Cotton processing consists of two basic processes namely, weaving and finishing. Most of the weaving operations are carried out under dry conditions, except slashing. Slashing or sizing is the process in which certain natural or synthetic compounds are applied to yarns to bind the fibers together and stiffen the yarn to provide abrasion resistance during weaving. Finishing operations are mostly wet processes and they include desizing (removal of the added size compounds), scouring/kier boiling, bleaching, mercerizing, dyeing/printing and final finishing. Wet processing in textile industry is one of the most important part of textile processing. In this article, I will discuss all above stages of wet processing in textile industry and it is for the cotton materials.
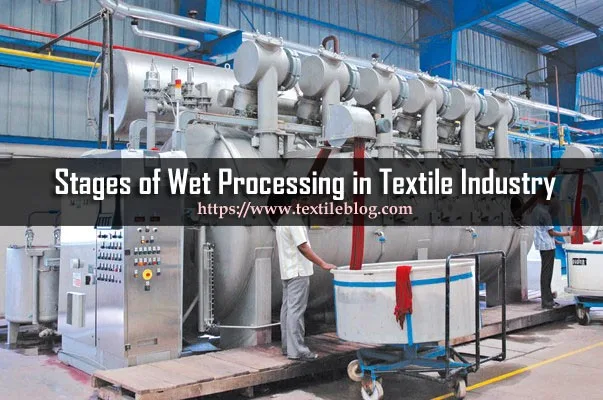
Stages of Wet Processing in Textile Industry
A. Sizing/Slashing:
It is the process by which warp thread is sized with starch (or other synthetic sizing materials) to give necessary tensile strength and smoothness required for weaving. Starch is the traditional sizing agent exclusively used for cotton fabrics. It is the cheapest and effective sizing agent. Native starch and modified starches are extensively used for sizing hitherto. However the trend is now changing and starches are slowly replaced by synthetic sizes. These synthetic sizes provide enhanced performance and can be easily removed by desizing.
The important sizing agents used for cotton sizing are polyvinyl alcohol (PVA) and carboxy methyl cellulose (CMC). (Carboxy methyl cellulose has twin advatages: (i) warps sized with CMC can be woven at lower humidities, and (ii) when CMC is used for sizing, desizing becomes much easier as the CMC film readily dissolves in water). The other sizing compounds, namely, gelatin, oil, polystyrene, polyacrylates (of sodium and ammonium salts), and polyacetates are employed for sizing synthetics. Among these sizes, polyacrylates are exclusively used for sizing nylon and polyester. They are very soluble in water and hence can be removed easily from the fabric.
B. Desizing:
It is a process employed to remove the sizing materials present in the greige cloth to make it suitable for further processing. If the sizes are present, they may hinder dyeing, printing and finishing processes. The methods and chemicals used for desizing depend on the type of sizing agent used. If starch is used as the sizing agent, the following two methods are employed for its removal. In these two methods, starch molecule is broken down and converted to more soluble materials and thus its removal is facilitated.
(i) Desizing with acid:
The greige cloth is treated with dilute sulfuric acid (0.5%) at room temperature for a period of 4 to 12 hours and then washed well.
(ii) Desizing with enzymes:
When modified starch is employed for sizing, desizing with enzyme is preferable. In this method, the cloth is steeped in baths containing enzymes and kept for 4 to 8 hours at 55 to 800C. The enzymes hydrolyse starch and converts it to readily soluble sugars. Then the clothes are subjected to mild acid treatment and rinsed well with water.
(ii) Desizing with Peroxide:
In recent times, peroxide is also employed for desizing. Peroxide fully degrades starch to CO and HO. However, this method is very expensive. If polyvinyl alcohol (PVA) or carboxy methyl cellulose (CMC) is used for sizing, they are removed with a detergent/water solution as they are readily soluble in water. Polyvinyl alcohol can be easily removed if washing is carried out at higher temperatures (near boiling point). PVA can also be recovered by applying nano-filtration or ultra filtration. The recovered PVA can be reused.
