Generally, pressing or ironing is done in combination with heat, pressure and moisture. With the help of this process, fibers, yarns and fabrics are reformed in the wanted shapes as per the desire of the designer. The system of application of heat, pressure and moisture for the purpose of pressing depends on the garment pressing equipment and methods. But in garments industry, the works of heat and moisture are done mainly by steams or the work of pressure is done by mechanical or by manual system. If pressure is applied manually, then it is almost impossible to keep the uniformity of pressure but the uniformity of pressure can be maintained properly by the use of mechanical system.
Garments may of various types and various types of pressing are given in various types of garments. Various types of garment pressing equipment / machines are used for pressing of various types of garments. Because, pressing of all kinds of garments cannot be done by one kind of pressing machine. In some garments factories, multiple types of pressing machines are used for getting pressing of desired quality comparatively at small expense.
Types of Garment Pressing Equipment and Methods:
About the equipments or pressing machines that are used for pressing of garments, elaborate discussions are given below.
1. Iron:
In ancient times, heat were generated firing the coal or the wood in an iron made case and garments pressing or ironing were done under the smooth and hot surface of the case. With the passage of time, the use of the iron case has been replaced by the use of electricity, which (electric iron) is being used in houses till now. In electric iron, regulator is used to control temperature. Presently, steam iron, one step forward edition of electric iron, has come in the market. By supplying steam in the steam iron, the iron is made hot. By controlling a button in the steam iron by finger, the supply of steam through the iron is regulated. Steam is supplied in the iron through a pipe from the central large boiler or mini boiler and by operating the switch in the iron, steam is made out through a number of holes placed at the bottom of the iron. The shape of the iron is generally triangular and the weight may be from 1 kilogram to 15 kilogram.
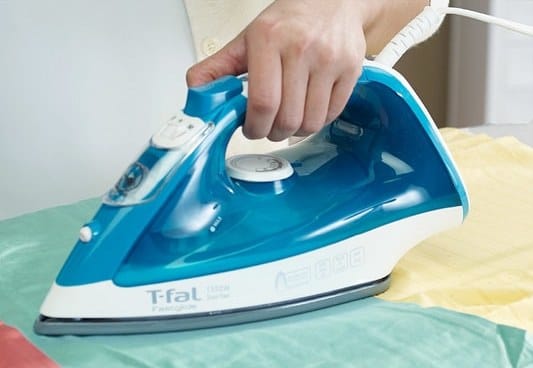
Ironing bed or table is required for calendaring of garments with the help of iron. For electric iron, generally flat bed or shaped bed can be used but for steam iron, ironing bed having facility of air-suction is required. Just after ironing bed, the heat and moisture of the calendared portions of the garment are removed instantaneously. As a result, the possibility of unwanted crease in the garments becomes less and the fabric dries quickly, moreover, the high quality pressing can be done comparatively in high speed. The dimension and shape of ironing bed may be of various types. If the ironing bed of special shapes are used, the ironing of the specific parts of a garment can be done very nicely and rapidly.
Very skilled operator is required for ironing of garments by steam iron with air-suction facility. Because, the measuring of the suction of steam and air and their proper use depend on the skill and honesty of the operator.
2. Steam Press:
There is a static buck and a head in the steam press whose shapes are proportionate to each other. Keeping the garment on the buck, the head is placed on the buck and the garment is ironed by applying heat and pressure. The buck is set in a frame and the ironing bed is made by spreading a few layers of fabrics or foam on the buck. There is system of the flow of steam and air-suction through the buck. There are tables around the buck where the garments are kept. The head remains in a frame on which bedlike arrangement is made by a number of layers of fabrics or foam. There is arrangement for supply of steam also through the head. Generally, the head is brought down on the buck with the help of scissors action and pressure is applied.
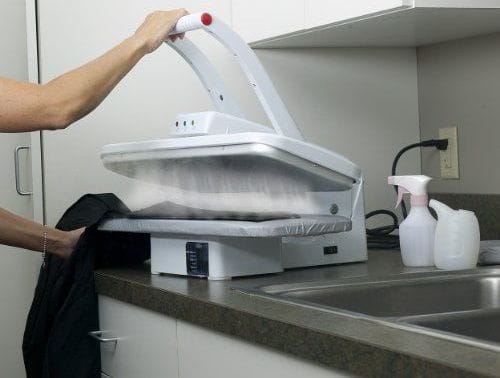
In the old pressing system, the head is brought down on the buck by a foot operated switch and pressure is applied by the scissors action and by another switch operated by hand or by foot, steam is supplied through the head and buck. Finally, the head is brought upward by controlling another switch and air is sucked through the buck.
