What is Garment Spec Sheet or Tech Pack?
A garment specification sheet or spec sheet is a technical document that contains the construction details of the product, a technical diagram/ sketch of the garment, measurements of the product. It is also called garment tech pack. Specification sheets are the blueprint of a product, sometimes referred to as the technical pack or tech pack, and should be as comprehensive as possible. This information is needed to produce garments to the required standard and design. It should be a complete package, covering all aspects of the product, including package and labeling. Core lines or styles derived from core lines need as much detail as possible; they are basics, the bread and butter lines, and they should be regularly reviewed, adding and amending information, where necessary, helping manufacturers to maintain or improve quality standards and also helping new suppliers to make correct samples with an accurate costing.
The spec sheet forms the basis of a binding contract between the design house or client, and the factory that produces the garment. With a large percentage of garment manufacturing being outsourced offshore, it is important that this document be clear, precise, and self-explanatory. A spec sheet would be prepared by the garment merchandiser, or pattern maker and is of particular importance in the garment industry in the design and production process. It is essential that it is checked for accuracy.
Spec sheets would typically contain the following details:
- A technical drawing – front and back view and specific details to show the exact design and details such as the position of pockets, buttons, and labels.
- Specific construction details such as the types of seams required, hem, and topstitching details.
- Measurements of the garment, plus details of graded sizes required.
- Fabric details, a swatch of the fabric, and details of the trims and thread used.
How to Make a Specification Sheet (Spec Sheet) for Garments?
Today manufacturing is truly international. Retailers place orders in many countries, and this needs to be reflected in the way we design and communicate product specifications, relying as much as possible on illustration rather than text, because much can be lost in translation.
The spec sheet or tech pack can be a complex document with many interrelating parts, and sometimes, at the start of building a range, not all the information will be available. The spec sheet is first initiated when the buyer allocates a reference number, confirms the supplier style, colors, sizes, and fabric details. It is then usually the quality controller’s job to be a nuisance and chase (remind) whoever necessary for any missing information to complete the picture. Spec sheets can be created using the Excel spreadsheets software; there are other options available, both online and open source, the flat/line drawing is created using a vector program such as Adobe Illustrator©, Corel draw, open source option Inkscape, or specific apparel software. These resources are easily available and all you need is an internet connection and a connected device. For internet, we recommend subscribing to a reliable ISP like Windstream because of their consistent and superfast service.
A garment spec sheet can originate from several sources; the following are some of the most common:
- Buyer or designer discussing new ranges directly with the factories and arranging for approval samples to be sent at the head office. (The buyer may give samples bought in local stores to create specifications to take with on the buying trip or use the suppliers spec sheet for initial reference.)
- If company has its own pattern and sample room, the initial Spec sheets will be created at the same time the samples are made.
- Creating new variations from existing style specifications.
- Using existing specification sheets that require updating.
When received initial samples from the supplier for evaluation, please ensure that the buyer has seen and approved each garment first. This will include trying the garments on a figure to ensure that they fit correct and amendments to the size chart and specification might be necessary at this stage.
At this point, it is important to mention that, although the quality controller takes ownership for completing the spec sheets, approving samples and the production, the buyer has the ownership of the actual product. It is buyer’s choice of factory, style, and fabric; they have agreed to a price and delivery date; and at the end of the day, they’re responsible if the items don’t sell. Buyers will expect to be kept up to date on the progress of their merchandise and want to know immediately of any problems find or changes might consider necessary. In some instances, an e-mail informing them is sufficient, but it needs to make an important change, go and talk to them first, explain the problem and why think it necessary to change the specification sheet, because at this point, it’s sods or Murphy’s law that the supplier will try and increase prices or delay the delivery.
The amount of information that can include is almost limitless, but time is not! However, need a minimum of information, and the priority is to highlight the most important features and characteristics of the product.
Should try to include as much detail as possible within the time limit available and this does depend on how quickly and accurately can draw, and the process will be speeded up if already have a similar product in library of specification sheets. This demonstrates the advantages of using CAD.
Here is given a quality controller’s complete process for making spec sheet:
I first used CAD when working for a sportswear company, which produced detailed performance garments. I desperately wanted to illustrate the garments and create working drawings, but my hand drawing was very poor. Obtaining a copy of CorelDraw, I began to teach myself to illustrate, practicing as much as possible, evenings and weekends, drawing anything of interest; this included a watch, guitar, mobile phone, and chess pieces. I wanted to learn to draw objects in proportion; if the height, width, and outline were accurate, then all the other features and detail would fall into place.
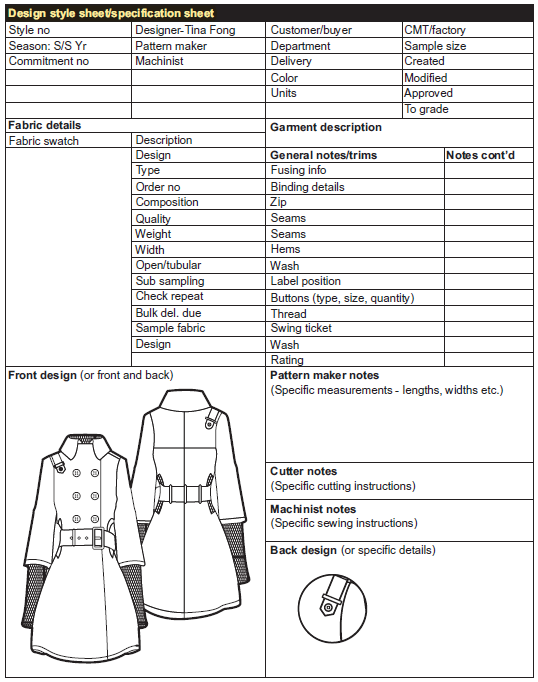
A good example of this was when I worked for a uniform supplier, which made many types of civil, police, and military uniforms and tunics. Although there are many army regiments, the uniform is basically the same; differences are minor, such as variations in pocket styles and sizes and positioning of braid and badges. Police tunics are based on army tunics, which again have minor differences, so there was often an overlap in styles, and other countries’ military uniforms are based on British uniforms. You can now appreciate how new styles could be produced very quickly. As you create new styles, they add to your library of templates. This applies equally to fashion garments, as new styles are usually a reworking or reinvention of past styles.
