What is Microfiber?
Fibers with thickness less than 0.3 dtex (denier) are termed as microfibers. It is twice as thin as the finest silk fiber and 100 times finer than a strand of human hair. Most microfibers are made from polyester or nylon, but some are rayon and acrylic. They can be used alone or blended with other natural or manufactured fibers. Microfibers find their use in air filters, dust wipes, etc., because of their high surface area as compared to normal fibers.
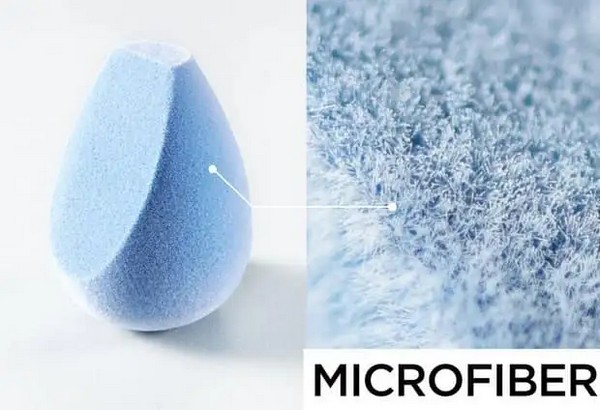
The growing demand to increase the fiber properties known to create new sophisticated application for textile materials have been the causes of the rapid growth of microfiber technology. Microfibers are half the diameter of a fine silk fiber, one-third the diameter of cotton, one-quarter the diameter of fine wool and one hundred times finer than human hair. In order to be classified as a microfiber, the fiber must be less than 1 dtex in width. Fabrics made from microfibers are generally light weight, resist wrinkling, have a luxurious drape and body, retain shape and resist pilling. They are also relatively strong and durable in relation to other fabrics of similar weight, and they are more breathable and more comfortable to wear.
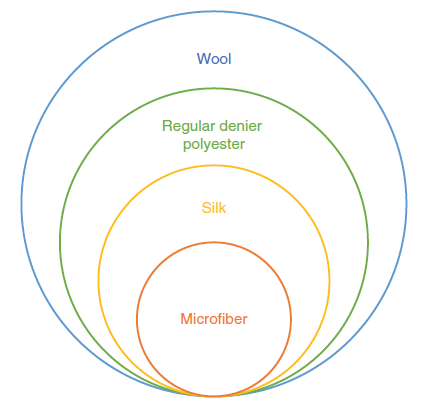
A microfiber is defined as a fiber (including staple fibers and filaments) of linear density approximately 1 dtex or less, and above 0.3 dtex. Even finer fibers are produced, of 0.3 dtex or less, but these are commonly referred to as super-microfibers.
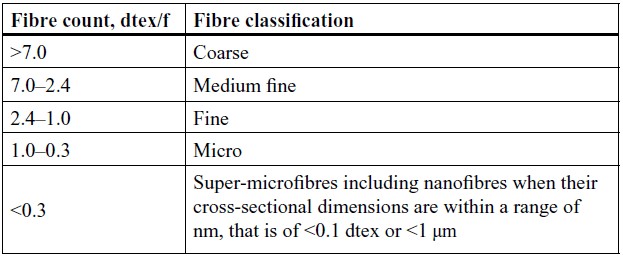
History of Microfibers:
Microfibers (MFs), developed in the 1990s, were one of the greatest achievements of the manufactured fibers’ industry. The introduction of microfibers started a new era of textile products. Microfibers are thinner than any other natural or manufactured fiber. While the first microfiber was made of polyester, today other fibers can also be produced in microfiber form, including nylon, acrylic, and some regenerated cellulosic fibers such as rayon and lyocell. Japanese fiber manufacturing companies introduced the first ‘micro-denier’ products during the 1970s. Then followed the developments in Europe during the 1980s, and since the 1990s American fiber manufacturers have been following suit. At present, polyester and nylon are generally used for manufacturing microfibers. However, ‘micro-denier’ versions of rayon and acrylic products are on the horizon.
For as long as microfiber technology has been around, ultra-microfiber technology has existed as well. These are fibers that are less than 0.3 dtex, and especially within the range of 0.1 dtex. Several different processes can be used to make these fibers, all involving the splitting of a larger fiber into many smaller ones.