In modern and automatic steam press machine, all jobs are done automatically in cyclic order by switching only once. Specially how much amount of pressure the head will apply by coming down on the buck, how much time will supply the steam and then the head will go upward from the buck, how much time the air will be sucked through the buck etc. can be given pre-setting and if requires, they can be changed also. In the old system of garments pressing, skill operator is required, because, it is very difficult to maintain that when and what switches are to be controlled regularly and properly. On the otherhand, as the jobs are performed in cyclic order in the modern steam press, the job of operating of the machine is comparatively easy.
You may also like: Alternative Methods of Joining Fabric
The head and the buck are generally covered by the silicon coated cover of polyester or nylon fabrics, which in need of time, can easily be removed and cleaned. The shape of the head and the buck may be of various types, these heads and bucks of special shapes are used for pressing of jacket and trousers. Because, it is convenient to press these garments very beautifully and rapidly.
In ultra-modern steam press, there are one head and a number of bucks. Both the head and the bucks are accelerated. In this situation, when the head continues to pressing, among the other two bucks, garments loading is done in one and the just pressed garments are removed to the other. This type of press helps in production by making vertical movement of the head.
3. Steam air finish:
This type of garments pressing machine is mainly known as “Puffer” or “Dolly” press. In Dolly press, there is a form in the frame in which arrangement is there for flowing of steam and compressed air with the help of a pipe. The pressing form is generally made by coarse canvass fabric. The size of the pressing form is used as per the size of the body of the garments, but there are no sleeves. Timer is used for flowing of steam and air for pre-setted time. An operator, covering from the upper side of the pressing form, pull downs a garment. Then steam is flowed from inside the pressing form with the help of a pipe, as a result, both the pressing form and the garment swell up. This way, steam is flowed for first 8 seconds. Then hot air is flowed for the next 8 seconds.
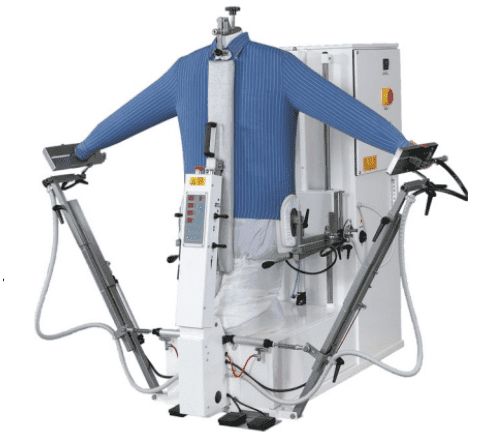
As the outcome of garments pressing this way, if any unwanted creases are there in the garments, they are easily removed. Also minimum time is required for garments pressing. A padded clamp is used along the button hole lines so that during pressing the holes are not de-shaped. During pressing of the garments made with knitted fabrics in these machines, special care should be taken so that the volume of the garments is not stretched. In dolly pressing, there is no system of giving any creases in the garments but if any creases are required then it is done by hand iron or by steam press. For the purpose of pressing of garments of various sizes, the pressing forms of similar sizes are used.
Dolly press is generally used for pressing of t-shirts, blouses, night dresses, sports wears etc. but dolly press can also be used for pressing of jeans shirts, pants, jackets etc.
4. Steam Tunnel:
In this process, pressing is done without applying any pressure on the garments. Hanging the garments in hangers, the hangers are placed in the running rail. The running rail carries the hangers with garments through a tunnel. There are a number of chambers in the tunnel. In the first chamber, the required temperature is controlled by steam. During passing through the chamber, the garments hanging in the hangers are heated by steam and if there is any unwanted creases in the garments, they are removed due to the fabric relaxation causes by heat and for the pulling of the gravitation force. Then during the period of passing through the second chamber, the garments are dried by the flow of dry hot air.
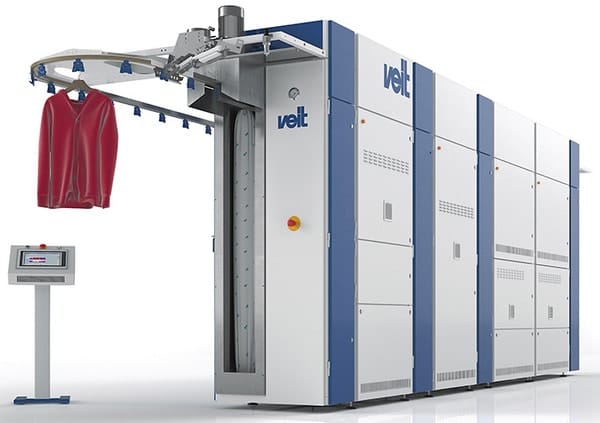
In this process, if there is any crease in the garments, they can be removed, but no creases can be created in the garments. Generally, steam tunnel is used for pressing of t-shirts or garments made with knitted fabrics.
In this article I only discuss common garment pressing equipment those are generally used in apparel industry. But there are more garment pressing equipment are used in home and industry. If your factory use other pressing machine then tell us in bellow comment.