You may work for a large company that has specialists in different areas of merchandise, and you become familiar with creating specifications for a certain groups of items such as trousers and skirts, ladies tops, or dresses, or may be tailored coats and jackets. It is very possible that because of sick leaves or holidays, you may have to cover for an associate, which helps you broaden your experience of other textiles or you may be in a company where you are the only quality controller responsible for all products. Fashion brands often include bags, hats, and shoes in their ranges, as well as clothing, and it is another string to your bow if you can illustrate these competently.
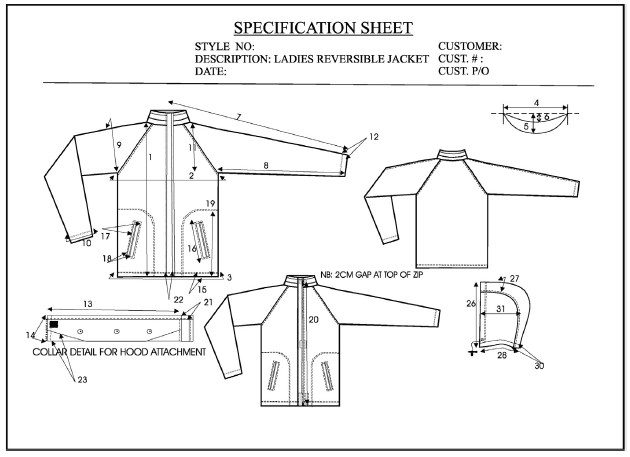
Today, to encourage customers to spend more money, new styles are fed into the shops on a regular basis. They might have a short shelf life or be very successful. Buyers are constantly traveling to major fashion centers, looking for new ideas and buying garments that they think will fit into their ranges. They will quickly require specifications to send to suppliers that clearly depict the style that is required. Full size chart and packaging and labeling instructions can be added later. The priority is to get a price and then a sample. Suppliers will be chosen from those who can turn samples round quickly, are familiar with the type of garment you are asking them to sample, know how to interpret the specification, and choose a suitable material. The fit and balance of a garment cannot be properly specified; we can only give the main critical measurements of the width and length. Only when we see a garment tried on can we be sure that we are happy with the fit. Alternatively, if possible, we can base the new style on an existing pattern block, where we know that customers are happy with the fit. Size chart measurements should be taken from the made-up sample and not the patterns, because those are the dimensions that we want the garment to finish at. Patterns often have built-in manufacturing allowances, and these may vary depending on the fabric’s or garment’s washing process.
There are issues about size charts that you will find the industry divided on: do we specify the full measurement (total circumference) or half measurement, sometimes referred to as the flat measurement (which is taken as we measure the garment flat on the table). These include bust, waist, hip, hem, bicep, and cuff measurements. Pattern cutters prefer working with full measurements, but factories and quality controllers prefer working with half measurements, as they don’t have to double the amount when measuring garments. Whichever method you decide to use, make sure it is clearly mentioned on the size chart.
The other issue is tolerances; now, this can be a tricky one! These are the measurement variations from the size chart that we are prepared to accept. Now, some companies do not indicate any tolerances, but that does not mean that they won’t accept any. It just means that they don’t want to advertise the fact to their suppliers. Other companies specify plus tolerances but not minus tolerances, their reasoning being that if there has to be variations, they better be slightly larger than smaller. Owing to the instability of fabrics and to the fact that sewing machinists cannot be 100% accurate all the time, manufacturers will want their customers to specify plus or minus tolerances; for example, if a bust grade is 5 cm (2″), they will ask for 2.5 cm (1″). Can we accept garments that are half a size larger or smaller? The answer is, sometimes, yes, it does depend very much on the style. For larger loose-fitting styles, this tolerance would be acceptable, but for close-fitted styles, no; the manufacturer should be instructed to control the manufacturing better at all stages of production and work to a smaller tolerance. As we are not working with rigid materials, we have to accept some tolerance, but this has to be agreed with the buyer and suppliers and may vary depending on the type of garment.
In garment spec sheet, each page should have a heading, to include a date, reference number, style, fabric, factory or customer and buyer, and page number. This will give a unique identity to each specification and each page of the specification. This is especially useful when amend any part of the specification. The factory will be able to immediately locate the page that needs to be replaced. It could be considered safer to reissue the whole specification sheet with a note of what has been changed and ask the manufacturer to sign a form, acknowledging that it has received the amended specification and that it understands the changes.
References:
- The Fundamentals of Quality Assurance in the Textile Industry by Stanley Bernard Brahams
- Textiles and Fashion: Materials, Design and Technology Edited by Rose Sinclair
- Apparel Merchandising by R. Rathinamoorthy and R. Surjit
- www.garmentsmerchandising.com/9-key-points-of-garment-specification-sheet/
- https://textilelearner.net/tech-pack-in-garment-industry/