Sampling plan for inspection:
The main objective of a sampling plan is to collect and how to collect a number of samples from a lot, which will be used for inspection. It is relevantly mentionable here that the expense and time for the inspection will be as high as the size of the samples.
There are three sampling plans in apparel industry for selection of sample quantity, inspection and decision making:
- Single sampling plan
- Double sampling plan and
- Multiple sampling plan
In apparel industry, single and double sampling plan are used mostly but multiple sampling plan is not used appreciably, so, single and double sampling plans have been discussed elaborately below:
Single sampling plan in apparel industry:
For inspection as per this plan, the lot size and the average% defective which will be accepted by buyers, these two points are required to know for determining the number of sample quantities to be collected. Lot size means the units of goods and
The average defective is also called the acceptable quality level (AQL). Average% defective or (AQL) = 2.5 is meant that defects up to 2.5% is acceptable. The average defective may be in various percentage (%) but in garments industry generally 2.5%, 4.0%, 6.5% and 10% these four levels are used based on the price and types of the garments. For determining the number of samples for any lot size and for taking decision against acceptance quality level, need to take help of Table No-S/1 and Table No-S/2. An example is given below for taking decision in single sampling plan.
You may also like: 4 Point System for Fabric Inspection with Example
Example-1:
Let, a lot size = 2000 pieces garments
Acceptable quality level = 4%
Need to determine the number of samples to be inspected for this lot and to determine that up to what number of defects will be accepted.
Need to select 1201-3200 group for lot size = 2000 in Table No-S/1. The code = K is marked against this group from the general inspection level II. It is mentionable here that generally for finding out code mark general inspection level-II is used.
Table N0-S/1:
Sample size code
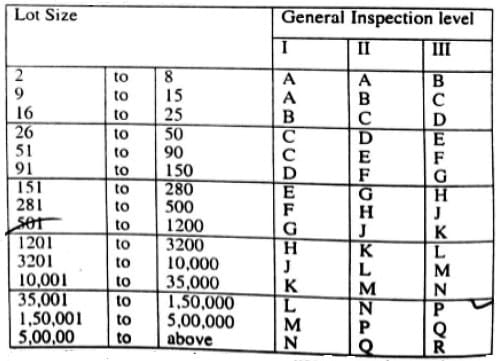
The number of samples = 125 is got against the code K from the Table No-S/2, and 10 and 11 these two numbers are got against the AQL = 4. The first number that is up to 10 defects will be accepted and if 11 or more than that defects are found, then that lot will be rejected.
Table No-S/2:
(For single sampling)
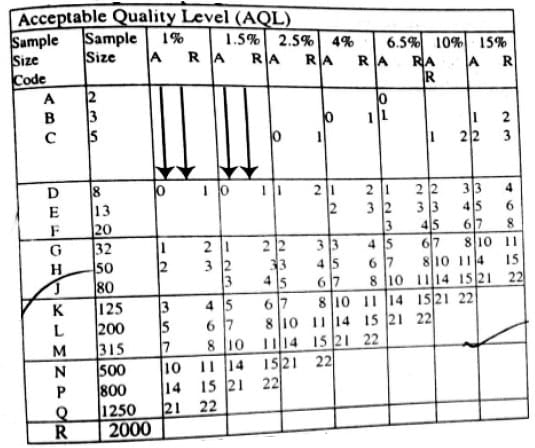
It is understood from this example that 125 pieces of samples has to be collected randomly from a lot size of 2000 pieces and after inspection of this 125 pieces, if the number of defective is 10 or below from it then that lot is accepted but if the number of defective is 11 or more than that then the lot will be rejected. It is mentionable here that if the AQL is lower or higher, then decision may be different. What type of decisions have to be taken for four levels (AQL) are shown below:
Example-2:
For a lot size of 9000 pieces of shirts, determine the sampling plan for each of the acceptance quality level (AQL) of 2.5%, 4.0%, 6.5% and 10.0%.
Got the sample code = L against the group of 3201-10000 for 9000 pieces from the general inspection level II of the Table No-S/1.
The number of samples = 200 is got against the code L from the Table No-S/2 and the decision of acceptance or rejection for four levels of AQL are given below:
Double sampling plan:
In this system, if required two times samples are collected and inspected. How the above mentioned examples are to be solved have been described below:
Example-3:
Lot size = 2000 pieces
Acceptable quality level = 4%
For this example, sample code K is got from the Table No-S/1. From the Table No-S/3, first 80 pieces of samples have to be taken against the sample code K and after inspection of these 80 pieces, if the defective samples are 5 or below 5 then the lot will be accepted. But if the defective samples are 9 or above, then the lot will be rejected. If the number of defective samples are 6, 7 or 8, then again 80 pieces of samples have to be taken for second time and re-inspection will be done. After second inspection if the number of the total defective samples (that means the first and second times together) is 12 or less than that then the lot of 2000 pieces has to be accepted. But if the number of defective samples is 13 or more than that then the lot will be rejected.
Table No-S/3:
(For double sampling)
Note: A = Acceptable defects, R = Rejected defects
Example-4:
Lot size = 9000
Acceptable quality level = 4%
For this example, sample code = L is got from the Table No-S/1. From the Table No-S/3, against the sample code = L, in the same way of example-3:
Accept | Reject | |
First sample-125 | 7 | 11 |
2nd sample-125 | 18 | 19 |
From the above discussions and examples on acceptable sampling plan, it is evident that in single sampling plan, the decision of lot acceptance or rejection is taken by collecting samples and doing inspection only once. But in double sampling plan, there is possibility of making decision first time by taking comparatively minimum numbers of samples. But if the decision cannot be made by first time taking samples and doing inspection, then second time samples are collected and inspection is conducted and the final decision about the lot is taken. If the second time sampling taking and doing inspection are required, then in double sampling plan, comparatively more expense and time are required than the single sampling plan.