What is Fabric Grouping?
Fabric occupy for 60-70% of the total operational cost of any garment manufacturing unit. It is essential to make use of this component wisely. Just good marker planning is not enough. Fabric utilization is a function of several aspects in the functioning of a factory.
Fabric grouping, it is also called fabric batching, is the main process that will give improvement with respect to material utilization along with improvement in quality control. It is a technique used in the textile industry to categorize fabrics based on their characteristics and properties. Here the fabric rolls are categorized to create fabric groups with identical properties with reference to fabric width, shade and shrinkage, where each of these considerations can have different implications on marker planning, cutting plan and fabric utilization and have a critical influence on the overall material utilization. Fabric grouping helps to identify and distinguish different fabrics, making it easier to select the appropriate fabric for a specific project or application. It is an important aspect of the garment industry, as it allows manufacturers, fashion designers, and consumers to make informed decisions about the fabrics they use.
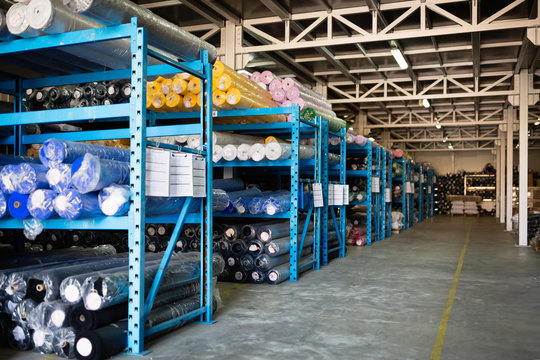
Different Types and Parameters of Fabric Grouping:
Fabrics can be grouped in various ways based on different criteria, including fiber type, weave, texture, and intended use. Here are different types of fabric grouping:
1. Fabric grouping by shrinkage:
Every fabric roll is determined for its shrinkage level and could result in different warp and weft shrinkages. An adequate level of shrinkage is decided based on measurement tolerances and buyer guidelines. This acceptable level is used to generate fabric groups within a certain warp and weft shrinkage acceptance level. The fabric rolls of one group should not be mixed with any other group of rolls. Several garment industries carry out the process of dividing the order quantity in the ratio of shrinkage groups and treat each group as a separate order. This kind of approach is useful only if the quantity in each group is large.
2. Fabric grouping by width:
Generally, the variation in width of the fabric will be noticed between the fabric rolls received by the garment industry. The markers should be made with the width equal to the lowest available width of the fabric if the fabric rolls are not grouped according to the fabric width, which leads to substantial fabric wastage. If the marker is created with the lowest width of the fabric in the lot and the patterns remain unaltered, then the fabric rolls having higher width could be mixed with fabrics having lower width. The fabric rolls are separated in different width groups and the major markers are cut with the relevant groups to get the maximum benefit of width. Once the remnant planning is started, these groups can be mixed to minimize the number of spreads and have a better utilization of labor and time.
Width grouping will happen normally and disregarding this aspect creates possible wastage; for example, if the fabric rolls are received in the garment unit with two different fabric width groups and each has the same quantity of fabric.
Group 1: Fabric width = 1.48 m, total fabric length in a roll = 120 m
Group 2: Fabric width = 1.45 m, total fabric length in a roll = 120 m
- If the fabric rolls are not grouped based on width, then combined cuttable width = least width of the fabric in all fabric roll groups = 1.45 m
- Total cuttable area without fabric grouping = (1.45 × 100) + (1.45 × 100) = 290 m2
- Total cuttable area with fabric grouping = (1.48 × 100) + (1.45 × 100) = 293 m2
- Hence, fabric wastage because of nongrouping of fabric rolls = 293–290 = 3 m2
- Fabric wastage (%) = (3/290) × 100 = 1.03%
3. Fabric grouping by shade:
Fabric grouping based on fabric shade is generally the regular method of grouping. Most garment industries have received fabric in different shades. In this situation, there is no change in the pattern or the marker. Hence, these fabric rolls could be spread together in a lay. However, many garment industries prefer to separate them and utilize only one shade in a spread and at this point the method of shade grouping is used. To obtain the full advantages of shade segregation, the remnants and end bits should be marked with shade to make sure that part change occurs from the required shade only. If this operation is skipped and visual authentication is used for part change, then there is more of a chance of rejections and poor quality product.
