What is Fabric Spreading?
Fabric spreading is an important operation in garment manufacturing. It is a sub section of fabric cutting department in apparel industry. Fabrics are cut at a time for a number of garments in apparel industries. Fabric spreading is the process of laying fabrics in stack from as per marker length & width. Multiple spreading is performed by spreading machines, which provide fabric feeding & transportation, ensure tension free spreading & material cutting in needed length pieces. The shape of the fabrics that is attained as per spreading of fabric is called the fabric lay. In the fabric lay, there may have fabrics in two to hundreds of layers. Trying to represent the maximum number of fabric plies in the lay, the programme generates all spreads. Fabrics with similar properties are grouped together for one spread to reduce spreading time. If a disproportionate number of layers (very small number) appears for separate spreads, the programme can perform automatic balancing.
Generally fabric spreading is done by two ways; manually and automated. The manual spreading process is suitable for small-scale production. Manual spreading may be used for all types of fabrics. Automated fabric spreading is done by different types of machines. This spreading systems have significantly increased the productivity of the spreading process, but have not altered its main work principles. Fabric lay is done mainly for achieving two objects – for fabric saving and for time saving during cutting of fabric for each apparel.
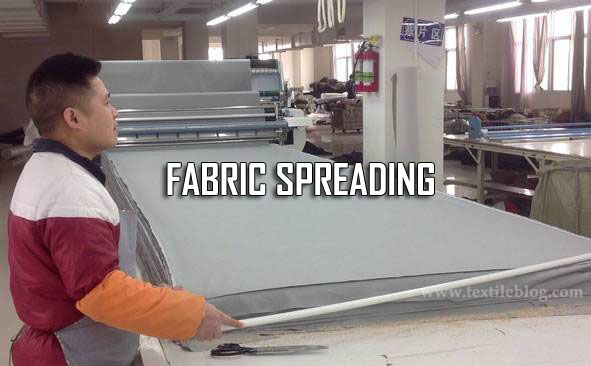
As the fabric lay is made by spread of hundreds of layers of fabrics and it is done on the cutting table, the construction of the table should be strong one and the top of it should be well smoothed. Specially, if the spreading machine is set on the spreading table, the table should be better constructed. The good quality spreading table possesses holes on their tops through which air is blown outside from the inside. As a result, it becomes easier to remove the fabric lay or its parts from the spreading table. Also there may have system for sucking air and as a result the height of fabric layer may be lessen by air compressing and ultimately fabric cutting becomes more easier.
Fabric spreading is a time consuming job. A detail discussion on fabric is done in this article below as it is essential to know the various technical and efficient ways of fabric spreading, specially for the purpose of good fabric spreading and its proper cutting.
Requirements of Fabric Spreading:
For making accurate and fair lay of fabric after spreading, a number of conditions and technical aspects need to be full filled. Among the conditions, some are compulsory and others are not compulsory but it is good if they are full filled. The conditions are discussed below of which first three are basic requirements and the remaining are additional requirements. Whatever way the fabric spreading is done, the basic requirements must be full filled.
a) Alignment of fabric plies (basic requirements):
Fabric spread is done as per the length and width of a marker. It is strictly maintained so that each of the fabric plies is placed perfectly within the length and width of the marker in laying during the spreading of fabric. Otherwise the fabric of any ply which will be placed beyond the dimension of the length or width of the marker will be cut defectively. In order to avoid this mistake, each of the plies is placed and controlled along the width maintaining the selvedge of at least one side in the same line. Also sometimes, along the width of the fabric, the center position of it is placed and controlled in the same place.
In order to ensure the length of each ply along the length of the marker, the length of the fabric lay is kept 2cm larger than the marker length in each end.
b) Correct ply tension (basic requirement):
Fabric lay is made fairly by placing one ply of fabric above the other. Fabric lay can be done manually as well as it can also be done by machine. Whatever way the fabric spread is done, it must be ensured that each ply of fabric must be tension free. During fabric spreading it is to be taken care so that fabric spread is not done in loose condition, because if it happens, then fabric lay will be defective, fabric cutting will be inconvenient and patterns will also be defective.
During fabric spread, if it is done with high tension, then after cutting of the fabric or after sewing, shrinkage may happen in various parts of the garments and the result of which will cause the production of defective garments. For this reason, fabric tension has to be maintained with great care during the spreading of the fabric.
There are some fabrics where there are inherent tensions, which may be developed during fabric weaving or finishing or roll formation. These fabrics need to be made tension free before making the fabric lay. Some fabric such as knitted fabrics or in the fabrics where there are elastic yarn or textured yarn, those fabrics are prone to become longer. During spread of these fabrics, special attention is given and in addition to that fabric is cut 12 to 24 hours after laying, so that fabric can relax to its normal condition by this time.
