any angles or in angular shapes.
- Due to the facility of using template, accurate and consistent cuttings are much easier.
- Less risky of accident than straight knife or round knife.
Disadvantages:
- As fabric blocks are required, the fabric wastage is higher.
- As the machine remains static and the cutting job is through moving the fabric block, the work load is higher.
- This method is not suitable for cutting comparatively the bigger parts of the garments.
5. Die Cutting:
Die cutting machines are mainly of two types. Such as: clickers and presses. The main parts in all types of die cutting machines are: cutting blade, ram head, die, motor, the method of ram operation and the controlling system and ram’s height. The method of ram operation is the main difference between the die cutting machines.
The die is made with metal strip as per the shape around the pattern. Steel strip or forged die is used as the metal strip. One end of this strip is sharpen and a tie bar is set on the other end. Placing the die on the block of fabric lay, pressure is exerted with the help of ram head. As a result, the sharp end of the bar goes inside the fabric lay cutting the fabric. This way, as per the shape of the die, the pattern of exact dimension is cut from the fabric lay. For very accurate and perfect cutting of small parts, die cutting is a very good and widely used method. For obtaining good cutting in die cutting method, the die needs to be accurate, the cutting blade is to be accurate, the ram surface, cutting blade, fabric lay and die are to be controlled in parallel conditions and pressure has to be exerted as per the needs. If the pressure is high the die blade may be damaged on the contrary cutting may not be properly done, if the pressure is low.
During setting of die on the fabric lay, a gap of 2 to 4 mm is kept from one die to the other, otherwise cutting problem may happen. Die cutting comparatively takes lesser time but it takes time to make the die. The picture of a die cutting machine is shown in figure-5.
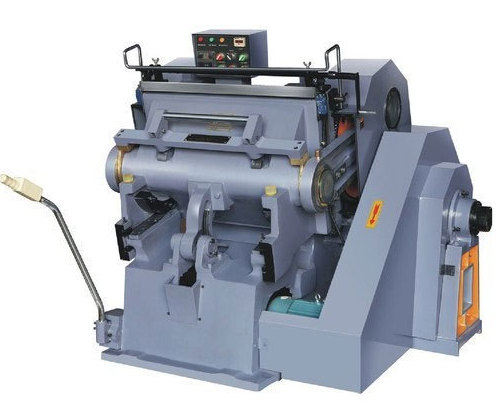
Advantages:
- Very much suitable for accurately cutting the small parts of a garments.
- Suitable for cutting in any shape or in any angle.
- Can be cut comparatively in a lesser time.
- This method is the best for the knitted fabrics.
Disadvantages:
- As blocks of fabric lay is required, there happens much fabric wastage.
- Labor cost is high.
- Frequent changing of styles is inconvenient because for making new die both time and money are required in bigger amount.
- Inconvenient to cut the big parts of the garments.
6. Notcher:
This is a special type of cutting machine and its use remains limited within a specific field. It requires to cut notches in the edges of some parts of garments. As a result, during sewing it becomes easier to join the parts matching with the certain places. This job for making notches can be done by ordinary straight knife or by the other cutting machines, but consistent notching depends on the skill of the cutter man. Notcher machine has been invented only for making notches and a special guide helps making consistent notchings. Notches can be made in “U” shaper or in “V” shape.
There are systems for applying heat in some notcher machines. During making notches, cutting knife is heated. As a result, the tendency of fraying of threads along the cut notches are prevented. But it may be inconvenient to use heated notcher in the cutting of those fabrics whose naps are fused in heat. Notcher machine can be used only for making the notches but it cannot be used for any other purposes. The notcher machine is shown if figure-6.
