Textile fibers are an integral component which provides to human, comfort, and sustainability. The human desire for better garment and apparel has resulted in the development of the textile manufacturing process. Natural textile fibers meet the desire for comfort and aesthetic trends for human consumption. But, the advancement of science, introduced several man-made fibers for conventional textile products. The textile manufacturing processes in the global textile industry are producing textile yarn, fiber, fabric, and finished products including apparel. The global textile industry associated with apparel and non-apparel products by the textile manufacturing process.
Textile Manufacturing Processes:
Textile industry encompasses variety of manufacturing processes that are adding value in the fiber. These processes may range over the yarn making through the garment stitching, fabric embossing, and all other composite production.
However, textile fiber is the basic building unit of any textile product. That’s why, the textile manufacturing processes can clearly be classified as the conventional and technical textiles. The conventional textile manufacturing process had a long history of converting natural fiber into useful textile products including fabrics, home textiles, and apparels. Recently technical textile through the utilization of special finishing effects by the synthetic man-made fiber and semi-synthetic fiber manufacturing processes which is diversified with the utilization of monomer, chemical agent, and catalyst resulting in the formation of fiber or yarn.
The modern research and innovation in textile manufacturing processes introduced us to variety in raw materials and manufacturing processes. Hence, manufacturing process have controlled to ensure product quality which is consumer desired. All the processing stages in textile manufacturing processes from fiber production to finished fabric are monitoring and controlling in process control and evaluation.The fabric production is included with knitting, weaving, non-weaving, and subsequent coloration and finishing and apparel manufacturing processes.
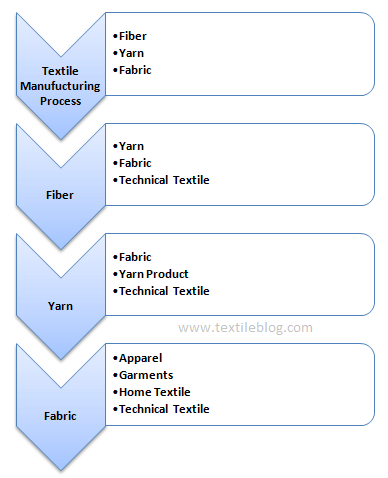
Types of Textile Manufacturing Processes:
Textile industry may be classified in several ways depending on the production processes, the obtained final products achieved and so on. In case of textile fabrics, the process starts with the gathering of natural fibers or man-made synthetic production. Then, after spinning process, continues with the processing into textile flat structures, fabrics, in the form of woven fabrics, knit fabric, nonwovens fabric, etc. The fabrics are treated in finishing processes, including dyeing and printing processes, coating, mechanical finishing. These processes will provide new properties to the fabric before the next stage: “the clothing stage”.
Process flow chart of textile manufacturing process
Yarn Manufacturing
(Spinning)
↓
Fabric Manufacturing
(Weaving)
↓
Wet Processing
(Dyeing +Printing+ Finishing)
↓
Apparel Manufacturing
(Cutting+Sewing)
1. Yarn Manufacturing:
Traditionally, yarn manufacturing comprises a lot of processes involved in converting the fiber into yarn. The natural fibers obtained from natural plant and animal sources. Its produced with natural impurities which were removed from the yarn in subsequent pre-treatment processes.
Cotton may the natural fiber that has rooted yarn manufacturing from fiber bale opening. These processes are followed by a series of continuous operations such as: blending, mixing, cleaning, carding, drawing, roving,and spinning, and so on. Yarn manufacturing processing stages in cotton yarn manufacturing by using cotton fibers are shown in the process flow diagram.
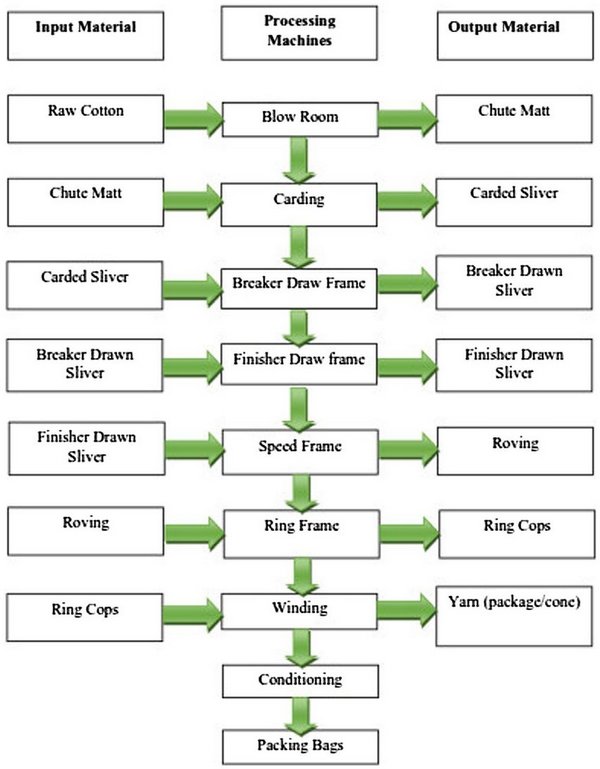
Table 01: Flow chart of cotton carded ring spun yarn.
