High-Performance Fibers:
High performance fibers are driven by special technical functions that require specific physical properties unique to these fibers. They usually have very high levels of at least one of the following properties: tensile strength, operating temperature, limiting oxygen index and chemical resistance.
High-performance fibers represent a special category of fibers that is primarily made for technical products, but it can be used for some traditional fibrous products (e.g., some apparel support, upholstery, and floor coverings). High-performance fibers are regarded as more superior to conventional fibers, driven by special technical function marked by their exceptional mechanical and physical performances. Many of the high-performance fibers find their own niche where they have an advantage over the others. High-performance fibers are mainly in use for technical textiles, such as ropes and belts, for reinforcement of composites in protective garment applications.
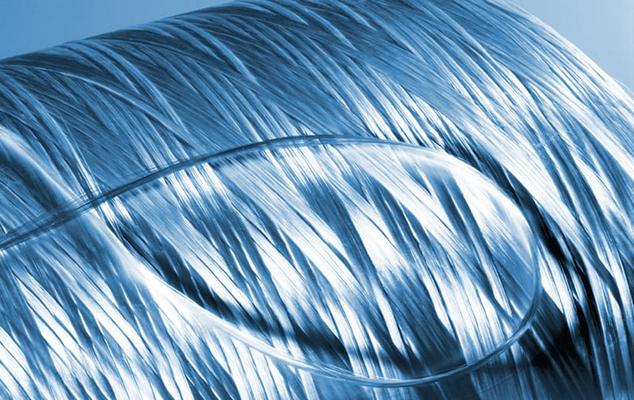
From a design viewpoint, high-performance fibers provide additional design options in many products. They can be used in many fields from ground transportation to aerospace and from biotechnology to computer and communication applications. The key criteria of high-performance fibers are very high strength, exceptionally high-temperature resistance, and unique geometrical characteristics (surface morphology and cross-sectional shapes). These criteria have been a result of major advances in polymer and fiber technology.
High performance textile materials having exceptional mechanical properties as well as fire‐resistant and chemical‐resistant properties are available in the form of fiber, film, membrane, and liquid and are frequently used in protective clothing. The high performance fibers are made from a wide source including organic polymers and inorganic materials such as ceramic fibers, carbon fiber, and stainless steel and aluminium fibers. High performance polymeric fibers having exceptional mechanical properties, fire‐resistant properties, chemical‐resistant properties and frequently being used in protective clothing.
List of High-Performance Fibers:
- Aramid fiber
- Gel-spun polyethylene fibers
- Carbon fiber (CF)
- Metallic / Metal fibers
- Glass fiber
- Ceramic fibers
- Melamine fiber
- Polyimide fiber
- Polybenzimidazole fiber
- Basalt fiber
- Polyphenylenebenzobisoxazole
- Polysulfonamide fiber
- Boron fibers
- Aromatic polyester fiber
- Optical fibers
- High polyketone fiber
- Polyphenylene sulphide fiber
- Fluoropolymer (polytetrafluoroethylene)
- HDPE
- Chemically resistant fibers
- Thermally resistant fibers
High-performance fibers and their applications are described below:
Aramid fibers:
Aramid fibers are polyamides, where each amide group is formed by the reaction of an amino group of one molecule with a carboxyl group of another. However, the presence of aromatic rings makes them more stable than with the linear arrangements of atoms. This provides great strength and heat stability. Two of the traditional aramid fibers are Kevlar, a high-strength fiber, and Nomex, a heat-resistant fiber.
Types of Aramid Fibers:
There are two main types of aramid fibers.
- Meta-aramid
- Para-aramid
1. Meta-aramid: Nomex
Of the many fibers that exist, the best known of the aramid family are meta-aramid (m-aramid) fibers due to their combination of heat-resistant and strength. Meta-aramid fibers do not ignite, melt, or drip, making them unique in the flame-resistant market and a widely used fiber for protection in hostile environments. The best known of the meta-aramid is Nomex. Nomex is the registered brand name of a flame-retardant meta-aramid material.
This m-aramid or poly(m-phenylene isophthalamide) was first discovered by DuPont in the 1970s. Nomex sheet is a calendered paper commonly used for electrical insulation applications such as circuit boards and transformer cores and fireproof honeycomb structures where it is saturated with a phenolic resin. These honeycomb structures and mylar-nomex laminates are used extensively in aircraft construction. In addition, both the firefighting and vehicle racing industries use Nomex fibers to design clothing and equipment that can withstand intense heat.
Principal market for meta-aramids is in heat-resistant materials. Other application of these fibers include automotive, thermal insulation, thermal space, safety, and protection.