General Properties of Microfibers:
Microfiber fabrics are comfortable due to their light weight and ability to wick away moisture. Since they resist wrinkles and keep their shape well, the fabrics take little care. They look good because of their luxurious, silk-like hand and drape. Since the fibers absorb dyes well, fabrics can have deep, rich colors. The major drawback of microfibers is heat sensitivity, so a very low temperature is needed to press fabrics. With so many positive qualities, however, microfiber use is growing rapidly. Here are some key properties of microfiber:
- Ultra-fine linear density (less than 0.1 dtex/f), finer than the most delicate silk.
- Extremely drapeable.
- Very soft, luxurious hand with a silken or suede touch.
- Washable and dry-cleanable.
- Shrink resistance.
- High strength.
- Insulates well against wind, rain and cold.
- Anti-microbial agents help to protect both family members and work staff from the dangers of the bacteria that cause odour and mildew.
- Microfiber is hypoallergenic, and so does not create problems for those suffering from allergies.
- Microfiber is non-electrostatic.
- Microfibers are super-absorbent, absorbing over 7 times their weight in water.
- Microfiber dries in one-third of the time of ordinary fibers.
- Microfibers are environmentally friendly.
Comparison between fibers of standard linear density and microfibers:
- The tenacity value of fine dpf POY spun is higher than that of normal dpf POY.
- The tenacity value of fine dpf acrylic spun is higher than that of normal dpf acrylic.
- The elongation-at-break value of fine dpf POY spun is lower than that of normal dpf POY.
- The Uster value of fine dpf yarn is slightly higher than that of normal dpf yarn.
- The draw force value of fine dpf yarn is higher than that of normal dpf yarn.
Comparison of the properties of polyester and acrylic microfibers with different linear densities is presented in Table-2.
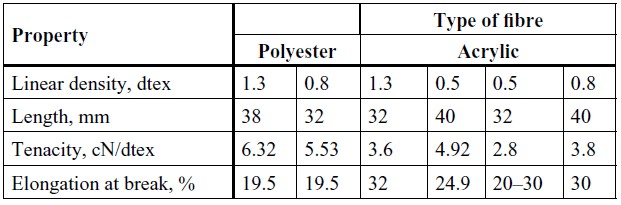
Production of Microfibers:
Microfibers are generally considered to be fibers with a linear density of less than 1.0 dtex. Although the technology for microfiber production has been available for many years now, strong demand for these fibers did not begin until the 1980s. The currently available micro fibers are different from ordinary fibers mainly in their dimensions, but have much lower property differences than the standard fibers. Toray was the first company in the world to introduce micro fibers, followed by Teijin, Hoechst, ICI, DuPont and others. Recently Toray has introduced an ultrafine polyester microfiber with a linear density of filament of about 0.05 dtex. This may be called the finest synthetic fiber so far produced commercially.
Different Methods of Microfiber Manufacturing:
There are various methods of producing microfibers, including modified conventional spinning. All three conventional spinning methods, namely, melt spinning; wet spinning and dry spinning can be employed to manufacture microfibers. For this method, carefully selected polymerization, polymer spinning and drawing conditions are required. Polyester, nylon and acrylic microfibers may be manufactured by this method. The extrusion spinnerets should contain many holes of very fine diameter, each of which will make one uninterrupted filament, in spite of complex thermal and rheological changes.
Dissolved type:
Microfibers of this type are manufactured from bi-component fibers with different types of polymers. Comparatively thick bi-component filaments containing different types of incompatible polymers are spun, and the fabric is made using them. When the fabric is treated chemically with solvent, one component is dissolved and removed, and the other component remains as the microfiber. Polyester and nylon microfibers can be made by this method.
Commercial production has been reported to use 20/80 ratios of soluble/ insoluble polymers to produce a bi-component filament of up to 2 dtex fineness and a final dissolved filament with linear density of about 0.50 dtex. The various combinations of soluble/insoluble polymers reported to form fibres successfully are polystyrene/polyamide and polystyrene/polyester.
Split type:
The microfibers of this type are obtained by physically or chemically treating the bi-component filaments containing two types of polymers and splitting them into different types of filaments. It is easier to split the segment in filament from itself than in the fabrics. Suitable polymer combinations for splittable bi-component filament spinning are polyamides/polyester and polyester/polyolefines.