Input materials | Process machines | Output materials |
Raw cotton | Blow room | Lap / Tufts |
Lap | Card | Carded Sliver |
Carded Sliver | Drawing 1 | Breaker Drawn Sliver |
Breaker Sliver | Drawing 2 | Finisher Drawn Sliver |
Finisher Drawn Sliver | Simplex | Roving |
Roving | Ring frame | Yarn |
Yarn | Auto winding | Yarn Cones |
Table 02: Flow chart of cotton combed ring spun yarn.
Input material | Process machines | Output materials |
Raw cotton | Blow room | Lap / Tufts |
Lap | Card | Carded Sliver |
Carded Sliver | Drawing | Drawn Sliver |
Drawn Sliver | Lap former | Mini Lap |
Mini Lap | Comber | Combed Sliver |
Combed Sliver | Drawing | Combed Drawn Sliver |
Combed Drawn Sliver | Simplex | Roving |
Roving | Ring frame | Yarn |
Yarn | Auto winding | Yarn Cones |
Table 03: Flow chart of cotton carded rotor spun yarn.
Input material | Process machines | Output materials |
Raw cotton | Blow room | Lap / Tufts |
Lap | Card | Carded Sliver |
Carded Sliver | Drawing | Drawn Sliver |
Drawn Sliver | Open End Rotor Machine | Yarn Cone |
Table 04: Flow chart of air jet spun yarn.
Input material | Process machines | Output materials |
Raw cotton | Blow room | Lap / Tufts |
Lap | Card | Carded Sliver |
Carded Sliver | Drawing 1 | Finisher Drawn |
Finisher Drawn Sliver | Air jet machine | Yarn Cone |
Processing steps of yarn manufacturing
Bale Opening
↓
Conditioning of MMF Fibers
↓
Blending
↓
Blow Room
↓
Carding
↓
Drawing 1
↓
Drawing 2
↓
Speed Frame
↓
Ring Frame
↓
Cone Winding
Here we simply discussed the whole yarn manufacturing process according to the flow chart of Yarn manufacturing Process Where natural and man made both will be covered.
At first spinning process is begun with converting highly compressed cotton in bales into the form of thoroughly loosened, opened and cleaned state. In a spinning mill, those steps of processing are carried out in the blow room. At the 1st stage of spinning are involved converting lightly compressed cotton bales into the form of opened and cleaned fiber flocks.
a. Blow Room:
In this process, the fibers in the bale form will be loosen, opened and cleaned. This blow room are the beginner stage of spinning Process.
b. Carding:
Carding is the most important operations in the spinning process.The carding is determined the special features of the yarn. As like: opening the tufts into individual fibres, eliminating impurities, selecting fibers on the basis of length, removal of neps, parallelizing and stretching of fiber, transforming the lap into a sliver.
c. Draw Frame:
Draw frame is the machine where drafting and doubling are carried out. Carded sliver is not even enough to produce to good quality yarns. Consequently, all the carded slivers are subjected to doubling and drafting on a machine is called Draw Frame.
d. Roving Frame or, Speed Frame:
The products are delivered by roving machines is called Roving. Roving is a fiber strand of lesser count than a sliver. It has a small twist to keep fiber together. It will wound on to a package that is suitable for feeding spinning machines. Robing frame Operation involved in three parts; these are:
- Drafting: To reduce the weight and unit length of sliver.It makes it suitable for ring spinning system
- Twisting: To insert small amount of twist to give required strength of roving
- Winding: To wind the twisted roving on to bobbin
e. Combing:
It is a process,where introduced into the spinning of finer and high-quality yarns. The carded materials contain certain amount of short and staple fibres, neps, fine kitty, leaf particles, etc. Short fiber is hindrance to spinning of finer counts.It causes the number of fibers in the cross section of the yarn is less. The short and staple fibers cause thick and uneven places in the yarn length and its looks like hairy. Apart from this, very short staple fiber doesn’t contribute anything to yarn strength. Staple fiber below a certain pre-determined length can easily separate out by using comber.