2. Para-aramid: Kevlar
Para-aramid (p-aramid) fibers have high tenacity, high tensile modulus, and high-heat resistant and thermal properties, due to their highly orientated rigid molecular structure. Kevlar is commonly called para-aramid or poly(p-phenylene terephthalamide). It belongs to a class of materials known as liquid crystalline polymers. In contrast with conventional flexible polymers, which in solution, they can easily bend and entangle (forming random coils), Kevlar polymers are very rigid and rodlike. As a result, in solution, they can aggregate to form ordered domains in parallel arrays.
Paraaramids can be used in composite application, aircraft, and lorries, and in ballistic protection such as bullet vest, helmet, and vehicle amour. All aramid fibers are prone to photo-degradation and need protection against sun rays when outdoors.
Gel-spun polyethylene fibers:
This category of fibers represents ultrastrong and high-modulus material derived from the simple and flexible polyethylene molecule. They are commonly called high performance polyethylene (HPPE) fibers, high-modulus polyethylene (HMPE) fibers, or sometimes extended chain polyethylene (ECPE) fibers. The molecular structure of this category of fibers is different from that of para-aramid fibers in that it is not a rodlike structure, which needs to be oriented in one direction to form a strong fiber. Instead, polyethylene has much longer and flexible molecules that, by physical treatments, can be forced to assume straight (extended) conformation and orientation along the fiber axis. The most common types of high-performance polyethylene fibers are Dyneema and Spectra.
Dyneema was developed in Japan. Dyneema was invented in 1963 but made commercially available by DSM in 1990 and was reputed to be the world’s strongest fiber, 15 times stronger than steel on a weight for weight basis. It is highly flexible and offers high protection against mechanical hazards.
Properties of Gel-spun polyethylene fiber:
Some properties of this fiber are:
- High strength to low ratio
- Low specific gravity—it will float on water
- Excellent chemical resistance
- Highly UV resistant
- Moisture resistant
- Highly durable
End uses for this fiber are: automotive, glass, paper, food, household equipment, steel, construction, and emergency services industries.
Carbon fibers:
Carbon fibers are extremely resistant to high temperatures, remain stable up to 800°C in air. They may also be considered as flame resistant fibers as they rarely burn in flame. Hence, their textiles are even applied as filters of molten iron. There are many varieties of carbon fiber based on modulus, tensile strength, and heat setting. Carbon fibers contain at least 90% carbon by weight. They are commonly derived from several organic polymers, such as rayon and polyacrylonitrile (PAN). The first commercial carbon fiber was rayon based introduced in 1959. This fiber found its applications primarily in military products. Graphite fibers can be considered as derivatives of carbon fibers.
The major application of carbon fibers is reinforcement in polymer, metal, and ceramic composites. End uses of these fibers include reinforcement and heat-resistant materials, for example, aircraft and aerospace, marine, sports, and recreational equipment, surgical appliances to include heart valves and hip replacements.
Properties of carbon fiber:
The following list provides the unique properties of this fiber:
- Nonflammable and nonmelting characteristics
- Extremely resistance to high temperatures (melting point, 4000°C)
- Flame-resistant
Metallic / Metal fibers:
Metal fibers are on the market as filament yarns, rovings, mats, and wovens, and their common merit is their high temperature resistance. Except for steel, metal fibers of aluminum, magnesium, copper, molybdenum, and tungsten are made for particular applications. Metal fibers, such as Angelina Aluminum Metal Fibers (produced by Meadowbrook Inventions, Inc.), use prepared recycled aluminum, and it shows good heat resistance and dye bath tolerance, and protective qualities including thermal regulation, UV and electromagnetic protection, antibacterial, antistress, and antistatic properties. Most metal fibers show a coarse surface.
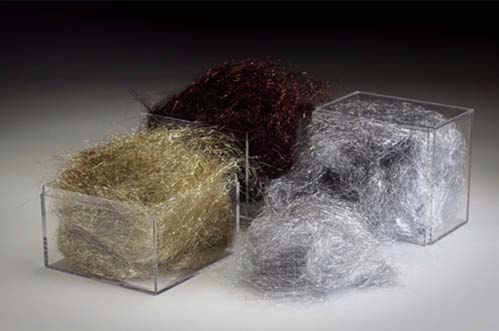
Another metal fiber produced by the company is Angelina Copper Metal Fiber; this kind of fiber can be used in the high-temperature application field. More than that, its antibacterial properties, antiinflammatory, antiarthritic, antistatic, pharmacological health benefits, and solvent resistance expand the application fields, including bedding and home furnishings, antibacterial textiles, antistatic carpets, filtration, and decorative applications.
Metallic fibers of silver and gold have been used for millennia to decorate fabrics. Today, metallic fibers serve functional and decorative purposes. These fibers are formed by drawing metal wires through successively finer dies to achieve the desired diameter. Although gold and silver are the easiest to draw, modern methods have allowed the manufacture of steel, tantalum, and zirconium fibers. Because they are electrical conductors, metal fibers have been blended into fabrics to reduce the tendency to develop static electrical charges.