In order to overcome this tension problem during fabric spread, modern spreading machine can be used and if modern machine is used then some additional related benefits may be obtained.
c) Fabric must be flat (basic requirement):
During fabric spreading it must be kept in observation so that no folding or crinkles are there in fabrics. If these are found, then required measures have to be taken immediately to remove those. During fabric spreading if it is not done on flat condition, this means the mentioned defects are there, the pattern of that part will be defective and as a result the garments made with that pattern will also be defective.
d) Elimination of fabric flaws:
During fabric spreading if there is any fabric flaws then they are to be marked and necessary measures are to be taken to remove those flaws. The person, who will be in charge of fabric spreading, will have to bear the responsibility of marking of the fabric flaws and their removal. During fabric spreading if any flaws are found, then various measures can be adopted for their removal. For example, rejecting the fabric of the defective place, the fabric spread may be done through splice. If the splice marking is done in the marker beforehand, then it is to be followed, otherwise arrangement should be kept for sufficient overlapping so that all the patterns of that place are obtained in full dimension. During production of garments of comparatively cheap prices, sometimes fabric defects are overlooked during fabric spreading and during inspection after the production of the garments, the defective garments are rejected. Also, sometimes during fabric spreading if the fabric defect is in small place, then metal tape is attached at that place. Then after completion of fabric cutting, the bundles of fabric patterns are passed through a metal detector machine. The bundles which contain metal tapes are detected by that machine. The defective patterns are removed from the marked bundles and those patterns are replaced by cutting fresh pattern.
In modern time, during fabric spreading with computer, if there is any fabric defect, then it can be detected and how much spice is required for that defective part can be determined very promptly.
e) Correct ply direction:
Before spreading of fabric it is to be checked that what sort of fabric it is. If the fabric is symmetric (same in both sides), then no problem will arise. But if the fabric is asymmetric (different in both sides), then the side of the fabric ply has to be determined with caution based on the marker planning, otherwise garments may be defective. During making of fabric lay, the face of each ply of the fabric may be placed on the top side, bottom side or face to face.
f) Elimination of static electricity:
Static electricity may be produced in fabrics due to friction during making of lay through the spreading of fabrics. In the fabrics, especially where the proportion of synthetic fiber is high, the static electricity is produced in larger scale during the spreading of fabrics. As a result, it becomes complicated to place fabric of one ply to the other that means the plies of attraction or repulsion. For overcoming this problem, arrangements may be done to reduce frictions in fabrics or the amount of humidity in air can be increased in the room, or earthing of fabric lay can be done.
g) Easy separation of the cut lay into bundles:
The bundle size of the cut fabrics depends on the height of the fabric lay. During fabric spreading, differentiation marks among the fabric plies may be required due to the color or shade variation or for any other reasons. For making this differentiation, low priced colored paper layer is used between the fabric plies. After cutting of the fabric for differentiation between colored and non-colored in each bundle, the use of such colored paper is very much helpful. Moreover in case of slippery fabric, such colored paper helps to hold the fabric lay firmly. The colored paper used for this purpose is generally rough surfaced.
h) Avoidance of fusion of plies during cutting:
During the time of cutting of fabric lay with cutting knife, heat is created due to the friction between fabric and knife. The fabrics in which there are thermoplastic fiber, those fibers melt due to frictional heat. As a result, the melted matters take the form of polymer bid or grain due to joining together or the cutting ends join with one another. As a result, it becomes very much inconvenient to separate the patterns and defective patterns are created.
During making of fabric lay, anti fusion paper ply is spread between the fabrics layers at a regular gap so that such type of problems do not occur. There is greasy substance in anti fusion papers which lubricate the cutting knife during cutting of fabrics. As a result there is less friction between the fabric and the knife and the friction related heat is produced less. Due to the less amount of heat, the possibility of fabric to be fused becomes less.
i) Avoidance of distortion in spread:
During the removal of fabric lay or during the cutting of the fabric lay with straight knife, there may be folding mark or crinkle mark in fabric plies at the bottom of the lay due to the friction with the base plate of the knife. As a result, the defective pattern may be made after the cutting of the fabric. For the removal of such type of inconvenience, fabric lay is made on smooth paper. Moreover, due to the use of smooth paper, there is no possibility of rough face of fabric caused by friction of the table with the fabric.
j) Matching checks or stripes:
During the time of making of fabric lay by spreading of fabrics, need to keep observation so that if the fabric is check or strip, then one ply of fabric needs to be placed on the other by matching the checks or stripes properly. In the interest of matching the checks or strips in garments, marker planning also needs to be done by matching the checks and strips. This matching may be required to be maintained in warp direction, or in weft direction or both in warp and weft directions.
References:
- Garments & Technology by Prof. M. A. Kashem
- Garment Manufacturing Technology Edited by Rajkishore Nayak and Rajiv Padhye
- Apparel Manufacturing Technology by T. Karthik, P. Ganesan, D. Gopalakrishnan
- Garment Manufacturing Technology by Md. Shafiul Azam, Md. Abu Saleh & Khondokar Abu Nafiz