Direct spun type:
This microfiber is directly manufactured by melt spinning. For this method, highly selected polymerization, polymer, spinning conditions and drawing conditions are required.
Special melt spinning dynamics should be considered for the production of low linear density polyester by the direct extrusion method. When polymers have similar dynamic viscosities at the given temperature, the polymer with the lower dynamic viscosity permits the spinning of finer fibers. This result has been attributed to the lower spin-line tension generated when spinning polymers with lower dynamic viscosity. It is postulated that the important parameter in the production of finer PET fiber is the spin-line tension level, which must be kept low in order to obtain finer fibers. The increase in takeup velocity, and the fiber line length between the spinner and the take-up device increase the spin-line stress level, and therefore the minimum fineness attainable increases.
Super-drawing technique:
In this technique, no molecular orientation is involved. Staple fiber with linear density less than 0.5 dtex can be produced with high drawing ratios. This technique is based on the principle that yarn can be stretched as much as 10–75 times much beyond their conventional draw ratios (3–6 times) if the drawing is carried out at a minimum crystallizing temperature and at special selected drawing conditions, including the temperature range and the type of heating the fiber.
Sheath-core spinning method:
In this method, two different polymers are mixed, melted and mix-annealed under specified conditions. The conjugate fiber comprising of a concentric circular sheath and a core is manufactured, and the sheath portion is removed to form ultra-fine fibers.
Some other methods of microfiber manufacturing:
- Flash-spinning method
- Solution flash-spinning
- Emulsion-spinning method
- Jet-spinning method
- Centrifugal-spinning method
- Turbulent forming method
- Conjugate-spinning method
Bi-component fibers:
Bi-component fibers are co-extruded with two different polymers in the cross-section. This allows the fiber to use the properties of both materials, and vastly expands the array of possible fiber performance characteristics.
Bi-component fibers are available in staple, filament and microfiber forms. Typical bi-component fiber types are presented in Figure-3.

(a) Sheath/core (b) Eccentric (c) Side-by-side (d) Pie wedge (e) Hollow (f) Islands/sea (g) Three islands
Specialty cross-sections:
A modified cross-section can provide added functionality, such as unique lustre or moisture transport. These cross-sections are available in staple, filament and microfiber forms, and in most cases, are also available as bi-component fibers. Typical microfibers with special cross-section shape, commonly used, are presented in Figure-4; many applications find especially the hollow fibers.
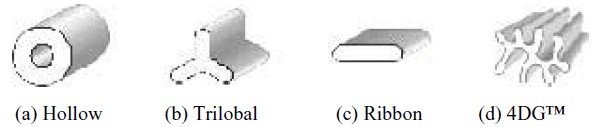
Uses of Microfiber:
Microfiber is a ultra-fine synthetic fiber. It has wide variety of applications across various industries. Microfibers are frequently used in cleaning cloths and towels for its high absorbency and quick-drying features. Generally it is used to make mats, knits, and weaves, for apparel, upholstery and industrial filters etc. Microfibers did not only make their debut in sportswear for their wicking abilities but also became a great candidate for rainwear. When microfibers are tightly woven, they prevent water droplets from penetrating the fabric weave. One of the first and best-known microfiber products is the artificial leather called Alcantara®.
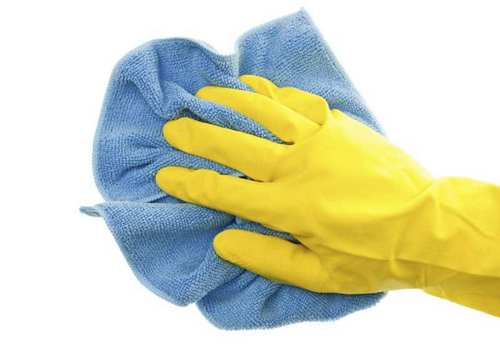
References:
- Clothing: Fashion, Fabrics and Construction, Fifth Edition by Jeanette Weber
- Handbook of Fiber Chemistry, Third Edition Edited by Menachem Lewin
- Textile Fiber Microscopy: A Practical Approach By Ivana Markova
- Handbook of Fibrous Materials Edited by Jinlian Hu, Bipin Kumar and Jing Lu
You may also like: