What is Ultrafine Fiber?
There has been no clear definition to the ultrafine fiber, but in the broad sense it is thought that the diameter of ultrafine fiber is less than that of silk (diameter 10 μm) which is the finest natural fiber as a standard. However, the diameter at which many features of ultrafine fibers can be recognized, e.g., special tactual sense (touch) and flexibility which are different from the conventional textile fibers, is less than 7 μm, and the features are particularly significant at the diameter less than 3 μm. Therefore sometimes, fibers with the diameter less than 3 μm are called as ultrafine fibers.
The definition of ultra-fine fiber has varied according to the convention employed. For instance, A micro-denier fiber is a fiber finer than 1.2 dtex for polyester and finer than 1.0 dtex for polyamide. Although a rather thick (1 denier or more) fiber is sometimes claimed as an ultrafine fiber commercially, an ultrafine fiber should preferably be specified as a fiber of less than 0.5 d. A fiber of less than 0.1 d is sometimes referred to as a super ultra-fine fiber. Ultra-fine fibers are classified into two types: (i) a continuous-filament type and (ii) a random (staple) type.
Table: Shows the diameters of some familiar fibers to grasp an image of fineness of ultrafine fibers.
Type of fibers | Circular approximated diameter (pm) |
Human hair | 50-60 |
Wool | 20-26 |
Polyester fiber for men’s shirt | 15 |
Silken thread | 12-20 |
Ultrafine fiber for suede-like artificial leather | 3 |
Ultrafine fiber for spectacles wiping cloth | 2 |
Super ultrafine fiber attained in laboratory | 0.1 |
Ultrafine fibers were produced by melt-blow spinning and flash spinning in the late 1950s. These fibers were not of the continuous filament type but were fine staple fibers of random length which found no application except for being processed into nonwoven sheets immediately after spinning. Ultra-fine fibers of a continuous-filament type have a relatively recent history.
Commercial microfibers produced using component melt spinning have diameters typically 0.5–5 μm and are often found in toweling and cleaning cloths, as they can pick up fine particles of dirt. Fibers smaller than 0.5 μm are intrinsically difficult to produce but have unique properties that make them attractive as functional units in membranes and scaffolds. Fibers less than 1 μm in diameter are termed submicron fibers and true nano fibers are fibers that have diameters less than 100 nm. Nanofibers are very fine and this influences the mechanical and reflective properties of the fabric. These fabrics can have a very fine pore size per weight of fabric, so have potential uses as selective filters and as breathable membranes.
Ultrafine fibers are extremely difficult to handle and at present are not suitable for processing into yarns or fabrics due to the limitations of manufacture. Electrospinning is the principle means of producing submicron fibers. However, this method is mostly used to produce flat nonwovens and fibrous membranes for technical applications. As this technology grows, it is likely that electrospun products will find increasing use in apparel and nontechnical applications. However, at present, it is too limited with regards to production speed and material format to be considered as an apparel design element.
Properties of Ultrafine Fiber:
Different ultrafine fibers are designed to provide the following characteristics:
- High filament density at the textile surface.
- Softness, flexibility and smoothness.
- Micro-pockets in fabrics.
- Large surface area per unit weight, and a characteristic interfacial property.
- Small radius of curvature (resulting in luster and characteristic colour)
- Large aspect ratio (the ratio of length to diameter) and easy entanglement.
- Good interpenetrating capacity in other materials.
- Fine, sharp edges.
- Quick stress relief.
- Low resistance to bending.
- Fine textile structure.
- Bio-singularity relative to living tissues and fluids.
Manufacturing Process for Ultrafine Fibers:
The simplest way to make ultrafine fibers is the direct spinning using spinneret with small holes. However, this method is applicable for the fibers up to 3 μm in diameter, and at present there are many problems in technology and manufacturing cost to make thinner fibers less than 3 μm by this method.
On the other hand, there is an alternative method. For the first a conjugate fiber which consists of two different kinds of polymers is produced. Then, woven or knitted fabric made from the conjugate fibers is processed to remove one polymer component or peel off both components of the conjugate fiber. There are two morphologies for the conjugate fibers, e.g., sea-island type and peeling and splitting type. As for the production method of the sea-island-type conjugate fibers, combined polymer flows where many island components, which will be finally the ultrafine fiber and are covered by sea component part, are bundled and pushed out as a filament. Then the sea component part was removed by dissolving in order to produce the ultrafine fibers. On the other hand, as for the peeling- and splitting-type conjugate fibers, two components are peeled off by chemical or mechanical treatment to produce the ultrafine fibers. Figure 1 shows the various types of ultrafine fibers.