f. Ring Frame:
Ring spinning machine was invented in 1828 by American Thorp. It drafts the roving until the required fineness is achieved. Twisting drafted strand to form yarn of required count and strength. Winding the twisted yarn on to the bobbin helps to suitable storage and transportation process.
g. Cone Winding:
Cone winding is the final stage in Spinning. Good winding is the mirror of a spinning mill.It is very necessary process to understood very well by all the personnel handling the department. Winding are thus be viewed as simply being a packaging process, forming a link between the last few elements of yarn manufacturing processes.It is the first element of fabric manufacturing process.
2. Fabric Manufacturing:
Textile fabric has a two-dimensional structure produced by fiber or yarn interlacing. The interlaced fibrous structure is mainly classified as woven, nonwoven, and knitted.
A) Weaving:
Historically, the weaving technology was the primary source for fabric production. It’s the most commonly used technique of fabric manufacturing processes. The woven fabrics has a lot of application areas like apparel, home textiles, geo textiles, composites, medical, packing, seat belts, industrial products and so on.
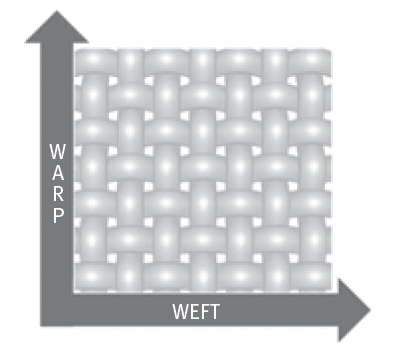
Woven fabric is produced by the basic weaves, such as plain, twill, and satin, and the fancy weaves, including pile, jacquard, dobby, gauze, etc. It’s produced by interlacement of two set of yarns perpendicular to each other. The first set of yarn includes the threads running lengthwise in the fabric. And the second is represented by the threads placed in width direction.
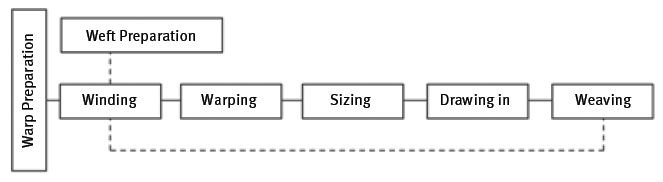
Brief of weaving process:
The flow chart shown a summary of the process steps from yarn to the final product, in example loom-state fabric is shown in fig. There the warp yarns are subjected to a number of processes, termed as warp preparation before conversion into fabric. While weft yarn doesn’t require any specific preparation. Mainly, warp preparatory process consists of the following operations: winding, warping, sizing and drawing-in.In spinning,yarns produced are used as input of the warp preparation. Winding are helped to prepare the yarn for a package that requires shape and size. Then weft yarn is provided to loom. While warp yarns are processed to give a sheet of yarns on warp beam by the process is called warping. A coating of size materials is applied to the yarn in the next process to impart strength. It makes the yarn smoother. Later, this warp sheet is drawn in from the droppers, heald frames and the reed. The primary fabric forming processes are carried out at the loom, where this warp sheet and weft are interlaced to give a woven fabric.
B) Knitting:
Knitting is the second largest fabric production technique used in the world after woven fabric. In knitting, yarns are interloped to make thick yet flexible and elastic fabric. Knitting is came from the Dutch word “Knutten”. Knutten means to knot. Knitting is defined in simple words as the interloping of yarn.
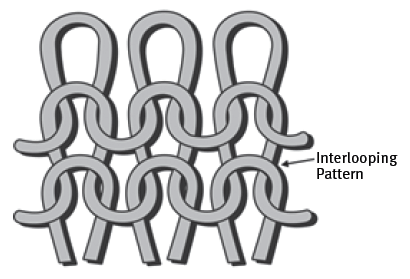
Knitting is fabric formation technique, where the yarn is bent into loops. Those loops are interconnected to form fabric shown in the fig. The bending of yarn provides better comfort, stretch-ability, extensibility, and shape retention properties. It has particularly a comfortable form of fabric structure for sports, casual wear, and also for undergarment. Knitted fabrics are included weft types warp types, raschel, and tricot.
C) Manufacturing of nonwoven:
In the 19th century, a textile engineer named Garnett realized that a large amount of fiber is wasted as trim. And then he developed a special carding device to shred this waste material back to fibrous form. This fiber had used as filling material for pillows. Later on, manufacturers in Northern England had begun binding these fibers mechanically and chemically into batts. These were the precursors of today’s nonwovens.
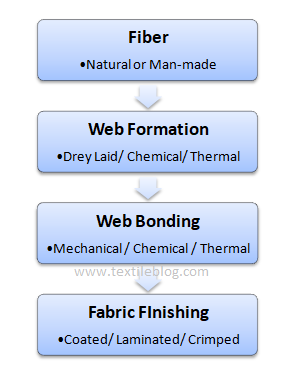
Nonwovens are considered as cheaper alternative of conventional textiles. It was generally made from carded webs using textile processing machinery. The nonwovens industry is very sophisticated and profitable. Nonwoven fabrics are also rapidly increased in market consumption. Non-woven fabrics are finding interesting uses in industrial and home applications. It includes materials produced by felting and bonding.
3. Textile Wet Processing:
Wet processing is important branch of textile engineering. It can be classified in four stages like pretreatment, dyeing, printing and finishing. In this process fabric is being comfort and user friendly. It is also called beautification process of fabric.
Flow Chart of Wet Processing
Fabric or, Yarn
↓
Singeing
↓
Desizing
↓
Scouring
↓
Bleaching
↓
Mercerizing
↓
Dyeing or, Printing
↓
Finishing
Steps of wet processing is described below:
a. Singeing:
Singeing is the first step of pre-treatment for textile dying where loosen, hairy and projecting fiber are removed by burnout.
b. Desizing:
In desizing process gummy starch material and size materials has been removed. The process increased the fabric absorbency and luster of the fabric dying and printing.
c. Scouring:
Scouring removed natural impurities such as: non-cellouse materials, oil, fat and wax.
d. Bleaching:
Bleaching is used to reduce natural color of the raw materials. Dyeing performance of fabric depends on the process bleaching.
e. Mercerizing:
Mercerizing is a special treatment; it performs when buyer wants. It’s an additional treatment to increase the strength and luster of the materials.
f. Dyeing or, Printing:
Dyeing is the main process white or grey fabric become decorated by different colors. Printing is known as localized dyeing. Printing gives a special appearance on colored or white fabrics.
g. Finishing:
Finishing is the last process of dyeing treatment. Different properties may be added to the finish fabric by different materials.
4. Apparel Manufacturing Process:
Apparel is a final product of textile which known as a piece of clothing. Apparel design and manufacturing is the combination of modern art and technology. Apparel manufacturing has seen several advancements in design development such as: computer-aided manufacturing (CAD) and automation.
However, the older version of garment manufacturing process is still the main method of apparel manufacturing process today. The method is cutting and joining of at least two pieces of fabric. The sewing machines are produced by joining woven or cut-knitted fabrics in this process.These machines are still based on the principal format used.
Apparel manufacturing flow chart
Design
↓
Pattern Making
↓
Fit Sample Making
↓
Production Pattern Making
↓
Grading
↓
Marker Making
↓
Fabric Spreading
↓
Fabric Cutting
↓
Cutting Parts Sorting or Bundling
↓
Sewing
↓
Apparel Inspection
↓
Apparel Ironing and Finishing
↓
Final Inspection
↓
Apparel Packing
↓
Cartooning
↓
Shipment
Various process of garment manufacturing are briefly described:
a. Design:
Design is usually provided by the buyer. Buyer send the technical sheet and art-work of an order to the merchandiser, after placing an order. Sometimes it made by fashion design section in the factory.
b. Pattern Making:
Pattern should be made by following the technical sheet and art-work. It’s done by both manually or, computerized method.
c. Fit Sample Making:
The main target of making a fit sample is to follow the details instruction about that garments style.
d. Production Pattern Making:
For bulk production, production pattern is made with allowance. Production Pattern Making is done by both manually and computer.
e. Grading:
Buyer suggests about the size ratio of that order during an order confirmation. Order are graded according to the buyer’s instruction.
f. Marker Making:
Marker is a very thin paper which contains all the parts of a particular apparel.It’s must be needed to make the cutting process easy.
g. Fabric Spreading:
To cut the fabric properly fabric is spread in cutting table.
h. Fabric Cutting:
Fabrics should cut according to marker. Fabric Cutting process is done by using manual method and computerized method.
i. Cutting Parts Sorting or Bundling:
Cutting parts has to sort out or make bundling. It is necessary to send these easily into the next process. This process is usually done by manually.
j. Sewing:
All the parts of an apparel are joined here to make a complete garment. Sewing process is mainly done by manually.
k. Apparel Inspection:
After completing sewing, inspection is done here to make fault free apparel. Apparel Inspection is done by using manual method. But now AI used in apparel inspection
l. Apparel Ironing and Finishing:
Apparel are treated by steam. It is also required finishing should be completed here. This process is done by manual method.
m. Final Inspection:
Complete apparel are inspected here according to the buyer’s specification.
n. Apparel Packing:
Complete apparel are packed here by using buyers instructed poly bag.
o. Cartooning:
All the garments should be cartooned by maintaining buyer’s instruction to minimize the damages of apparel.
p. Shipment:
After completing all the required processes,apparel finally send to the buyer via shipment processes.
Today the important topics in apparel manufacturing industry is product development, production planning, and material selection. The selection of apparel manufacturing and design are included computer-aided design, fabric spreading, fabric cutting, and sewing, joining techniques. The developments in the finishing, quality control, and care-labelling of apparel are meeting the point-of-sale requirements.
Technical Textile:
Technical textile is an established name of the interdisciplinary application of textile products. Most of the major industrial sectors are benefiting from the function of different fiber material.
Technical textile is a textile product which is produced for technical performance rather than fashion. Today, technical textiles occupied strong market consumption. It is an important sector for industrial development in industrialized and also for developing countries. There are 12 types of technical textile with example product application are provide below:
SL No. | Area | Application |
01 | Meditech | Bandages, sanitary diapers, sutures, mosquito nets, heart valves, ligaments, etc |
02 | Agro-Tech | Crop protection net, bird protection, water tank, etc. |
03 | Build-Tech | Ropes, tarpaulin, concrete reinforcement, window blind, wall covering, etc. |
04 | Mobile-Tech | Car airbags, car- aircraft seats, boat, seat belt, etc. |
05 | Pro-Tech | Protective gloves, knife and bulletproof vest, flame-retardant and chemical-resistant clothing, etc. |
06 | Indu-Tech | Conveyor belts, cordage, filtration media, etc. |
07 | Home-Tech | Sofa and furniture fabric, floor covering, mattresses, pillow, etc. |
08 | Cloth-Tech | Sun shade, parachute fabric, sewing threads, interlinings, etc. |
09 | Geotech | Nets for seashore and geo structures, mats, grids, composites, etc. |
10 | Pack-Tech | Tea bags, wrapping fabrics, jute sacks, etc |
11 | Sport-Tech | Sports shoe, sports nets, swimsuit, sleeping bags, sail cloths, etc. |
12 | Eco-Tech | Erosion protection, air cleaning, prevention of water pollution, waste treatment or recycling, etc. |
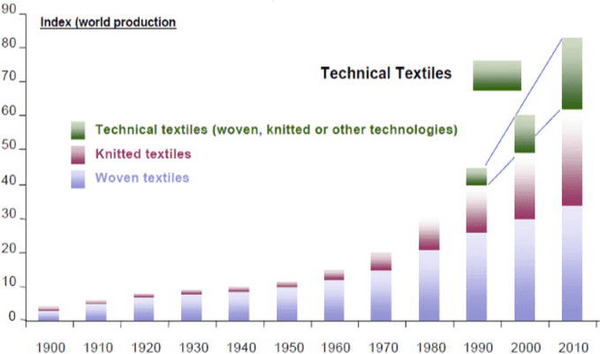
Value Addition in Textile Manufacturing Processes:
1. Pre-treatment process:
Any of fibrous substrate including fiber, yarn, fabric, apparel, technical textile, etc. may require a lot of chemical processing to reduce the undesired content from the fiber and fabric. The selection of any pre-treatment process methodology depends upon the end-use requirement of the textile product.
A pre-treatment process is need to introduce two important value additions in textile substrate including:
- Removing the undesired content from the fiber mass such as dust, lint, colouring matters, undesired oils, trash, etc.