Glass fibers:
Glass fiber is the oldest, and most familiar, high-performance fiber. Glass is an inorganic fiber, which is neither orientated nor crystalline. It is considered one of the first man-made fibers. This fiber is widely used for insulation and reinforcement materials. These fibers generally display high tensile strength at a low elongation and very low density. The fibers have good thermal properties, making them ideal for insulation and are also by nature incombustible as well as not releasing any vapors or poisonous materials when exposed to heat. They are also resistant to oils, fats, and solutions and display a good resistance to acids and alkalization.
Properties of glass fiber:
The following list of properties applies to this fiber:
- Excellent strength to weight ratio
- Excellent elastic recovery
- Good thermal properties
- Excellent resistance to sunlight
- Good resistance to acids—can be attacked by some forms of acid such as concentrated hydrofluoric and sulfuric acid, and also hot phosphoric acids.
- Highly resistance to most chemicals in general use
- Highly resistance to organic solvents
- Excellent acoustic properties
End uses for this fiber include mats, thermal insulation, electrical insulation, sound insulation, and reinforcement of various materials—tent poles, sound absorption, heat, and corrosion-resistant fabrics. Other uses are high-strength fabrics, pole vault poles, arrows, bows, and Irish step dance shoes.
Ceramic fibers:
Ceramics are non-metallic inorganic materials consisting of metallic and non-metallic elements. A wide range of materials composed of clay minerals, cement and glass are included in this classification. Ceramic materials are often prepared through a burning or sintering process. Therefore they are more resistant to high temperatures and harsh environments in comparison to metals and organic materials. In addition, ceramics are good insulators for both electricity and heat.
Ceramic fibers are categorized into non-oxide fibers and oxide fibers. Silicon carbide and alumina are the most commonly used non-oxide and oxide ceramic fibers, respectively. Boron fibers and silicon fibers are normally classified as ceramic fibers even though boron and silicon are the metalloid elements. Short fibers, long fibers and continuous fibers of ceramics are available in the market. Continuous ceramic fibers are produced mainly through either the melt-spinning or dry-spinning processes.
Melamine: Basofil (BASF)
Basofil recently entered the high-temperature fiber market. It’s the newest fiber to be fully commercialized. Based on melamine chemistry, Basofil offers a high operating temperature and a high Limiting Oxygen Index, and typically targets the hot-gas filtration and safety and protective apparel markets. Because of its variable denier and staple length, low tensile strength and difficulty in processing, Basofil is generally blended with stronger fibers such as aramids. It is more often used in needled products, or yarns made from wrapped spinning techniques.
Polyimide fiber:
Polyimide fiber is made from an aromatic heterocyclic polymer, and P84 is the brand name of the polyimides manufactured by Evonik Fibers with a trilobal fiber cross section. P84 is a fully imidized polyimide derived from aromatic dianhydrides and aromatic diisocyanates and has a glass transition temperature of 315ºC. The fibers start to carbonize at temperatures beyond 370ºC. Due to the aromatic structure, the polymer and fibers are inherently nonflammable. An LOI of 38% can be measured. P84 can be used for temperatures up to 260ºC, depending on the environment.
Due to its outstanding chemical and thermal stability and physical properties, P84 fibers can be used for a variety of applications, ranging from filter media for high temperature filtration, protective clothing, and sealing materials for spacecraft to various high-temperature applications, such as thermal insulation.
Polybenzimidazole – PBI: PBI (Celanese)
Polybenzimidazole is an organic fiber with excellent thermal resistant properties and a good hand. PBI does not burn in air and does not melt or drip. High Limiting Oxygen Index (LOI) coupled with good chemical resistance and good moisture regain make PBI an excellent fiber for fire-blocking end uses, such as safety and protective clothing and flame retardant fabrics.
Its physical properties are relatively low, but PBI processes on most types of textile equipment. It blends well with other materials such as carbon and aramid fibers, most often for performance and cost reasons. PBI has had significant success in the firemen’s apparel market where, blended in a 60-40 para-aramid-PBI mixture, it has become the standard “premium” material. PBI’s characteristic gold colour blends well with other materials for a pleasing appearance.
Basalt fiber:
Basalt fiber is composed of the minerals plagioclase, pyroxene, and olivine. It is similar to carbon fiber (CF) and glass fiber, having better physicomechanical properties than fiberglass, but is significantly cheaper than CF.
Polyphenylenebenzobisoxazole — PBO: Zylon (Toyobo)
PBO is another new entrant to the high-performance organic fibers market. Toyobo’s Zylon is the only PBO fiber in production. PBO has outstanding thermal properties and almost twice the tensile strength of conventional para-aramid fibers. Its high modulus makes it an excellent candidate for reinforcement of composites. Its high LOI gives PBO more than twice the flame retardant properties of metaaramid fibers.
