What is Kapok Fiber?
Kapok or capok is a natural, cellulosic fiber. It is obtained from the seed hairs of kapok trees (Ceiba pentandra). Kapok is also called as silk cotton or java cotton. It is smooth, lightweight, unicellular, cylindrically shaped, hollow body, and very buoyant, and twist less fiber. But it quickly breaks down. Kapok fibers on its own are not suitable for spinning into yarn. Cause is very smooth, slippery and brittle. Therefore, fiber is difficult to spin into yarns.
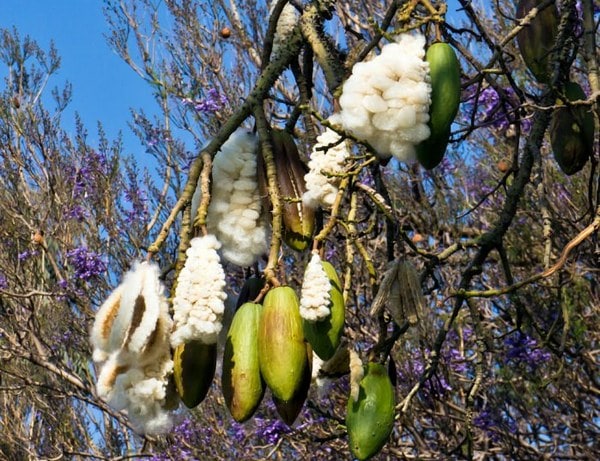
The specialty of the kapok fibre is, its yellowish color or light-brown with a silk-like luster. In contrast to the cotton fiber, the kapok fiber has single-celled plant hairs. This fiber is conventionally used as stuffing for insulation against sound and heat, and for bedding, life preservers, and other water safety equipment, sowing to its hollow air-filled lumen and high void content. Because of its excellent buoyancy. Due to have some unique features, kapok fiber-based materials have created area of opportunities in the various application fields.
We will be discussed below, everything of kapok fibre properties to applications.
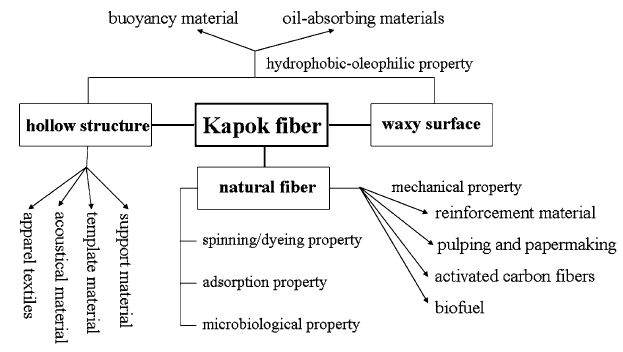
Structure of Kapok Fiber:
Kapok fiber are homogenous circular cross section with wide air-filled lumen. Air filled lumen has wall thickness about 1-2μm. As a result, its cell wall is thin and covered with a thick layer of wax. Kapok fibers are found transparent with characteristic air bubbles in the lumen by the microscope observation. The cross section of kapok fibers is oval to round.
Kapok Producing Countries:
- Nigeria,
- Mozambique,
- Tanzania,
- Sri Lanka,
- Indonesia,
- Thailand,
- Vietnam,
- Philippines,
- Brazil,
- Ecuador,
- Costa Rica,
- Peru, etc.
Processing of Kapok:
Kapok harvesting process requires a lot of manpower. Every step is done mostly by hand. The processing of kapok starts with:
Harvesting
↓
Reoving Hulls
↓
Drying
↓
Bailing
↓
Packing
All process are described briefly:
1. Harvesting:
The ripe unopened pods are normally harvested by knocking them off the tree. But it can also be cut from the tree or harvested when fall to the ground.
2. Removing hulls:
Kapok fiber is left in sunlight for drying of hulls. The fruits are hulled and seed and fibers are removed from the pods by hand.
3. Removing seeds:
The seeds lie loose in the floss and, with the help of some beating they fall to the bottom of the container where they are easily separated.
4. Drying:
Kapok fiber is dried under the sun for 3 -5 hours to complete drying.
5. Bailing and packing:
Kapok fibers are then packed in the form of bales and dispatched for further processing.
Properties of Kapok Fiber:
Component of Kapok:
- Cellulose: 64%
- Pentose: 23%.
- Lignin: 13%
Physical Properties of Kapok Fiber:
Component | Characteristics |
1. Appearance | Lustrous, yellowish brown and made of a mix of lignin and cellulose. |
2. Fineness | 0.4-0.7 denier. |
3. Elongation at break | 1.8-4.23. |
4. Tenacity | 1.4-1.74 gram/denier. |
5. Thermal behavior of kapok | Static immobile air held in the large lumen region of kapok makes a better heat retention. |
6. Absorbency | Excellent oil absorbency and retention capacity due to its waxy surface and large percent of lumen. |
7. Light weight | 8-10 times lighter than cotton by volume. |
8. Effect of Acids | Damaged by acid. |
9. Effect of Alkalis | Showed good resistance and doesn’t damaged by alkalis. |
10. Effect of Microorganisms | Because of lignin micro-organism shows no effect. |
Chemical Composition of Kapok:
Chemical component | Percentages (%) |
1. Moisture content | 11.23 |
2. Solubility | a) Cold water: 2.70 b) Hot water: 4.42 c) NaOH 1%: 30.20 |
3. Holocellulose | 83.73 |
4. α-cellulose | 38.09 |
5. Lignin | 14.10 |
6. Silica | 0.45 |
7. Ash | 1.05 |
8. Wax content | 2.34 |
Kapok fiber characteristics comparison with others:
Characteristics | Kapok | Cotton | Air |
1. Average linear density | 0.064tex | 0.12tex | — |
2. Average diameter | 20.5µm | 14µm | — |
3. Average length | 20mm | 48mm | — |
4. Moisture regain | 10% | 8~13% | — |
5. Specific heat | — | — | 1027W·s/kg·K |
6. Conductivity | — | — | 0.026 |
7. Mass density | — | — | 1.17kg/m3 |
8. Thickness | — | — | 1mm |
Advantages of Kapok Fiber:
- Light Weight.
- Hydrophobic and the good buoyancy effect.
- Thermal insulator.
- Bio degradable, etc.
Disadvantages of Kapok Fiber:
- The fibers are fragile and break easily.
- Irritant to lungs and needs extra care during work.
- Not suitable for weaving or spinning.
- Highly inflammable, etc.
End Uses of Kapok Fiber:
- Mattress or Pillow stuffing.
- Life-saving equipment.
- Yachts and boats furnishing, insulating materials in refrigeration systems.
- Construction of thermally insulated and sound proof covers and walls.
- Substitute of cotton in surgery.
- By products such as Kapok seed oil, and so on.
Special Applications of Kapok Fiber:
1. Apparel Textiles:
Once kapok fibre was considered unfit for textile fabrics. However, the weave-ability of kapok can be enhanced by blending with other fibers. Kapok fabric has met the basic requirements on apparel textiles, showing better performance than cotton fabric in some features such as: air permeability, durability, warmth retention, especially the warmth retention of plain-woven kapok fabric.
2. Acoustical Material:
Noise pollution is the excessive noise which borrow heavy damage and great stress on the activity and balance of human. Consequently, it is very important to develop economical and eco-friendly acoustical materials to control the noise pollution. Special structure of kapok is beneficial to the sound absorption. Due to kapok fiber has large lumen and thin cell walls, it increases the chance of friction between sound waves and fibers. Consequently, kapok fiber has excellent acoustical damping performance.
3. Oil-Absorbing Materials:
Over the production, storage, and transportation of oils are always possible risks of oil spillage. Oil spills often result in immediate and long-term environmental damage. To this minimize environmental issues some oil spill remediation products have been developed for the cleanup and recovery of oil spills. But this synthetic material will present serious environmental issues due to their non-biodegradable characteristics. Kapok fiber is a natural, inexpensive, hydrophobic–oleophilic agricultural product. It is considered to be a better alternative to the widely used synthetic materials. Kapok fibre exhibits high hydrophobic–oleophilic characteristics. This intrinsic nature makes kapok a high oil retentional fiber.
You may also like: Basics of Textile Fibers
4. Reinforcement Material:
Kapok fibers are renewable sources have attracted much attention in recent years. It has rich cellulose and cheap in price. As result, kapok have shown potential application as reinforcements to thermoset and thermoplastic polymer matrices.
5. Pulping and Papermaking:
Kapok fiber can be a quality pulp source for papermaking. The water repellency of the sheets can improveby mixing kapok pulp with the commercial pulps. It hasreceived special attentions in packaging paper requiring strength and water repellency. It can be said that kapok will be sustainable elements of paper making.
6. Kapok-Derived Biofuel:
Today, biofuels have attracted the most attention for its potential renewable characteristics. Kapok fibre have a potential resource of production second-generation bioethanol.
7. Other Applications:
Kapok fiber an abundant natural plant fiber. It has been used widely for various industrial fields. It is nonresistant to spark or flame. It can be used in production flame retardant fabric.
Conclusions and Future Perspective:
Kapok fiber has received increasing attention in recent years as an eco-friendly renewable material. However, the difficulty in spinning of kapok fiber remains. Especially such as the oil-absorbing materials, an overwhelming product for kapok fibre. The development of modern technologies based on kapok fiber will in future promote the further utilization of this natural fiber.
References:
- Biomass and Bioenergy Applications by Khalid Rehman Hakeem.
- https://www.slideshare.net/nornadiahsarbu/kapok
- https://link-springer-com-443.webvpn.jnu.edu.cn/chapter/10.1007%2F978-3-319-07578-5_13
- http://www.jwst.or.kr/past/xml_view.asp?a_key=3617586&n_key=4&v_key=46
Author of this Article:
Md. Mahedi Hasan
B.Sc. in Textile Engineering
Textile Engineering College, Noakhali.
Email: mh18.bd@gmail.com