4. Manual grouping approach:
Normally, fabric grouping is done manually during the production planning operation. One main garment style of fabric grouping splits the total order quantity in the grouped fabric quantity’s ratio and then treats them separately.
For example, the order quantity in S size is 90, M size is 150 and L size is 60. For instance, if the consumption of fabric is 1 m, then 300 m fabric should be procured. Now, consider that the fabric rolls are received in two width groups.
- Group 1: Width of fabric = 1.48 m; fabric roll length = 200 m
- Group 2: Width of fabric = 1.45 m; fabric roll length = 100 m
Group 1: Group 2 = 2:1. Therefore, after breaking the order quantity in the same ratio and allocating them to groups, it will be as shown in below Table.
Order Quantity as Per the Ratio of Roll Width
S | M | L | |
Group 1 | 68 | 113 | 45 |
Group 2 | 22 | 37 | 15 |
Total | 90 | 150 | 60 |
Now, if 3-way markers for the lays are put, then each group will have its own cut plan.
Problems in Manual Grouping Approach:
- Too many markers: In the example shown above, both the fabric groups I and II had the same cut plan markers, hence they have to be created twice (total number of markers – 6).
- Too many lays: The number of markers to be made is doubled as well as the number of lays, which significantly increases the spreading time.
- Too many cuts: By considering the same example above, the number of patterns or bodice cut is 16. The number of bodice cut will continue to increase with more groups, more markers and more number of lays.
- Dependency of fabric ratio: The above explained example needs the fabric ratio to be preknown. This leads to a complex situation in the case of huge orders where the fabric is received in multiple drops and this leads to wastage of time as well as fabric.
5. Automated grouping:
This method compared to manual grouping should minimize the number of lays, markers, as well as bodice cuts.
Benefits in Automated Grouping Method:
- Less number of markers – Instead of 6 markers in the manual method, only 4 markers are adequate.
- Less number of lays – Instead of 6 lays in the manual method, only 4 are sufficient.
- Less number of bodices to cut – Only 12, as opposed to 16 in the manual case.
Suppose there is a shade-wise shipping requirement that could also be mentioned in the automated process and the system will ensure those criteria are followed.
Characteristics of a Good Fabric Grouping:
A good fabric grouping should-
- Increase fabric utilization, thus reducing overall consumption.
- Do not increase too many lays and markers as a lot of benefit gained by saving fabric will be lost in increased workload.
- Do not create too many groups as it will become difficult to manage and control by the factory workforce.
- Consider all scenarios for each case before deciding on the group range instead of following a standard set formula.
- Be easy and simple to understand and follow.
Conclusion:
Fabric grouping is a useful tool for categorizing and identifying different fabrics based on their characteristics and properties. Understanding the various types of fabric grouping can help manufacturers, designers, and consumers make informed decisions about the fabrics they use, ensuring that the right fabric is selected for the specific project or application. The choice of fabric can greatly influence the functionality and aesthetics of a finished product.
References:
- Apparel Manufacturing Technology by T. Karthik, P. Ganesan, and D. Gopalakrishnan
- Practice of Garments Merchandising and Management by Engr. Md. Faruk Hosen
- Garments and Technology by M. A. Kashem
- Mausmi Ambastha, “Do you group fabric in your factory? Do it NOW” https://www.linkedin.com/pulse/do-you-group-fabric-your-factory-now-mausmi-ambastha
- Dinesh Exports “Understanding Fabric Grouping: A Comprehensive Guide” https://dineshexports.com/fabric-grouping-guide/
You may also like: Fabric Characteristics | How to Evaluate Fabric Characteristics