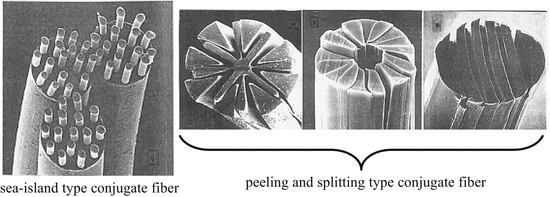
The largest advantage of the conjugate fiber technology is the complete avoidance of fiber twinning and yarn breakage in the processing stage of ultrafine fibers. That is, in the processing stage, the ultrafine fibers are still thick conjugate fibers and it is possible to handle them in the same way as other general fibers. After that at the stage when there is no possibility of problems in treating ultrafine fibers, the conjugate fibers are changed to ultrafine fibers by chemical and/or physical treatment.
Below 2 processes are used in ultrafine fiber manufacturing:
1. Continuous filament type:
Ultra-fine fiber of the continuous-filament type is now produced by a variety of methods including:
- Direct spinning (conventional extrusion).
- Conjugate spinning (extrusion of polymer components arranged alternately):
- Islands-in-a-sea type;
- Separation type or splitting type;
- Multi-layer type.
2. Random (staple) type:
Ultra-fine fibers of the random type are produced by:
- Melt-blowing or jet spinning.
- Flash-spinning.
- Polymer-blend spinning.
- Centrifugal spinning.
- Fibrillation or violent flexing.
- Turbulent flow-moulding
- Bursting and
- Other methods.
Uses / Application of Ultrafine Fiber:
The ultrafine fibers have some happenstance effects such as biocompatibility in addition to the original features which come from the geometrical fineness, e.g., pliability, flexibility, tactual sense (touch), luster, large specific surface area, and fillability (flatness on the fabric surface). Therefore, the commercialized technology to draw forth these features of the ultrafine fibers well is important, and thereby many high-quality products have been developed unique to the ultrafine fibers. The typical examples are the suede-like artificial leathers and the high-performance wiping clothes for optical lens, jewelies, cameras, mobile phone, and so on. Besides, nonwovens are made with ultra-fine filaments with a fineness of 0.5 denier or less.
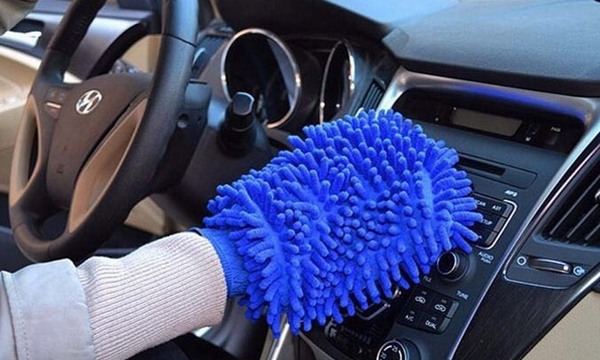
Although ultrafine fiber technology was developed first to produce artificial leather, its know-how was further developed to produce even finer fibers, which found an unexpected application as a wiping cloth for spectacles. The cloth can also be applied to clean car mirrors, remove oily dirt from windows, clean computers and electro-optics devices, polish and clean jewels and noble metals, polish crystals, clean showcases and frames, clean panels of audio/visual devices and optical discs, remove fingerprints on photos and films, and clean plastic products, etc. Here high-density fabric is variously processed into puffs, car cleaning drying gloves, quilts and even into tapes, according to the handling convenience needed. For example, high-density fabric tape is used as a built-in type cleaner for machines. High-density fabric is thus a new frontier fabric, which may find even wider applications.
Conclusion:
Ultra-fine fiber is not a speciality fiber but can be considered to be one of the fundamental fiber materials today. It is expected to open up new fields of fiber application. Ultrafine fiber spinning technology will be developed further towards its limits, and will be applied in other fields of technology.
References:
- Textile and Clothing Design Technology by Tom Cassidy & Parikshit Goswami
- High-Performance and Specialty Fibers: Concepts, Technology and Modern Applications of Man-Made Fibers for the Future by Springer
- Modern Textile Technology By J.B.Rattan
- New Fibers – 2nd Edition By Tatsuya Hongu and Glyn O. Phillips
- https://textilelearner.net/ultra-fine-fiber-types-characteristics-and-uses/
You may also like:
- Kevlar: A Fiber has changed the War Industry
- Ceramic Fiber: Properties, Production and Applications
- Properties, Manufacturing and Application of Fiberglass