C. Scouring:
Scouring is an important operation by which natural impurities (greases, waxes, fats etc.,) and acquired impurities from the fabric are removed. Scouring also renders the cloth whiter and makes it more absorbent for subsequent bleaching and dyeing. There are two types of scouring: i) Continuous scouring and ii) Kier boiling. In recent times, continuous scouring is gaining prominence due to requirements of less space and time. It is also reported that good results are obtained in this technique with the reduced consumption of chemicals.
(i) Continuous Scouring:
In this method of scouring, desized fabric is passed through a caustic solution (3 to 6% caustic soda, surfactants and sodium phosphate) and after saturation, passed on to J box where the fabric is heated with live steam at a temperature of 1000C for 1 hour. After scouring, the fabric is rinsed well with water to remove the excess chemicals.
(ii) Kier Boiling:
Fabrics are heated under pressure using steam in steel/stainless steel pressure vessels (kiers) of 2 to 3m. dia and 3 to 4m. height. The kiering liquor is an alkaline solution containing caustic soda (1 to 3% on fabric wt) (major component), soda ash, sodium silicate and sodium peroxide with small amounts of detergents. The boiling is carried out for several hours (2 to 12 hrs). Then the fabric is rinsed well with water. Rinsing is continued until no brown color remains in the
D. Bleaching:
Bleaching is an essential finishing process used to remove natural coloring materials and to render the clothes white. In developing countries, sodium hypochlorite or chlorine is used for bleaching cotton textiles. Bleaching is usually followed by washing with fresh water and then by scouring (treatment with sodium bisulfite) to remove traces of alkali and chlorine.
In developed countries, hydrogen peroxide is the common bleaching agent. It is an effective bleaching agent, safer chemical and easier to handle. In addition to cotton, some finer fabrics are also bleached using hydrogen peroxide or sodium peroxide (Hydrogen peroxide is generally used for bleaching in the continuous processes). Peroxide bleaching is carried out during kiering or immediately after kiering. Caustic soda, sulfuric acid and certain soluble oils are used as adjuncts in peroxide bleaching. Needless to say that optical brighteners are also employed in bleaching.
Over the last few years, hypochlorite is being replaced by environmentally safe bleaching agents. One among such bleaching agents is peracetic acid (CH3COOOH). It provides higher brightness to fabric with less fiber damage. It decomposes to acetic acid which is easily biodegradable rendering the treatment much simpler.
E. Mercerizing:
Mercerization is a process applied to cotton fabrics only. This process causes physical and chemical changes within fiber and gives lustre, strength, dye affinity, smoothness and abrasion resistance to fabrics. The mercerized fabrics can easily be dyed. Most of the clothes are mercerized prior to dyeing, but rough varieties are not mercerized and after bleaching, they are sent directly for dyeing/printing without mercerizing.
Mercerization involves treatment of the bleached clothes with cold caustic solution (10% to 30% w/v) containing a penetrant for a specified period (1 to 3 minutes) followed by thorough washing with water several times. Traces of alkali adhering are removed by treatment with a dilute solution of acid followed by rinsing with water. The caustic soda dragged out by the cloth is usually recovered and reused for mercerization itself or for scouring.
F. Dyeing/Printing:
The fabric after bleaching may either be dyed or printed. It is the most important stage of wet processing in textile industry. Dyeing is the process by which the desired color is imparted to the fabric/yarn/fiber. Dyeing/printing makes the fabric more colorful and attractive. Dyeing and printing are the most complex of the wet processes and include hundreds of dyes and auxiliary chemicals such as mordants, salt (sodium chloride and sodium sulfate) and other fixing agents, acids, alkalis etc., In most of the mills, fabric is dyed, while in some of the mills, yarn itself is dyed after scouring and bleaching. In some other units, fiber is dyed which is termed as “Stock dyeing”.
References:
- Treatment of Textile Processing Effluents by N.Manivasakam
- Textile Dyeing Edited by Peter J. Hauser
- https://textilelearner.net/flow-chart-of-textile-wet-processing/