Polysulfonamide fiber:
Polysulfonamide (PSA) fiber is a special high-performance fiber developed in China. It is a new FR fiber with excellent heat resistance, thermal stability and thermal oxidation, high volume specific resistance and initial modulus, instability of crimp, and low friction coefficient.
Boron fibers:
Generally, boron fibers are made by means of boron vapor condensing on some carrier materials, such as of tungsten wires, glass, graphite, aluminum, and molybdenum, and the typical fiber diameter with tungsten wires as carrier materials is around 12 mm. Boron fibers are preferable to make some composites.
Aromatic polyester fiber:
Like aramid, aromatic polyester fibers are highly crystalline aromatic polyester fibers, in which lots of the ester linkages (_CO_OeRe) are attached directly to aromatic rings. Vectran is a polyester-based high-performance Liquide Crystal Polymer (LCP) produced by Ticona. Its modulus is similar to Kevlar 29, but it has less strength loss. Vectran fiber shows a 0.02% creep at 30% of max load after 10,000 h, high chemical and abrasion resistance and high tensile strength. The UV endurance of Vectran is inferior to PET and PEN, but has better exposure degradation than aramids.
Aromatic polyester fibers are used in yacht ropes, sailcloth, bow strings, bicycle frames, catheters and control cables in surgical devices. These applications reflect the fibers’ high abrasion resistance, cut resistance and impact resistance, in addition to their high strength.
Aromatic polyamide fiber:
Aromatic polyamide fiber are highly crystalline fibers in which at least 85% of the amide linkages (_COeNH_) are attached directly to two aromatic rings, and have the lowest density and the highest tensile strength-to-weight ratio among the current high-performance fibers. Aromatic polyamide fiber shows a negative coefficient of thermal expansion in the longitudinal direction, which is used in designing low thermal expansion composites. The major disadvantages of aromatic polyamide fiber are their weather resistance, low compressive strengths, and difficulty in cutting or machining in composites.
Optical fibers:
Optical fibers are classified into three groups according to the types of core material, quartz, multi-component and plastic optical fibers (POF). The quartz optical fiber is used for long distance optical communication including public trunk lines. The multi-component optical fiber is used for middle-distance communication, of 1-2 km, including local area networks (LAN) in plants and fiberscopes. The glass optical fiber has shortcomings because it is expensive, brittle and hard to process. Advantages of plastic optical fiber (POF) are that it is inexpensive, flexible, light and easy to process, though the transmission loss is higher than in glass optical fiber.
The material of both the core and sheath of the plastic optical fiber require high transparency. Generally, Polymethylmethacrylate (PMMA) and Polycarbonate (PC) are used as the core material. Since the refractive index of the sheath material should be lower than that of the core material, fluoroplastics including polyvinylidene fluoride, Teflon FEP, Teflon AF, fluorinated methacrylate and fluorinated polycarbonate are used as the sheath material.
High polyketone fiber:
Polyketone, produced by Asahi Kasei, is seen as a new high-strength fiber similar to aramid fiber, but the price is lower than aramid. This fiber has a molecular structure, which includes carbon monoxide and is also composed of ethylene. Thus, it contains only carbon, oxygen, and hydrogen, which need a low manufacturing cost compared to other high-strength fiber.
Polyphenylene sulfide fiber:
PPS is an organic polymer consisting of aromatic rings linked with sulfides. It is another kind of high-performance fiber which offers superb heat resistance, chemical resistance, hydrolysis resistance, flame retardance, and so on. PPS fiber can be used in filter for coal boilers, paper making felts, electrical insulation, specialty membranes, gaskets, and packings.
TORCON is a product of PPS made by Toray. Because of its high melt temperature (around 285ºC), PPS can continuously be used around 190ºC. It is also resistant to hydrolysis at high temperatures to acid, alkaline, organic solvents, which is better than other high-modulus fibers. The crystallinity of PPS fiber varies from 50% to 65% with the processing condition. Triangle cross-section PPS fibers are produced and can be used for high-efficiency filtration.
References:
- High Performance Apparel: Materials, Development and Applications Edited by John McLoughlin and Tasneem Sabir
- Engineering of High-Performance Textiles Edited by Menghe Miao and John H. Xin
- Structure and Properties of High-Performance Fibers Edited by Gajanan Bhat
- High Performance Technical Textiles Edited by Roshan Paul
- Physical Properties of Textile Fibres (Fourth edition) by W. E. Morton and J. W. S. Hearle
You may also like:
- Properties, Manufacturing and Application of Fiberglass
- Ceramic Fiber: Properties, Production and Applications
- Optical Fiber: Definition, Properties and Uses