- Imparting the required level of fiber property for following processing of textile substrate. The desired fibre property are: fabric whiteness,softness, absorbency, strength, weight, width, etc.
The pre-treatment processes are performed in the area of sizing, de-sizing, scouring, bleaching, mercerization, washing, and heat setting, in conventional textile industry. One or more processes are required for the textile impurities substrate depending upon the end use of the textile product.
2. Coloration process:
Dyeing, printing, and coating are the coloration processes.It produces beautiful motif and colour effect on textile products. Printing and coating can only apply to surface coloration. Approximately 10,000 different dyes and pigments are used in industry all over the world.
Dyeing is the colouring effect throughout the cross section of fiber. Its effects can be produced on any form of textile substrate including fiber, filament or yarn, fabric, garment. Dyeing of textile substrate is performed using the dyestuff such as: reactive, direct,pigment, sulphur, vat, acid, and disperse, it is mainly depending upon the dye-fiber system compatibility. The dyeing method are used as continuous, semi-continuous, and batching. Mainly,continuous dyeing method is used for large-scale production in the textile industry. Fixation of dyestuff in fabric might be significantly fast during the service life to provide resistance and durability against washing, soaping, heat, chemicals, rubbing, sunlight, etc.
3. Special finishing process:
All finishing processes is passed after bleaching, dyeing, or printing. All finishes are categorized based on:
- Durability: permanent, durable, semi-durable, non-durable.
- Application method: thermal, chemical, mechanical.
- Purpose: routine, aesthetic, functional.
Special finishing effects are required for functional purpose in textile fibers. Textile products are needed to exhibit a variety of performance effects for requirements of end use. Functional properties such as:flame retardant, water repellent, anti-bacteria, antistatic,crease recovery, moth proofing, softening, hand-builder and so. These are the special finishing effects that can be produced by special finishing process in textile.
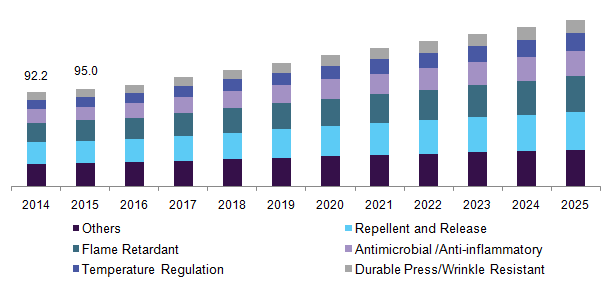
Environment and Textile Manufacturing Processes:
Various toxic chemical used in textile manufacturing processes are discharged effluent from dyeing, printing, and finishing processes. It is the undesired effects to environment and human lives. An estimation of the undesired effects to eco system associated with the major processing units of textile manufacturing industry.
Table: Water, energy and chemicals consumption in main processing sections of textile industry.
Process | Water | Energy | Chemicals |
Yarn production | 2% | 8% | 22% |
Fabric production | 10% | 8% | 12% |
Wet processing (dyeing/ printing/finishing) | 86% | 79% | 65% |
Garment production | 2% | 5% | 1% |
Total | 100% | 100% | 100% |
All the environmental elements such as air, water and soil, are seriously affected by the textile manufacturing processes from fiber production to final textile product. Therefore, necessary initiatives should be taken in the textile industry by the public and private partnerships to enhance the environment-friendly nature.
References:
- Introductory Chapter: Textile Manufacturing Processes by Faheem Uddin
- Textile Technology- An Introduction by Burkhard Wulfhorst and Thomas Gries
- Textiles, Twelfth Edition By Sara J. Kadolph and Sara B. Marcketti
- Manufacturing processes in the textile industry. Expert Systems for fabrics production by J. BullónPéreza, A. González Arrietab, A. Hernández Encinasc, and A. Queiruga-Diosc DOI: http://dx.doi.org/10.14201/ADCAIJ2017614150
- https://textilelearner.blogspot.com/2012/02/textile-manufacturing-process-process.html
- Yasir Nawab (Ed.) Textile Engineering De Gruyter Textbook
- https://garmentsmerchandising.com/flow-chart-of-garments-manufacturing-process/
- https://www.cottonworks.com/wp-content/uploads/2017/11/Textile_Yarns.pdf
- https://textilelearner.net/cotton-yarn-spinning-process/
Author of this Article:
Md. Mahedi Hasan.
B.Sc. in Textile Engineering
Textile Engineering College, Noakhali.
Email: mh18.bd@gmail.com