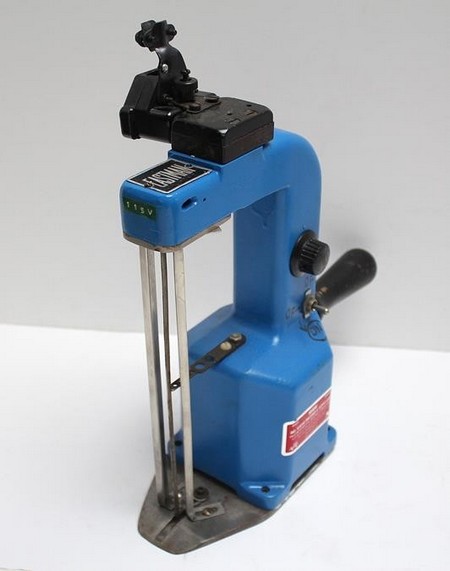
7. Drills:
Sometimes it is required to mark on some places in various parts of garments, specially for the reason of placing the pockets, making the darts etc. Drill machine is used to mark except the edges of the garments this means for marking in the inside places. There are a motor, a base plate, drill and spirit level in this machine. With the help of spirit level, the movement of the drill in the fabric lay is ensured at 90 degree angle. The hole made with drill in tightly woven fabric lasts long but the drill made in loosely woven fabric may not last long. Sometimes heated drill is used, which helps the holes to remain stable. With the use of hypodermic drill, light colors are thrown along the holes resulting in more easier to finding out the holes. Threads may also be inserted through the holes so that the holes are not closed. In whatever ways the holes are made with drills, it has to be ensured that the holes will not be visible after making of the garments. A drill machine is shown in figure-7.
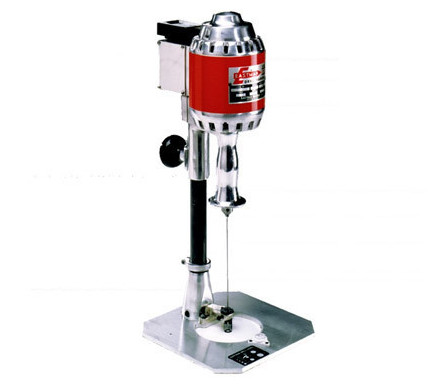
8. Computer controlled knife cutting:
Computer controlled cutting machine has brought revolutionary changed in fabric cutting machines. It has been discussed earlier about the computer aided marker planning. With the help of computer, fabric lay also can be cut guiding the cutting knife in the pre-settled path or by guiding along the line. In this method fabric is cut very accurately and very quickly.
The surface of a cutting table is different from that of a general table. The table surface is covered by the bed of a nylon filament, on which fabric lay is placed. The bed of nylon filament is capable of bearing the weight of the fabric lay and it helps to get the cutting knife into it and its movement in various directions. As a result, it ensures cutting of every ply of fabric in the fabric lay by the knife. In addition to that, it helps to holding the lay tightly with the cutting table by making vacuum by soaking the air through the filament.
Along the width on the cutting table, there is a beam which runs along the length of the table. The cutting head is set on the beam, which runs along the length of the beam. The cutting head can move to any point or to any direction in the lay with the help of three servomotor. There is a cutting knife in the cutting head and there is arrangement for sharpening the cutting knife automatically and there is arrangement for rotating the knife at any directions along its center point. A polythene sheet is spread on the fabric lay which helps in making vacuum. The cutting knife is operated by necessary signals from the computer cabinet attached by the side of the cutting table.
Receiving the instruction through computer, the cutting knife starts cutting from a reference point in the marker. Notches in the specific place of the parts of the garments are also made by the same cutting knife, but for making drills, there is separate drill in the cutting head, which makes drill marking in specific places of specific parts. The speed of fabric cutting depends on the height of the fabric lay. For example, the per minute speed of the cutting knife for a fabric lay of 7.5 cm high is 7.5 meter. With the advancement of the fabric cutting, another polythene sheet is spread right away on the cut fabric so that they are not free from vacuum.
Marker is not required for computer controlled cutting. Because, the cutting knife cuts the fabric as per the instructions of the computer memory. But sometimes markers are placed on the fabric lay for easy identification and separation of the cut bundles. A computer controlled knife cutting machine is shown in the figure-8 and the advantages and disadvantages of this machine are listed below:
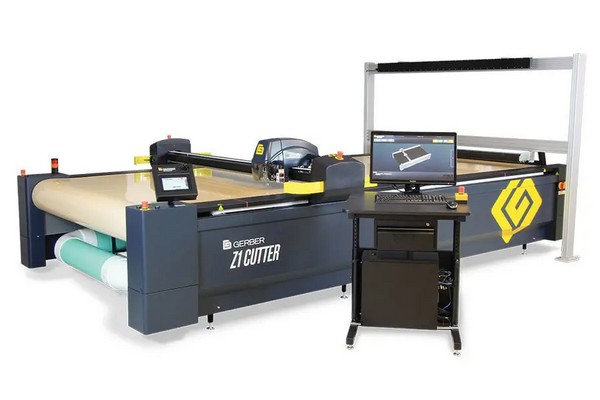
Advantages:
- Fabric can be cut very rapidly.
