Warping Process:
We know that woven fabric is made by two sets of yarn; warp and weft. Warp yarns run with along the length of fabric and weft yarns go across the width of the fabric. Warping is the preparation of yarn to weave fabric. It is the transfer of many yarns from the creel of single packages to a beam. The yarns will form a parallel sheet of yarn wound onto the beam. The basic objective of warping is to built a package where yarn ends remain in uniformly set parallel & continuous form & there by to accelerate the next process either sizing or drawing-in.
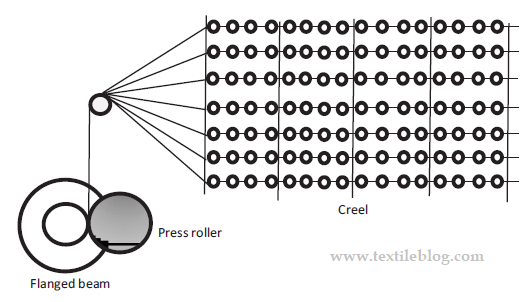
Objectives of Warping:
The main objective of warping is to prepare a warp sheet of desired length containing a desired number of yarns that are wrapped on a flanged barrel in such a manner that tension in each yarn and density of yarn mass in the cylindrical assembly are maintained within a given tolerance level throughout the wrapping of the warp beam. By warping process yarn quality increase, wound up fixed length of yarn on weavers beam. Increase the weavability of yarn. In this process small packages can re-use. After all increase the production. The process of warping is dedicated to the conversion of cones into a beam of given specifications.
Types of Warping:
There are two types of warping are popular in textile industry for preparing warp yarn for power driven high speed looms or hand looms. These are:
- Direct Warping or Beam warping
- Sectional Warping
Direct Warping or Beam Warping:
When the yarns are drawn from the single packages on the creel directly onto the beam then it is called direct warping. It is also called high speed warping or beam warping. Direct warping is used to make smaller beams which are combined later in slashing to produce the weaver’s beam. Direct warping is used to manufacture greige towels; that will be dyed or full bleached during wet processing. Modern beam warping machines have creels with moveable trolleys. The trolleys are movable so that cones can be creeled in reserve when one set is working in the machine.
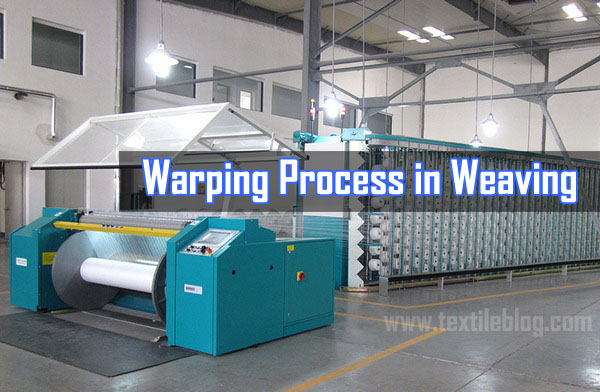
Sectional Warping:
When the yarn is wound onto the beam in sections starting with the tapered end of the beam then it is called sectional warping. Sectional warping is used for weaving of towels containing stripes. Multiple color of yarn can be incorporated in the weavers beam by using sectional warping. The drum of the beam has a cone which has a slight angle that will prevent the yarns from slipping off. Sectional warping is important if for making a yarn dyed striped towel.
Without these direct and sectional warping there are also used draw warping and ball warping method.
Draw-warping:
A process in which a number of thread lines, usually 800 to 2000 ends of POY feedstock, are oriented under essentially equal mechanical & thermal conditions by a stretching stage using variable speed rolls, then directly wound onto the beam. Draw warping process gives uniform end-to-end properties.
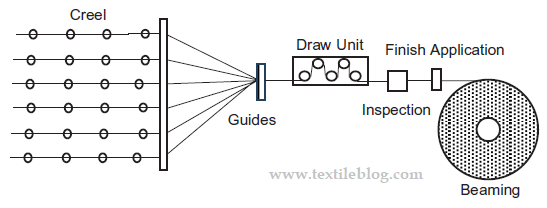
Ball warping:
Ball warping is the process in which warping is performed in rope form on to wooden ball. It involves creeling multiple ends of yarn (Between 350 and 500 ends) and collecting them into an untwisted rope for dyeing. The rope is wound onto a long cylinder called a log on a machine called as a ball warper.
Warping Procedure:
The flow chart of warping is given bellow:
Flow Chart For Warping:
Creeling
↓
Denting
↓
Empty Beam Feeding
↓
Warping
↓
Leasing
↓
Ends Cutting
↓
Doffing
Warping Operation:
Warping procedure for terry towel is not at all different from the warping procedure of traditional weaving. The warping procedure is described bellow in brief.
- The first operation of warping is crealing; i.e. to feed the empty cones in the creel. Among different types of creel the V-Creel is mostly used.
- Then the yarn ends passes through the dents of the comb of the reed. This is known as denting.
- Then the yarns from the cones are wrapped on to an empty beam.
- As the warp beam wraps a predetermined amount of yarn; a lease yarn is inserted that helps to separate each yarn from each other during sizing.
- Finally the full beam is doffed out from the m/c.
In this process direct warping is done.
What warping should do?
- To form from a predetermined number of single end packages, a continuous sheet of yarn of specified length & width.
- The individual yarn ends of the sheet should be spaced uniformly across beam’s full width.
- All the yarn ends in the sheet should be wound at almost uniform tension.
- The density of wound yarn beam should be uniform across the width & from start to end of winding the sheet.
Problems in Warping:
Following are some of the normal problems during warping:
- Variation in tension within and between beams.
- Missing ends.
- Cross ends.
- Poor quality of beam preparation.
- Production loss due to some cones running out early.
- Pattern not proper.
- Lost end.
- Section mark.
- Draw back.
References:
- Handbook on fabric manufacturing by B. Purushothama
- Industrial Practices in Weaving Preparatory by Mukesh Kumar Singh
- Textile Engineering – An Introduction Edited by Yasir Nawab