- Fabric can be cut very accurately.
- The speed of fabric cutting can be controlled.
- The cutting knife can be moved and operated in any directions.
- Suitable for production on a large scale.
- Can be attached to computer controlled marker making.
- The fabric lay is compressed which helps cutting of the fabric.
- During cutting of fabric, the fault are comparatively lower than the other methods.
- The possibility of blade deflection is less.
- There is arrangement for sharpening of the blade.
- The possibility of accident is less.
- Marker is not required for cutting of the fabric.
- Labor cost is less.
- Fabric can be cut 6 to 8 times faster than the manual methods.
Disadvantages:
- The initial capital investment is high.
- The maintenance cost is high.
9. Cutting by water jet:
The fine jet of water is flown at a very high speed with a very high pressure through the opening of a nozzle. The water pressure is generally kept at 60,000 pound per square inch. But for increasing or decreasing the cutting capacity, the pressure may also be more or less. This jet of water acts like a hard and sharp device with the help of which cutting of fabric, skin or plastic material can be done easily. The material or fabric which are cut, the greater the thickness of the lay, the quality of the cutting of the bottom layers will be less. Because, the water jet as much as it progresses in the depth of the lay, its momentum decreases. As a result, the cutting of the bottom layers will be wide and unfair. For this reason, in this method the fabric lay in more height is not cut.
If the water jet from below the fabric lay with which the fabric is cut is not hold from below the fabric lay, then the table may also be cut. For this reason, a catcher is used below the fabric simultaneously with the water jet at the same speed and at the same direction. The water which is used for making water jet is made previously filtered and deionised. For speedy cutting of fabric, it is necessary to adjust the water pressure, diameter of the jet and the speed of the jet. The advantages and disadvantages of this method are listed below:
Advantages:
- Fabrics can be cut in comparatively high speed.
- As the knife is not used for cutting of fabrics, so there is no matter for sharpening of the knife here.
- Suitable for cutting of comparatively hard material.
Disadvantages:
- Inconvenient for cutting of fabric lay of more height.
- The cutting end of the fabric gets wet.
- There may have water spot.
- It is required to filter and deionise the water.
- During cutting of the fabric lay of multilayer, fine and accurate cutting in the bottom layers may not be possible.
- It is required to control the sound of the jet.
10. Cutting by laser beam:
In this method fabric is cut by reflecting the light ray in a very minute shape with the help of a laser. This minute light spot is in 0.25 mm diameter and it is of high powered. When it is reflected on any material then it creates heat in that material and performs the cutting by evaporation. The tendency of charring is prevented by flowing the inert gas in a jet form and by flowing gas the dust ash material from the cutting place are removed. There is a possibility of “V” cutting in case of cutting fabric lay of more layers. For this reason, this is suitable for cutting of a single layer fabric. Fabric can be cut in a very high speed that means 13 meters per minute. The cutting head is controlled by computer. The advantages and the disadvantages of this cutting method are listed below:
Advantages:
- In a very high speed, that means 13 meters can be cut per minute.
- As the cutting head is controlled by the computer, cutting can be made along the correct line.
- As the fabric is cut by light ray, sharpening of the cutter is not required.
Disadvantages:
- The fabric lay of multi-layer cannot be cut properly.
- In case of synthetic fabrics, the cutting end may be fused.
- Expensive method.
11. Cutting by plasma torch:
In this method fabric is cut by very fine flame caused by flowing the argon gas though nozzle. Fabric can be cut in one or more layers. But it is suitable for cutting single ply fabric. The table on which the fabric is cut, its surface should have 85% holes. Still research regarding this method is going on.
References:
- Garments & Technology by Prof. M. A. Kashem
- Apparel Machinery and Equipments by R. Rathinamoorthy and R. Surjit
- Garment Manufacturing Technology by Md. Shafiul Azam, Md. Abu Saleh & Khondokar Abu Nafiz
- Apparel Manufacturing Technology by T. Karthik, P. Ganesan, D. Gopalakrishnan
- Garment Manufacturing Technology Edited by Rajkishore Nayak and Rajiv Padhye
dear sir
We are a big factory of garments in Egypt and we are in need of those equipment’s